Waste disposal presents an ever-growing challenge in urban areas. Waste-to-energy (WTE) technology provides an environmentally sound solution to this problem that also addresses the growing need for alternate energy sources. Over 150 waste-to-energy plants and other types of waste incineration facilities all over the world rely on a Yokogawa control system solution. Yokogawa measurement and control technologies thus play a key infrastructure role in making our world cleaner and more efficient.
Challenges
Customer Challenge
Each customer has its own challenge to optimize the plant operation and maintenance depending on plant type, fuel, the country’s regulation and so on.
Solution
Based on the customer’s request and feasibility study, our experts in waste-to-energy and biomass provides engineered solutions to improve operation and maintenance of the plant.
Enabling Technologies
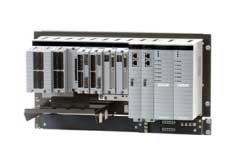
CENTUM VP Distributed Control System
The CENTUM VP integrated control system secures interruption-free “uptime only” plant performance for optimal productivity and profitability in the renewable energy field.
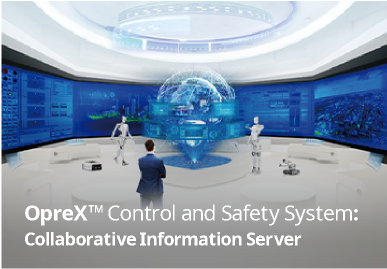
Collaborative Information Server (CI Server)
Yokogawa CI Server allows immediate improvement to production efficiency through digital transformation and reduction of operational maintenance whilst building a digital transformation framework.
Customer Challenge
Boiler slagging and fouling are one of the most common causes of maintenance headaches.
Solution
Yokogawa and Dublix Technology provide DD-Jet, an online boiler cleaner with turning water jets with a unique patented rotating nozzle cleans the boiler during full-load operation of the incinerator. The water-to-steam expansion provides a pressure wave, which is highly efficient to remove the fouling on the boiler surface. The system improves the efficiency of the furnaces and reduces the frequency of off-line maintenance. In addition, the DD-Jet system decreases the flue gas temperature at boiler outlet typically by 60 ℃, which reduces boiler corrosion.
Enabling Technologies
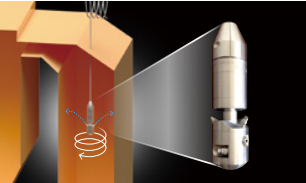
The DD-Jet is an on-line cleaning system for the radiation passes of boilers, found in waste-to-energy incinerators and biomass combustion plants. The system is installed on more than 40 waste-to-energy plants in Europe and Asia.
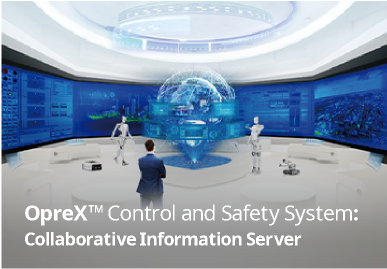
Collaborative Information Server (CI Server)
Yokogawa CI Server allows immediate improvement to production efficiency through digital transformation and reduction of operational maintenance whilst building a digital transformation framework.
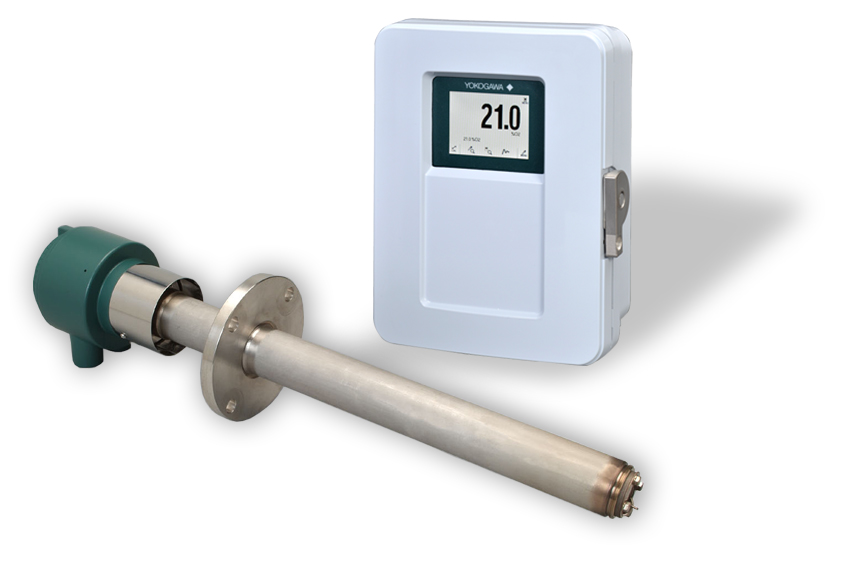
Yokogawa’s ZR analyzers are used for combustion monitoring and control applications and are relied on by a wide range of industries to optimize combustion and reduce NOX emissions.
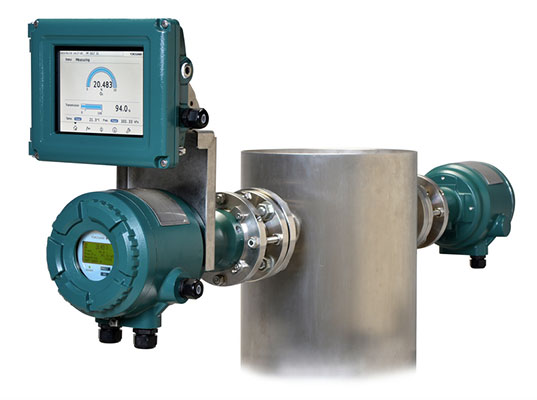
The TruePeak TDLS gas analyzer relies on a proprietary peak area integration method and is ideal for in-situ analysis in harsh process environments. It significantly improves the efficiency of boiler operations.
Customer Challenge
Minimizing the difference between the planned load and the actual amount of waste loaded into an incinerator. The actual amount depends on the waste type and condition.
Solution
The human interface station (HIS) for the Yokogawa CENTUM distributed control system (DCS) displays a trend graph in which curves are plotted indicating the planned and actual (cumulative weight) incinerator load. If there is any divergence from the planned load, the operator can adjust the stoker speed accordingly.
Enabling Technologies
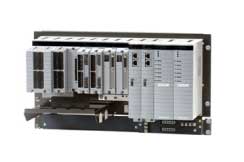
CENTUM VP Distributed Control System
The CENTUM VP integrated control system secures interruption-free “uptime only” plant performance for optimal productivity and profitability in the renewable energy field.
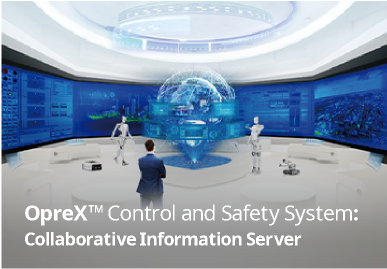
Collaborative Information Server (CI Server)
Yokogawa CI Server allows immediate improvement to production efficiency through digital transformation and reduction of operational maintenance whilst building a digital transformation framework.
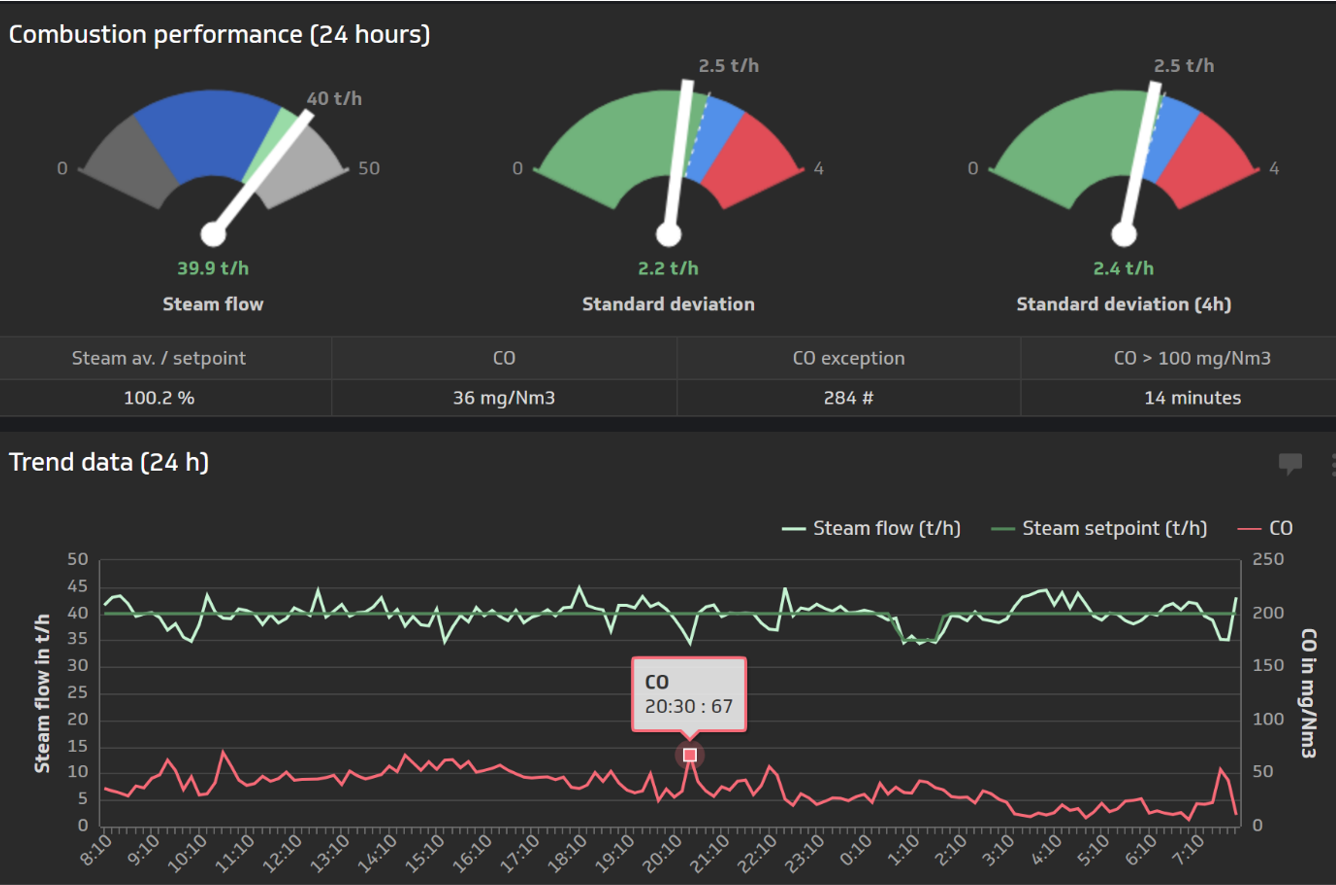
The FuzEvent is a high-performance advanced combustion control software that uses proprietary predictive control technology and leverages the company’s process know-how. Based on historical operating data and analysis of operating procedures carried out by experienced personnel, this software enables operators to keep plants operating at optimal efficiency 24/7. By ensuring a stable supply of steam and maximizing its use, the software helps to improve generation efficiency, reduce the likelihood of unplanned shutdowns, increase combustion capacity, and improve profitability for the plant operator. The emissions of NOx and other harmful gases due to incomplete combustion are also reduced.
Details
Waste to Energy Process
Waste delivered to an incineration facility is dumped into a pit and then transported by crane to the incinerator. The waste is burned and the remaining ash is collected at the bottom of the incinerator. The combustion heat can be used in district heating systems, water heating systems for swimming pools, and other applications, as well as to heat a boiler that produces steam. The steam drives a turbine that generates electricity. The exhaust gas passes through a cooling tower and dust collector before being discharged through the stack.
Control and Measurement Technologies
Plant-wide Systems and Instrumentation | ||
---|---|---|
Information
|
Control
|
Measurement
|
Processes | ||
Waste Unloading | Boiler | Turbine |
|
|
|
Flue-Gas Treatment | ||
|
Resources
- Modern waste to energy facility in UK uses CENTUM CS 3000 and ProSafe-RS
- Lakeside exports at least 34MW per hour to the country's national grid
- Italian waste to energy plant turns to CENTUM, PRM and FOUNDATION fieldbus solution
- Nearly 1500 FOUNDATION fieldbus devices are monitored and managed using the PRM
- A robust and reliable integrated control and safety system (ICSS) made up of the CENTUM CS3000 PCS and the ProSafe-RS SIS ensures safe operations while fully automating key processes.
- A variety of analytical instruments accurately measure the concentrations of key components, and this data can be monitored and controlled by the Yokogawa PCS.
The automation suppliers that will be successful in the long term will be those that effectively address application or industry specific problems for end users with a value proposition that cannot be ignored. These problems exist throughout the process industries today, and they won't be solved by simply offering a product, but through a combination of hardware, software, services, application expertise, and knowledge.
- Biofuel
- Biomass Power
- Chemical
- Drinking Water Treatment
- Energy Transition
- Geothermal Power
- Iron & Steel
- Offshore (FPSO FLNG & FSRU)
- Oil & Gas
- Oil & Gas Downstream
- Petrochemical
- Pharmaceutical
- Pipeline
- Power
- Pulp & Paper
- Refining
- Thermal
- Upstream
- Waste to Energy
- Wastewater Treatment
- Water & Wastewater
In ARC's view, customers need a compelling business value proposition to justify investment in any kind of automation. Vigilance and VigilantPlant were created with this in mind. Yokogawa's vision with VigilantPlant is to create an environment where plant personnel and operators are well informed, alert, and ready to take action.
- Biofuel
- Biomass Power
- Chemical
- Drinking Water Treatment
- Energy Transition
- Geothermal Power
- Iron & Steel
- Offshore (FPSO FLNG & FSRU)
- Oil & Gas
- Oil & Gas Downstream
- Petrochemical
- Pharmaceutical
- Pipeline
- Power
- Pulp & Paper
- Refining
- Thermal
- Upstream
- Waste to Energy
- Wastewater Treatment
- Water & Wastewater
Yokogawa has come a long way in making its message clear to the world of process automation. Last year, the company embarked on a full-scale global marketing campaign to make customers aware of the company's focus on system reliability, security, dependability, and robustness. Dubbed "Vigilance", the campaign created a unified message for the company and greatly helped expand awareness of the Yokogawa brand and corporate philosophy.
Process automation end users are under more pressure than ever to do more with less. The current economic climate means that many automation capital projects are on hold. With capital budgets tighter than ever, users instead focus on operational budgets (where cost cutting is also a key concern), or on automation investments with a very rapid return on investment.
In today's dynamic industrial marketplace, the only constant is change. Raw material costs, energy costs, market demands, environmental and safety regulations, technology, and even the nature of the labor force itself are constantly changing, and not always in predictable directions.
Videos
News
-
Press Release | Corporate Jun 5, 2024 Yokogawa Acquires BaxEnergy, a Provider of Renewable Energy Management Solutions
- Proven results across 120 GW+ of renewable energy operations in over 40 countries -
-
Press Release | Projects Oct 23, 2023 Yokogawa Completes Installation of High-Performance Combustion Control Solution at Poland's Largest Waste-to-Energy Plant
- Increases waste incineration volume by 5,500 tons annually if operated at full capacity -
-
Press Release | Projects Oct 7, 2014 Yokogawa Wins Control System Order for a Waste-to-Energy Facility in Cornwall, U.K.
Looking for more information on our people, technology and solutions?
Contact Us