To ensure the preservation of milk quality and prevent degradation, efficient monitoring of milk silo levels in a centralized location is crucial.
Introduction
The milk factory has a large capacity silo to store raw milk and intermediate products during processing and packaging of dairy products. To keep them fresh in silos and to prevent deterioration, it is necessary to continuously monitor the level and temperature in the silo.
|
![]()
Figure 1. Silos at a milk factory. |
Expected Benefits
-
Centralized management of raw materials in the siloStrengthens operational flexibility
-
Level monitoring with wireless
-
Simplifies data acquisition
-
No communication cables and power cables
-
Reduces maintenance costs
-
High-precision measurement is possible by utilizing the Yokogawa DPHarp
-
Enhances reliability
-
It is easy to expand the network in the future to add more measurement points
-
Simplifies expansion
Process Description
- The end-user wanted to build a remote system to continuously monitor levels in many silos.
- To preserve the freshness of raw materials, it is necessary to use the same quantities in all silos. Therefore, it is necessary to keep a record of the level in each silo.
- Currently, the level is recorded twice daily, manually, but it takes time and manpower and there is a risk of recording bad data.
Application Solutions
- By connecting a Yokogawa FN 310 Multiprotocol Module and FN 120 Communication Module to the HART transmitter installed in each silo, it is possible to transmit the process variable value and self diagnostic information with ISA 100 Field Wireless.
- The paperless recorder logs the data transmitted from the wireless devices.
- The paperless recorder can be accessed from the user's LAN environment, and it is possible to continuously monitor with a web browser.
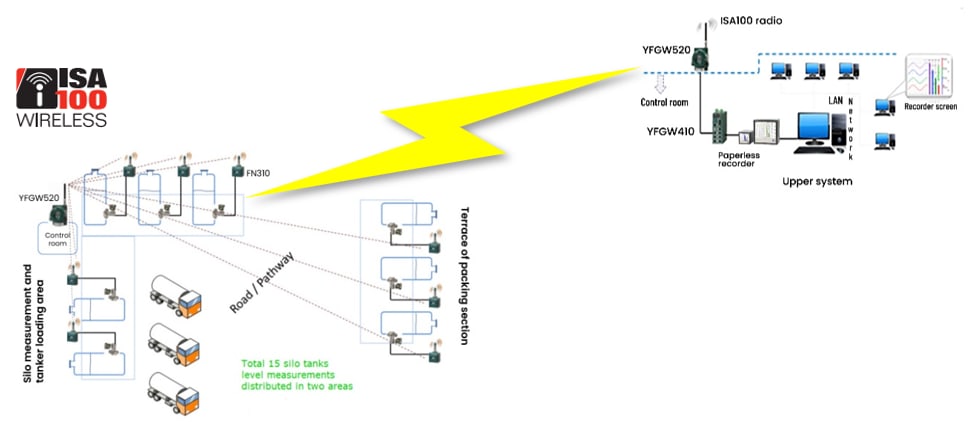
Figure 2. Continuous monitoring of silos using the FN310 Field Wireless Multiprotocol Module,
FN120 Field Wireless Communication Module, HART transmitter, ISA 100 wireless,
YFGW520 Field Wireless Access Point, YFGW410 Field Wireless Management Station,
and the GX10/GX20 Paperless Recorder.
Conclusion
- Monitoring all silo levels from one location makes it possible to use an equal amount of raw milk for each silo and reduce the risk of degradation of the raw milk.
- The HART transmitter connected to the FN 310 is driven by the built-in battery, eliminating the need for power supply equipment and wiring.
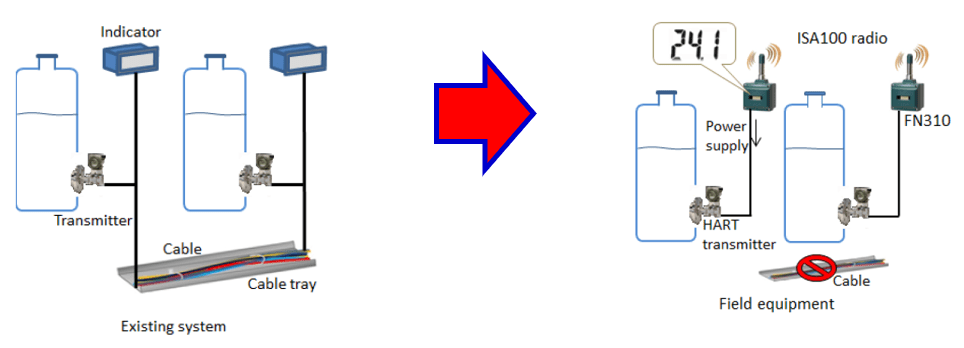
Figure 3. The HART transmitter connected to the FN310 is powered through a built-in battery.
This eliminates the need for wiring and power supply equipment.
Industries
-
Food & Beverage
The food and beverage industry must produce safe, high-quality foods and beverages for consumers. In addition to quality control, the manufacturing processes include many challenges such as managing ingredients, improving efficiency and handling global environmental issues. Yokogawa leverages its decades of technological expertise to help customers build and operate the ideal factory.
Related Products & Solutions
-
FN310 Field Wireless Multi-Protocol Module
- Field Wireless Multi-Protocol Module with Field Wireless Communication Module FN110
- Connect field wireless device with field wireless network
- Sensor data to field wireless network
-
Field Wireless
Reduce infrastructure investment and increase plant operation insights.
-
Paperless Recorders
- Portable paperless recorders
- Fully integrated data acquisition and display stations
- Secure, built-in data storage and network connectivity
Have Questions?
Contact a Yokogawa Expert to learn how we can help you solve your challenges.