Introduction: What is Energy Optimization
- Whatever utilities the process needs, the process gets.
- But the fulfillment of the process utilities needs should be done at the lower cost,
- within emissions constraints (solving energy and carbon balance together is key for consistency),
- within current operating constraints, and
- within contractual constraints
- A Utilities Real Time Optimizer such as Visual MESA ensures that Operations is doing the best it can with the utilities assets available at that moment and within the current operating conditions.
- It provides Operations a Real Time Target for operating the utilities at the minimum Site-Wide overall Utilities cost.
How the RTEMS Works
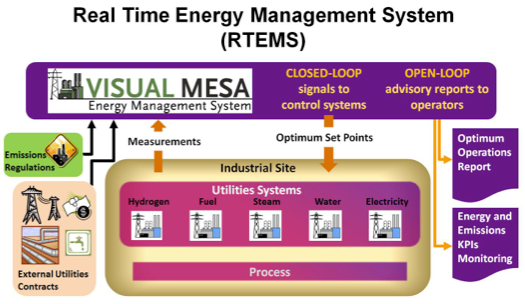
Calculation Foundation for the Energy Related Key Performance Indicators
- The RTEMS model is the foundation
- A site-wide integrated real time utilities
model ensures:
- Data health
- Data validation for all individual meters, including what happens to the model when a certain individual meter goes bad.
- Data Consistency
- By solving the integrated heat and material balances of the complete utilities systems
- Imbalances (both steam and fuel) are key indicators of consistency
- An online, real time Calculation Framework
- Data health
Real Time Online Energy Management System Implementation
- Saudi Kayan Petrochemical Company is one of the largest petrochemical complexes in the world, located in Jubail Industrial City, Kingdom of Saudi Arabia.
- A real time online utilities model was implemented to help with the energy cost minimization and energy management for the Petrochemical Complex.
- The real time, online, energy management system allows identifying the different economic trade-offs that challenges the production and internal distribution of the energy at minimum cost.
Real Time Online Energy Management System Implementation
- A detailed non-linear rigorous model of the steam, fuels, power, boiler feed water and condensates systems has been built, including all the interactions between these systems, constraints and degrees of freedom for their operation.
- The same model used for the online, real time optimization, is also used in stand-alone mode, populated either with current or historical data, to perform case studies for planning or evaluating alternatives for a better operation of the energy system.
- As a result of the project, the information of the Saudi Kayan Petrochemical Complex energy system has been organized into one real time model and a single environment to which everyone has access through a web browser.
Real Time Online Energy Management System Implementation: Visual MESA model views
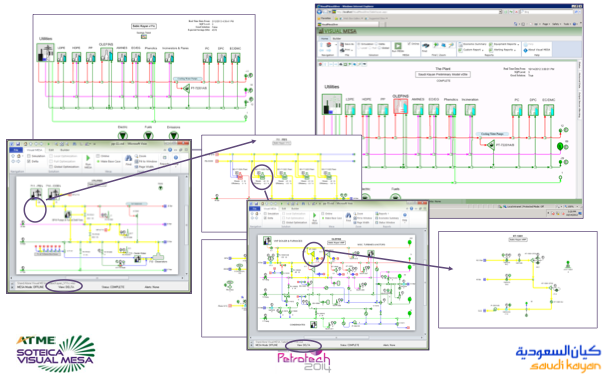
Real Time Online Energy Management System Implementation: Optimization Actionable Items
- Optimization Actionable Items:
- Packaged Boilers steam production (Fuel Gas Consumer)
- Crude Oil Boilers steam production (Crude Oil Consumer)
- VHP Boiler steam production (Fuel Gas Consumer)
- Turbine/Motor Swaps (Cooling water pumps, BFW pumps,... )
- Extraction/condensing turbines (Olefins Unit main compressors)
- Steam let-downs, vents and condensing will change automatically, manipulated by the control system, as a consequence of the actions performed over the optimization handles.
Real Time Online Energy Management System Implementation: Economic Benefits Example
- The total Real Time Online Energy Management System benefits have been around 3.42 MM$/year.
- Additional savings were obtained from:
- Online Energy Monitoring, Auditing and Accounting
- Online Energy KPIs
- What-if studies:
- Capital Project Opportunities
- Planning / Scheduling of Utilities
- An example will be presented in which Visual MESA recommendations were partially applied and, as consequence, 1.05 MM $/year of savings where achieved.
Real Time Online Energy Management System Implementation: Savings
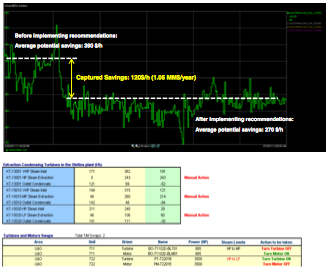
- The next figure illustrates the savings that were obtained from real time optimization between February 28th and March 7th, 2013
- Around 3:00 AM on March 2nd, Operators applied one of the optimization actions calculated by the RTEMS and 1.05 MM$/year of savings were immediately captured (i.e., the predicted savings trend drops)
- At that time, before SK operators took any action, Visual MESA was suggesting two turbine and motors swaps and increasing the extraction in all three extraction-condensing turbines at Olefins plant
Real Time Online Energy Management System Implementation: Applying recommendations
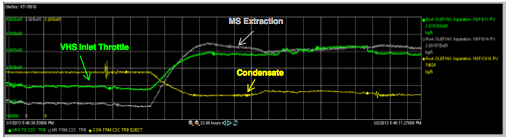
- Around 3:00 AM on March 2nd, operators started increasing the MP steam extraction on KT-15010 turbine located at the Olefins plant. This was only one of the calculated optimization actions.
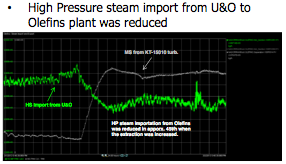
Real Time Online Energy Management System Implementation: Consequences of applied actions
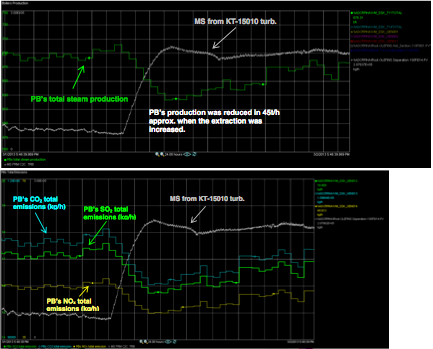
Relevance of Visual MESA RTEMS for SK's Sustainability Initiative
- RTEMS continuously calculates Key Performance Indicators (KPIs) such as boiler and heater efficiencies, plant energy consumptions, steam imbalances, etc. on a validated and consistent basis.
- RTEMS acts as the "Steam Vent and Letdown Police". Everybody will know that Visual MESA is looking at the Site- wide situation 24x7x365. It is continuously helping reduce cost.
- And taking into account the site-wide emission constraints.
Conclusions
- Visual MESA based Real Time Energy Management System was successfully implemented at Saudi Kayan Petrochemical Complex, helping to achieve energy cost savings.
- The same model used for the online, real time optimization, can also used in stand-alone mode, populated either with current or historical data, to perform case studies for planning or to evaluate alternatives for a better operation of the energy system.
- As a result of the project, the information of the Saudi Kayan Petrochemical Complex energy system has been organized into one real time model and a single environment to which everyone has access through a web browser.
Related Industries
-
화학
화학 플랜트는 연속 및 Batch 생산 공정에 의존하며, 각각은 제어 시스템에 대한 다양한 요구 사항을 제시합니다. 연속 공정은 실패하지 않고 생산 라인을 중단시키는 견고하고 안정적인 제어 시스템을 필요로하는 반면, Batch 공정의 중요성은 수식, 절차 및 공정을 조정하는 데 있어 큰 유연성을 허용하는 제어 시스템을 갖추는 데 있습니다. 두 종류의 시스템 모두 제품의 사용 가능한 품질 내역에서 관리되어야 하며 비일상적인 작업을 수행할 수 있어야 합니다. Yokogawa는 광범위한 제품 포트폴리오, 숙련된 시스템 엔지니어 및 글로벌 영업 및 서비스 네트워크를 통해 모든 공장 공정에 대한 솔루션을 제공합니다.
-
석유화학
석유화학 업종 고객사의 요구는 매우 다양합니다. 경쟁이 치열한 오늘날의 시장에서 앞서 나간다면, 생산자는 품질과 생산성을 향상시키기 위해 노력하고 있습니다. Yokogawa는 이 분야에서의 오랜 기간의 광범위한 경험을 바탕으로 이러한 요구에 맞는 맞춤 솔루션을 제공합니다.