Executive Summary
Map Ta Phut Olefins Co. Ltd., Rayong, Thailand
Map Ta Phut Olefins Company Limited (MOC), SCG Chemicals's subsidiary, operates a newly completed petrochemical complex at the Map Ta Phut Industrial Estate in Thailand's Rayong province. The complex produces 900,000 tpa of ethylene and 800,000 tpa of propylene, which is used in downstream plants to produce 400,000 tpa of high density polyethylene (HDPE) and 400,000 tpa of polypropylene.
Functioning for the first time as a main automation contractor (MAC), Yokogawa Thailand worked closely with the EPC contractor to deliver a comprehensive control and instrumentation solution for this greenfield project. This included the CENTUM VP production control system (PCS); the ProSafe-RS safety instrumented system (SIS); process gas chromatographs; analyzers; an advanced analytical instrument management system (AAIMS™); HART differential pressure transmitters, temperature transmitters, and flowmeters; InsightSuite AE asset excellence services; an Exaplog event analysis package for alarm reduction; and the Exasmoc advanced process control package.
The Challenges and the Solutions
1. Project execution
In such a large greenfield project, it is important to start engineering and determine the basic specifications at an early stage. As the MAC, Yokogawa Thailand proceeded from front end engineering design (FEED) to the engineering phase, then undertook configuration & implementation, staging, and startup & commissioning. By executing this project as the MAC, Yokogawa Thailand was able to effectively manage the overall project schedule and reduce maintenance costs by maintaining consistency in the specifications.
2. Safety and efficiency
The CENTUM VP PCS and ProSafe-RS SIS were integrated using the same engineering environment. This reduced the overall engineering costs and resulted in a system that operates smoothly and efficiently. The PCS and SIS faceplates have the same look & feel, and security measures are in place that restrict access to the SIS faceplate.
The ethylene plant has multiple crackers and decoking is essential to maintaining efficient ethylene production. The InsightSuite AE analysis package calculates an optimum decoking algorithm that is used to optimize steam consumption, for greater efficiency and improved plant safety.
3. Asset maximization
To manage the more than 5,000 Yokogawa field instruments installed throughout this large complex, MOC opted for a remote monitoring solution based on Yokogawa's PRM plant asset management package that reduces the maintenance workload for field technicians and generates summary reports for future reference. This is backed by InsightSuite AE services that work 24/7 to identify issues and implement corrections that improve both availability and performance rate and reduce maintenance costs over the entire plant lifecycle.
The olefins plant has approximately 20 critical safety valves that are rated for SIL levels 1, 2, and 3, and they need to be checked periodically to determine that they are in correct working order. PRM's partial stroke test (PST) function allows these tests to be run from the control room, eliminating the need for technicians to go to each device to manually check its operation. This reduces workload and ensures safety.
4. Analyzer maintenance and data acquisition
Nearly 60 gas chromatographs and a large number of other types of analyzers in several analyzer houses are utilized throughout this petrochemical complex. An AAIMS is used to monitor, evaluate, and improve the performance of these on-line analyzers in a cost-effective manner. An AAIMS executes statistical analyses for analyzer validation; calculates validation KPIs such as availability rate, breakdown rate, checking rate, reproduction rate, and standard deviation; and generates SQC validation, maintenance, and key performance reports. An AAIMS has the following benefits:
- A flexible and reliable tool that centralizes the monitoring and management of analyzers
- Automates the collection of analyzer data in real time from the PCS, through an OPC server
- Automates the analyzer validation process
Working at an AAIMS workstation, operators, QMI personnel, and maintenance personnel can also manually enter and edit data like sample test results and maintenance records.
The information on gas chromatographs and other types of analyzers that is gathered with this system can play an important role in maximizing the efficiency of plant operations.
Customer Satisfaction
Witoon Pradubsripetch, the olefins production manager at the MOC complex, said, "We are striving to operate this plant safely and efficiently, and to make maximum effective use of all assets. That's why we are using field digital technology with FDT/DTM, PRM, and AAIMS. We have started using ISA 100 wireless devices at our raw material tank yard. All systems in this plant are integrated in the central control room. Our operators can clearly see everything that is happening in the plant. They know the status of each operation and have all the information they need to make correct and timely decisions. We appreciate the support given to us by Yokogawa Thailand."
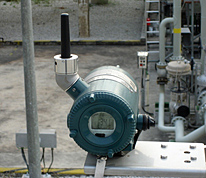
Wireless transmitter
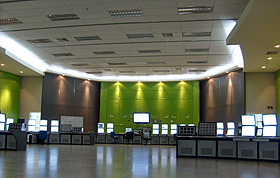
Central control room
相关行业
相关产品&解决方案
-
CENTUM VP
CENTUM VP具有简单而通用的架构,由人机界面、现场控制站和控制网络构成。
-
SIS (SIL3) ProSafe-RS
ProSafe-RS是获得德国认证机构(TÜV)认证的安全仪表系统,符合IEC 61508中确定的安全完整性等级(SIL)3。它已经在2400多个项目中安装使用,涵盖从大型集成过程自动化项目到独立解决方案等多种项目类型。
-
安全仪表系统 (SIS)
安全仪表系统 (SIS) 可保护人员、环境和资产。横河电机的SIS和相关安全解决方案被广泛应用于紧急停车、火灾与燃气、燃烧器管理和HIPPS等领域。
-
工厂资源管理系统(PRM)
工厂资源管理系统(PRM)是横河电机用于资产管理的一个关键平台。该平台旨在改进操作和维护,通过获得更大的可预测性,使工厂资产的可靠性和可用性增强。
-
报警分析(Exaplog)
新的Exaplog事件分析软件包有利于对DCS事件日志中的问题进行定量分析。通过报警设定调整和操作序列整定进行交替分析,可以持续提高生产效率。
-
现场提升等级
具有丰富经验的横河电机专业负责人参与这个过程的所有阶段。横河电机的咨询服务,可以帮助客户制定一个满意的迁移和提升等级的策略。
-
集散控制系统(DCS)
横河电机的集散控制系统(DCS) 可实现工业过程的自动化和控制,并提高业务绩效。30,000多套系统的经营者选择采用横河电机的DCS来实现其生产目标。