Executive Summary
Olefins Company Limited (MOC), a SCG Chemicals' subsidiary, produces 900,000 tpa of ethylene and 800,000 tpa of propylene, which is used in downstream plants to produce 400,000 tpa of high-density polyethylene (HDPE) and 400,000 tpa of polypropylene.
Functioning as a main automation contractor (MAC), Yokogawa worked closely with the EPC contractor to deliver a comprehensive control and instrumentation solution for this greenfield project. This included the CENTUM VP production control system (PCS); the ProSafe-RS safety instrumented system (SIS); process gas chromatographs; analyzers; an advanced analytical instrument management system (AAIMS™); HART differential pressure transmitters, temperature transmitters, and flowmeters; InsightSuite AE asset excellence services; an Exaplog event analysis package for alarm reduction; and the Exasmoc advanced process control package.
The Challenges
Yokogawa worked closely with the EPC contractor to deliver a comprehensive control, safety/alarm system, and instrumentation solution for this greenfield project.
The Solutions
1. Project execution
InIn such a large greenfield project, it is important to start engineering and determine the basic specifications at an early stage. As the MAC, Yokogawa proceeded from front end engineering design (FEED) to the engineering phase, then undertook configuration and implementation, staging, and startup and commissioning. By executing this project as the MAC, Yokogawa was able to effectively manage the overall project schedule and reduce maintenance costs by maintaining specifications consistency.
2. Safety and efficiency
The CENTUM VP PCS and ProSafe-RS SIS were integrated using the same engineering environment. This reduced the overall engineering costs and resulted in a system that operates smoothly and efficiently. The PCS and SIS faceplates have the same look and feel, and security measures are in place that restrict access to the SIS faceplate.
The ethylene plant has multiple crackers and decoking is essential to maintaining efficient ethylene production. The InsightSuite AE analysis package calculates an optimum decoking algorithm that is used to optimize steam consumption for greater efficiency and improved plant safety.
3. Asset maximization
To manage the more than 5,000 Yokogawa field instruments installed throughout this large complex, MOC opted for a remote monitoring solution based on Yokogawa's PRM plant asset management package that reduces the maintenance workload for field technicians and generates summary reports for future reference. This is backed by InsightSuite AE services that work around the clock to identify issues and implement corrections, improving both availability and performance rate and reduce maintenance costs over the entire plant lifecycle.
The Olefins plant has approximately 20 critical safety valves that are rated for SIL levels 1, 2, and 3, and they need to be checked periodically to determine if they are working correctly. PRM's partial stroke test (PST) function allows these tests to be run from the control room, eliminating the need for technicians to go to each device to manually check its operation. This reduces workload and ensures safety.
4. Analyzer maintenance and data acquisition
Nearly 60 gas chromatographs and many other types of analyzers in several analyzer houses are utilized throughout this petrochemical complex. An AAIMS is used to monitor, evaluate, and improve the performance of these on-line analyzers in a cost-effective manner. An AAIMS executes statistical analyses for analyzer validation; calculates validation KPIs such as availability rate, breakdown rate, checking rate, reproduction rate, and standard deviation; and generates SQC validation, maintenance, and key performance reports. An AAIMS has the following benefits:
- Centralizes the monitoring and management of analyzers in a flexible and reliable tool
- Automates the collection of analyzer data in real-time from the PCS through an OPC server
- Automates the analyzer validation process
- Allows manual entry and data editing like sample test results and maintenance records when operators, AMI personnel, and maintenance personnel work at an AAIMS workstation
The information on gas chromatographs and other types of analyzer that is gathered with this system can play an important role in maximizing the efficiency of plant operations.
Customer Satisfaction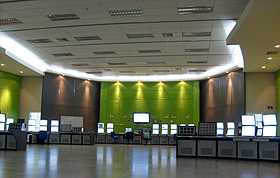
Witoon Pradubsripetch, the Olefins production manager at the MOC complex, said, "We are striving to operate this plant safely and efficiently, and to make maximum effective use of all assets. That's why we are using field digital technology with FDT/DTM, PRM, and AAIMS. We have started using ISA 100 wireless devices at our raw material tank yard. All systems in this plant are integrated in the central control room. Our operators can clearly see everything that is happening in the plant. They know the status of each operation and have all the information they need to make correct and timely decisions. We appreciate the support given to us by Yokogawa."
Related Industries
-
Petrochemical
- Diverse needs of petrochemical companies’
- Improve quality, productivity
- Yokogawa tailor-made solutions, long and wide-ranging experience in this field
-
Chemical
Chemical plants rely on continuous and batch production processes, each posing different requirements for a control system. A continuous process calls for a robust and stable control system that will not fail and cause the shutdown of a production line, whereas the emphasis with a batch process is on having a control system that allows great flexibility in making adjustments to formulas, procedures, and the like. Both kinds of systems need to be managed in available quality history of product, and to be able to execute non-routine operations. With its extensive product portfolio, experienced systems engineers, and global sales and service network, Yokogawa has a solution for every plant process.
Related Products & Solutions
-
Alarm Analysis (Exaplog)
The new Exaplog event analysis package facilitates the quantitative analysis of problems in the DCS event log. By alternating analysis with alarm setting adjustment and operation sequence tuning, you can continuously improve operational efficiency.
-
CENTUM VP DCS
Enhance productivity and optimizes processes
-
Distributed Control System (DCS)
Maximize performance and profitability
-
Field Upgrade
Yokogawa’s specialists are experienced in all phases of this process. Through its consulting service, Yokogawa can help you come up with optimal migration and upgrade strategies.
-
Plant Resource Manager (PRM)
- Plant manager software
- Properly manage facility for highly reliable, stable plant operation
- PRM contributes to quality of maintenance plans and optimizing maintenance costs throughout plant life cycle
-
SIL1/2/3 ProSafe-RS
- ProSafe-RS Yokogawa
- Control system integration
- Dual architecture in every module
- SIL3-level protection and high reliability
-
Safety Instrumented System (SIS)
Safeguard your plant with our industry-leading safety instrumented systems, designed to prevent unnecessary shutdowns, improve asset performance, and enhance operator effectiveness.