Executive Summary
Indian Oil Company Limited, Uttar Pradesh, India
The Mathura refinery is a strategically important facility that supplies diesel, gasoline, aviation turbine fuel, kerosene, liquefied petroleum gas, furnace oil, and bitumen to customers throughout northwestern India. The sixth refinery to be built by the Indian Oil Company Limited (IOCL), it had an initially capacity of 6.0 MMTPA at the time of its commissioning in 1982. Originally configured with facilities that included crude oil distillation (CDU), vacuum distillation (VDU), vis-breaker (VBU), and Merox process units, this refinery was revamped beginning in 1999 with the installation of a diesel hydro desulphurization unit (DHDS) licensed from the French firm Axens, for the production of high speed diesel (HSD) fuel with a low sulphur content of 0.25% (maximum).
A once-through hydrocracker (OHCU) and a hydrogen generation unit (HGU) were added on in 2000, increasing the plant's capacity to 8.0 MMTPA. As part of this plant revamp, a new distributed control system (DCS) and safety instrumented system (SIS) were installed to control both the originally configured and newly introduced units at this refinery.
In 2013, Yokogawa India was commissioned to carry out a revamping of the control and safety systems at the Mathura refinery. This project involved the design, engineering, installation, and commissioning of a CENTUM VP distributed control system (DCS) and a ProSafe-RS safety instrumented system (SIS) to replace the refinery's legacy systems. The project scope included the removal of the legacy DCS and the design, engineering, installation, and commissioning of an integrated CENTUM VP DCS and ProSafe-RS SIS solution. All this work was done on a tight schedule, while the refinery was shut down for routine maintenance.
Before and after revamp photos of the central control room (CCR).
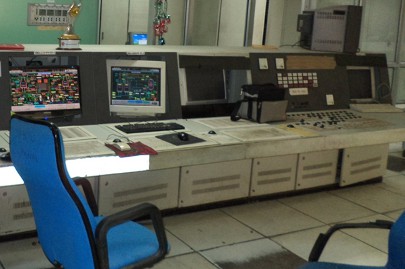
Before
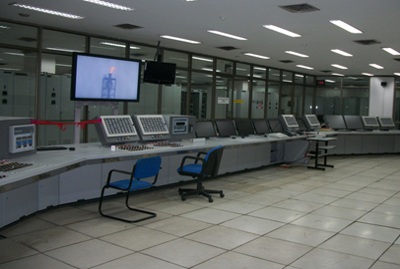
After
The CCR layout was jointly designed by IOCL and Yokogawa India. The number of consoles was increased to improve efficiency.
The Challenges and the Solutions
A tight schedule for a demanding project
- The removal of the existing systems, including 180 cabinets and 28,300 terminations, modifications to accommodate the new CENTUM VP system, in-stallation of new marshalling and system cabinets (201 cabinets), termination of signals (approximately 30,000), powering, loop checking, loop commis-sioning and system commissioning needed to be completed within a refinery shutdown period of just 20 days.
- For 400 signals, loop checking extended beyond the field junction boxes as the corresponding trans-mitters were to be replaced by Yokogawa HART transmitters.
- The "as built" I/O database was not available due to modifications that had been carried out over the past 10-15 years.
- No loop/logic write-up was available for the existing system.
- The DHDS AspenTech APC and connectivity to the plant LAN through a Honeywell PHD process information management system needed to be restored on the new system.
- The, suppliers had to be very tightly monitored as they had just eight weeks to deliver 200 cabinets (Rittal), 8,000 safety barriers (P&F), and work-stations and servers (Dell).
Good teamwork
With the aim of having minimal re-engineering of control loops and ensuring the commissioning of the units on the first attempt, Yokogawa and IOCL's engineers worked closely together to expedite the following tasks:
- A task force was formed to directly retrieve data from field devices and the existing systems.
- Based upon the physically verified termination schedule, a new I/O database was created and compared with the existing system's database. To ensure the complete correctness of the new database, which had been designed based on existing documents, internal loop checking was conducted on the existing DCS after the plant was shut down. Any necessary modifications were then made to ensure the 100% mapping of field data needed for a smooth start up of the plant. This remained the key for making the system ready exactly as built at site, enabling a smooth re-commissioning of the plant.
- The IOCL engineering team physically validated all engineering inputs, which also served to double check the engineering database.
- Based on photos of the existing graphics, new graphics were created. Each and every type of graphic modifier (color change/blinking ) in the existing DCS was checked and recorded and then configured in the Yokogawa DCS so as to retain operational integrity after the revamp.
- With IOCL's support, all 3rd party interfaces were engineered, validated, and commissioned on site.
- Staging and FAT for all six units was done in parallel at Yokogawa India, in close cooperation with IOCL.
- IOCL assisted by making building modifications to accommodate the removal of old cabinets and the installation of new cabinets.
- Given the tight schedule for the on-site work, a detailed hourly work plan was prepared for the period commencing with the receipt of the systems at the site. Necessary items were stored based on the order in which they would be used during the refinery shutdown period and consequent evacu-ation of space to make room for replaced system at stores to field loop checking up to field instrument.
- Commissioning of the hydrogen unit and parallel commissioning of all remaining units along with communications between the units were priority items during the shutdown.
All installation work was completed, units were powered on, loops were checked, commissioning was completed, and stable operation was achieved in a span of just 19 days - one day ahead of schedule.
Customer Satisfaction
The following key parameters were provided by IOCL as benchmarks for this project and each was met by Yokogawa India:
- Provide a best-in-class DCS/SIS solution on a robust, fast DCS network
- Integrate the DCS/ESD system network
- Ensure a robust HMI to be used as a direct node on the DCS network
- Provide a redundant ProSafe-RS SIS architecture for both ESD, from I/O level to CPU
- Include sequence of events (SOE) functionality with 1 msec event resolution for trip analysis and troubleshooting in the SIS - implemented as a built-in feature of ProSafe-RS
- Ensure stable control functions - implemented rigorously through offline checks during pre-commissioning
- Strictly adhere to supply and shutdown schedule
New system | |
System tags | 23,800 |
Field control stations (DCS controllers) | 28 |
Safety control stations (ProSafe-RS) | 11 |
Human machine interface stations | 23 |
DCS engineering stations | 4 |
SIS engineering stations | 4 |
Other stations (*) | 14 |
(*): Historical data stations, OPC interface stations for 3rd party systems, alarm information and management stations, documentation node (DON) stations, sequence of events (SOE) stations
Related Industries
-
오일 및 가스관련 다운스트림
석유 및 가스 산업은 최근 몇 년간 어려움이 커지고 있습니다. 여기에는 처리할 원료의 변화하는 특성, 공정 설비 및 장비의 고령화, 에너지 비용의 상승, 정유 공장을 안전하고 효율적으로 운영할 수 있는 숙련 된 플랜트 운영자의 부족, 그리고 시장과 시장의 끊임없이 변화하는 요구 사항이 포함됩니다.
지난 수년간 Yokogawa와는 많은 어려움을 겪고 있는 산업 솔루션을 제공하기 위해 여러 다운스트림 회사와 파트너 관계를 맺어 왔습니다. Yokogawa의 VigilantPlant 솔루션은 플랜트 소유자가 플랜트 내에서 최대한의 수익성과 지속 가능한 안전을 달성하도록 도왔습니다.
-
정유
끊임없이 변화하는 시장에서 정유설비는 원유 처리 장치뿐만 아니라 이익센터로도 인식됩니다. 동시에 그러한 시설에서 안전의 필요성에 대한 각별한 인식이 있습니다. 계획, 스케줄링, 관리 및 제어를 포함하는 총 생산 솔루션은 수익성, 효율성 및 환경 보호를 위한 장기 목표를 달성하는 데 필요합니다. Yokogawa는 자동화 분야에서 수년간 축적 된 전문성을 바탕으로 보다 향상된 작업성 및 보다 깨끗한 세상을위한 효율적인 솔루션을 제공합니다.
Related Products & Solutions
-
Distributed Control System (DCS)
10,000개가 넘는 플랜트의 운영자는 매년 생산 목표를 달성하기 위해 Yokogawa의 DCS 기술과 솔루션을 신뢰합니다.
-
SIS (Up to SIL 3) ProSafe-RS
ProSafe-RS는 IEC 61508에 명시된 SIL(Safety Integrity Level) 3을 충족하는 것으로 독일 인증 기관(TÜV)의 인증을 받은 안전 계측 시스템입니다.
-
컷오버 계획 및 실행
신중한 계획과 실행을 통해 요꼬가와는 고객의 시스템을 안전과 합리적인 비용, 가치를 더한 마이그레이션 프로세스를 실현 할 수 있도록 도와줍니다.