Executive Summary
Idemitsu Kosan, Japan
Idemitsu Kosan Co., Ltd. (Idemitsu) is a leading producer and distributor of oil, lubricants, and petrochemical products, and is also engaged in the research and development of functional and electronic materials as well as agricultural biochemicals. At the company's Technology & Engineering Center, technical experts are carrying out research in the refining and petrochemical fields, focusing on topics related to development, design, construction, operation, quality control, maintenance, and systems.
They provide technical supports that ensure safe and stable operations and enhance the competitiveness of processes. They also assist in the development of processes for manufacturing new functional chemicals and in licensing for the export of process and catalyst technologies.
At this center's bench plant, Idemitsu is using Yokogawa's Exapilot operation efficiency improvement package in experiments involving catalysts that are used in refinery hydrogenation and hydrocracking units which play important roles in determining the qualities of the refined products. To optimize such a catalytic reaction, candidate catalysts are evaluated in the bench plant under various temperatures and pressure levels.
Idemitsu has been using the Yokogawa CENTUM distributed control system at this bench plant. On the other hand, they are also already familiar with the benefits of Exapilot used elsewhere in their organization. To improve operations and achieve the same benefits at this very complex bench plant facility, they decided to introduce Exapilot here as well.
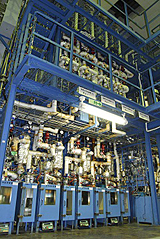
One of the bench plant units
The Challenges and the Solutions
Idemitsu's bench plant carries out more than 100 experiments each year. The operational settings differ for each test, determining how the plant's individual reactor units must be started up and shut down. The equipment used throughout the plant also varies depending on when it was installed. To prevent operator errors, it was essential to standardize operating procedures. To accomplish this, Exapilot was first introduced for use with the bench plant's main systems, then its use was broadened to other of this plant's functions. Specific advantages of the Exapilot system are as follows:
1. Dissemination of operator know-how
The bench plant startup and shutdown procedures for these experiments are complex, and they must be carried out repeatedly, placing great demands on the operators. The Exapilot system draws on the expertise of experienced personnel to provide cues that navigate operators step by step through each procedure.
2. Standardization of operations
Thanks to the use of Exapilot to set temperature gradients and alarm thresholds, the operation of the units throughout this plant is smoother and more uniform, resulting in improved safety.
3. Maintenance efficiency
Flowcharts created with Exapilot facilitate a greater understanding of the operation procedures. Idemitsu anticipates that this will allow its more junior personnel to operate this plant more effectively.
4. Labor-saving
Each experiment requires different parameter settings. Before the introduction of Exapilot, operators needed to manually enter data based on the information specified in a hard copy experiment plan submitted by the department that was requesting the experiment. Now operators receive an Excel document that can be used to automatically enter the data to the DCS in a single operation, and the operators only need to confirm the parameter settings. Excel reports can also be sent back to the requesting department, speeding up the overall process and ensuring greater accuracy.
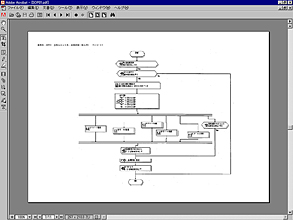
A standard operating procedure flowchart created by Exapilot
Future Plan
Based on the results achieved so far, Idemitsu expects that it will be able to achieve a 2,000 hour reduction in work hours by introducing Exapilot throughout this experimental facility. And to make more effective use of assets such as process gas chromatographs that are shared by more than one unit, the plan is to import the test schedule to Exapilot and automatically reflect this in the operating plan.
Customer Satisfaction
Our feedback from Idemitsu indicates that they have found Exapilot to be an effective tool in improving work efficiency. They appreciate the ability to create a flowchart that guides them in streamlining and optimizing an operation. They would like to see Exapilot enter wide use so that their operators can accumulate know-how and solve operational issues on their own. While still evaluating the use of Exapilot at their experimental facility, they do recognize that it has had the desired effect, and would like to extend the scope of its application and obtain further benefits.
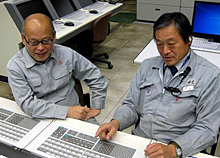
Kunio Furuuchi and Kazushige Chiba of the
Idemitsu Technology & Engineering Center
Related Industries
-
오일 및 가스관련 다운스트림
석유 및 가스 산업은 최근 몇 년간 어려움이 커지고 있습니다. 여기에는 처리할 원료의 변화하는 특성, 공정 설비 및 장비의 고령화, 에너지 비용의 상승, 정유 공장을 안전하고 효율적으로 운영할 수 있는 숙련 된 플랜트 운영자의 부족, 그리고 시장과 시장의 끊임없이 변화하는 요구 사항이 포함됩니다.
지난 수년간 Yokogawa와는 많은 어려움을 겪고 있는 산업 솔루션을 제공하기 위해 여러 다운스트림 회사와 파트너 관계를 맺어 왔습니다. Yokogawa의 VigilantPlant 솔루션은 플랜트 소유자가 플랜트 내에서 최대한의 수익성과 지속 가능한 안전을 달성하도록 도왔습니다.
-
정유
끊임없이 변화하는 시장에서 정유설비는 원유 처리 장치뿐만 아니라 이익센터로도 인식됩니다. 동시에 그러한 시설에서 안전의 필요성에 대한 각별한 인식이 있습니다. 계획, 스케줄링, 관리 및 제어를 포함하는 총 생산 솔루션은 수익성, 효율성 및 환경 보호를 위한 장기 목표를 달성하는 데 필요합니다. Yokogawa는 자동화 분야에서 수년간 축적 된 전문성을 바탕으로 보다 향상된 작업성 및 보다 깨끗한 세상을위한 효율적인 솔루션을 제공합니다.
Related Products & Solutions
-
Distributed Control System (DCS)
10,000개가 넘는 플랜트의 운영자는 매년 생산 목표를 달성하기 위해 Yokogawa의 DCS 기술과 솔루션을 신뢰합니다.
-
Procedural Automation (Exapilot)
Modular Procedural Automation (MPA)는 공정 플랜트에서 프로시저 지식을 수집, 최적화 및 보존하기 위한 유연한 방법론을 제공하며 신뢰성, 유연성 및 수명주기 비용 요구 사항을 충족합니다.