Prevent costly downtime and process equipment failures with real-time pressure monitoring. Yokogawa’s Sushi Sensor is the optimal choice for industries depending on bottled gas in essential procedures.
Downtime due to a lack of bottled gas can be catastrophic. Shutting down an analyzer due to depleted gas can result in regulatory fines, damage to equipment, and costly delays. Traditionally, pressure monitoring of bottled gas has been performed manually, leaving room for error and increasing the risk of running out before the planned cylinder exchange. Continuous pressure monitoring and reporting, real-time calculation of consumption rates, anticipated replacement dates, and alerting users of potential leaks are possible with our product. Users can accurately predict when their gas supply will require refills/replacement to avoid costly shutdowns and fines.
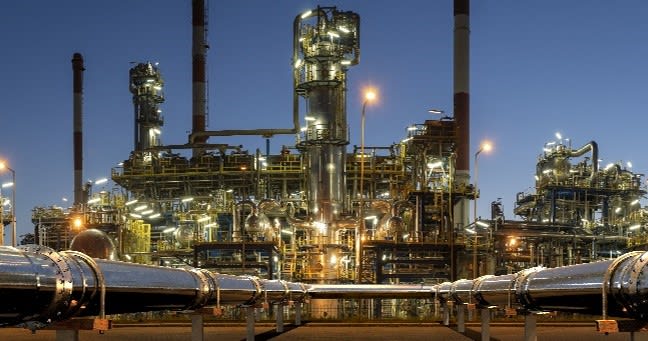
Example: Petrochemical plant using bottle gas pressure
Challenges
Challenges arise in industries such as petrochemical, chemical, and pharmaceutical plants where the use of bottled gas is integral to processes like calibration, carrier gas, and utility gas. These processes are critical to production and operations, necessitating a reliable and uninterrupted gas supply. However, the traditional method presents significant drawbacks. The approach relies on intermittent checks, making it difficult to predict and document usage trends accurately. Moreover, manual monitoring is prone to human error. These limitations highlight the pressing need for an advanced and dependable solution to effectively monitor bottled gas pressure.
Running out of bottled gas carries severe consequences for analyzer operation, leading to production downtime, financial penalties, and potential equipment damage. The process of replenishing bottled gases can take 4 to 6 weeks if suitable replacement bottles are not readily available on-site, resulting in prolonged plant shutdowns. Beyond operational disruptions, inadequate gas supply can cause analyzer damage and regulatory fines. To mitigate these risks, monitoring the pressure of the bottles becomes crucial. However, the current practice increases the likelihood of running out of gas before the next scheduled check.
Solution
Introducing the Sushi Pressure Sensor, a wireless monitoring solution that revolutionizes bottled gas pressure monitoring. These compact, battery-powered sensors utilize the LoRaWAN wireless network for seamless data transmission. With three versions available - Vibration, Temperature, and Pressure - they are versatile and suitable for various monitoring applications. The Sushi Sensors offer long-term operation without frequent maintenance, continuously measuring and transmitting data for up to 10 years.
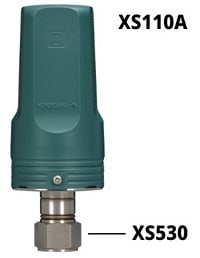
Wireless Pressure Sensor
With the Sushi Pressure Sensor, you gain access to advanced monitoring capabilities. Continuous monitoring ensures real-time awareness of pressure levels, and real-time alarming promptly notifies users of abnormal events or leaks. The sensor also enables predictive monitoring allowing for proactive planning and avoiding downtime.
After-hours notifications via email or text messages ensure critical alerts reach the right personnel promptly. The sensor's low maintenance requirements and long battery life optimize operational efficiency and free up human capital. Complementing the sensor is the GA10 Software which seamlessly integrates with the sensor for efficient data management and analysis, empowering informed decision-making.

In conclusion, the Sushi Pressure Sensor offers a superior wireless monitoring solution for bottled gas pressure. With continuous monitoring, real-time alarming, predictive capabilities, after-hours notifications, and low maintenance requirements, it ensures a reliable and efficient monitoring system.
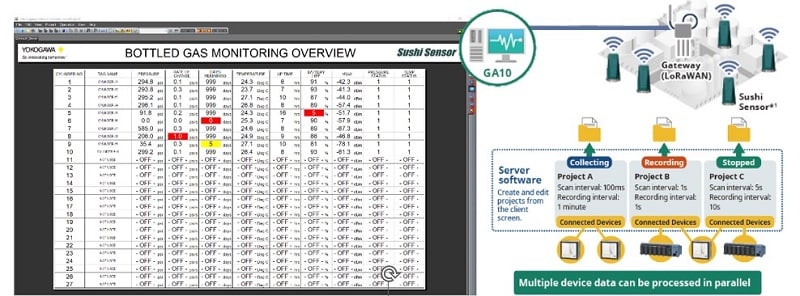
Data Logging Software GA10 - Monitors and records data from a variety of instruments via networks
Key Benefits
- Continuous monitoring in real-time.
- Predictive monitoring for proactive planning.
- Prompt alerts for abnormal events and leaks.
- After-hours notifications for quick response.
- Low maintenance, long-term operation.
- LoRaWan wireless networks transmit in the 915MHz range, allowing them to have a long-range line of site performance.
- Typical range for the Sushi sensors is up to 0.5 miles.
- Improved operational efficiency.
- Easy deployment and integration.
- Integration with GA10 Software for comprehensive data management.
Overall, the Sushi Sensor offers continuous, predictive monitoring with real-time alerts, low maintenance, and versatile deployment options. It ensures reliable data transmission, improves efficiency, and integrates seamlessly with the GA10 Software for comprehensive data management and analysis. For industries depending on bottled gas in essential procedures, it is the optimal choice.
Industries
-
Chemical
Chemical plants rely on continuous and batch production processes, each posing different requirements for a control system. A continuous process calls for a robust and stable control system that will not fail and cause the shutdown of a production line, whereas the emphasis with a batch process is on having a control system that allows great flexibility in making adjustments to formulas, procedures, and the like. Both kinds of systems need to be managed in available quality history of product, and to be able to execute non-routine operations. With its extensive product portfolio, experienced systems engineers, and global sales and service network, Yokogawa has a solution for every plant process.
-
Petrochemical
- Diverse needs of petrochemical companies’
- Improve quality, productivity
- Yokogawa tailor-made solutions, long and wide-ranging experience in this field
-
Pharmaceutical
Under continual pressure to increase profitability, maintain government compliance, and meet emerging market opportunities, the pharmaceutical manufacturing industry faces unique challenges that require unique solutions. As one of the world’s leading industrial automation suppliers, Yokogawa is poised and prepared to deliver those solutions, creating individualized lean manufacturing techniques that deliver consistent, measurable results.
Related Products & Solutions
-
Data Logging Software GA10
The latest software that enables you to build a DAQ system without programming. Designed for maximum compatibility with Yokogawa recorders, data loggers, temperature controllers, and power monitors, GA10 can also acquire data via Modbus communications.
-
XS110A Wireless Pressure Sensor - Wireless Pressure Monitoring
Wireless Pressure Monitoring Module
-
Analyzers
Process analyzers are used to determine the chemical composition and physical properties of substances used in industrial processes.
-
Sushi Sensor
Optimize processes with a range of wireless measurement and diagnostic solutions.
-
Sushi Sensor
Optimize processes with a range of wireless measurement and diagnostic solutions.
Have Questions?
Contact a Yokogawa Expert to learn how we can help you solve your challenges.