Executive Summary
Idemitsu Kosan, Japan
Idemitsu Kosan Co., Ltd. (Idemitsu) is a leading producer and distributor of oil, lubricants, and petrochemical products, and is also engaged in the research and development of functional and electronic materials as well as agricultural biochemicals. At the company's Technology & Engineering Center, technical experts are carrying out research in the refining and petrochemical fields, focusing on topics related to development, design, construction, operation, quality control, maintenance, and systems.
They provide technical supports that ensure safe and stable operations and enhance the competitiveness of processes. They also assist in the development of processes for manufacturing new functional chemicals and in licensing for the export of process and catalyst technologies.
At this center's bench plant, Idemitsu is using Yokogawa's Exapilot operation efficiency improvement package in experiments involving catalysts that are used in refinery hydrogenation and hydrocracking units which play important roles in determining the qualities of the refined products. To optimize such a catalytic reaction, candidate catalysts are evaluated in the bench plant under various temperatures and pressure levels.
Idemitsu has been using the Yokogawa CENTUM distributed control system at this bench plant. On the other hand, they are also already familiar with the benefits of Exapilot used elsewhere in their organization. To improve operations and achieve the same benefits at this very complex bench plant facility, they decided to introduce Exapilot here as well.
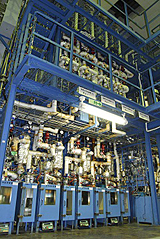
One of the bench plant units
The Challenges and the Solutions
Idemitsu's bench plant carries out more than 100 experiments each year. The operational settings differ for each test, determining how the plant's individual reactor units must be started up and shut down. The equipment used throughout the plant also varies depending on when it was installed. To prevent operator errors, it was essential to standardize operating procedures. To accomplish this, Exapilot was first introduced for use with the bench plant's main systems, then its use was broadened to other of this plant's functions. Specific advantages of the Exapilot system are as follows:
1. Dissemination of operator know-how
The bench plant startup and shutdown procedures for these experiments are complex, and they must be carried out repeatedly, placing great demands on the operators. The Exapilot system draws on the expertise of experienced personnel to provide cues that navigate operators step by step through each procedure.
2. Standardization of operations
Thanks to the use of Exapilot to set temperature gradients and alarm thresholds, the operation of the units throughout this plant is smoother and more uniform, resulting in improved safety.
3. Maintenance efficiency
Flowcharts created with Exapilot facilitate a greater understanding of the operation procedures. Idemitsu anticipates that this will allow its more junior personnel to operate this plant more effectively.
4. Labor-saving
Each experiment requires different parameter settings. Before the introduction of Exapilot, operators needed to manually enter data based on the information specified in a hard copy experiment plan submitted by the department that was requesting the experiment. Now operators receive an Excel document that can be used to automatically enter the data to the DCS in a single operation, and the operators only need to confirm the parameter settings. Excel reports can also be sent back to the requesting department, speeding up the overall process and ensuring greater accuracy.
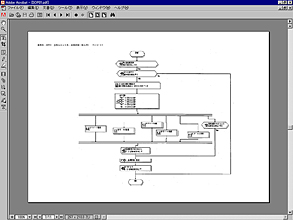
A standard operating procedure flowchart created by Exapilot
Future Plan
Based on the results achieved so far, Idemitsu expects that it will be able to achieve a 2,000 hour reduction in work hours by introducing Exapilot throughout this experimental facility. And to make more effective use of assets such as process gas chromatographs that are shared by more than one unit, the plan is to import the test schedule to Exapilot and automatically reflect this in the operating plan.
Customer Satisfaction
Our feedback from Idemitsu indicates that they have found Exapilot to be an effective tool in improving work efficiency. They appreciate the ability to create a flowchart that guides them in streamlining and optimizing an operation. They would like to see Exapilot enter wide use so that their operators can accumulate know-how and solve operational issues on their own. While still evaluating the use of Exapilot at their experimental facility, they do recognize that it has had the desired effect, and would like to extend the scope of its application and obtain further benefits.
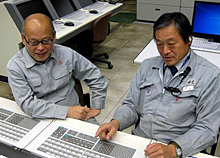
Kunio Furuuchi and Kazushige Chiba of the
Idemitsu Technology & Engineering Center
Related Industries
-
Oil & Gas Downstream
The oil & gas downstream industry has been facing an increasing number of challenges in recent years. These include the changing characteristics of the feedstock to be processed, aging of process facilities and equipment, rising cost of energy, lack of skilled plant operators who can run a refinery safely and efficiently, and the ever-changing requirements from both the market and the customer.
Over the years, Yokogawa has partnered with many downstream companies to provide industrial solutions focused on solving these challenges and problems. Yokogawa's VigilantPlant solutions have helped plant owners to achieve maximum profitability and sustainable safety within their plants.
-
Refining
In the ever changing marketplace, refineries are seen not only as crude processing units but also as profit centers. At the same time, there is a keen awareness of the need for safety at such facilities. A total production solution that encompasses planning, scheduling, management, and control is required to achieve long-term goals for profitability, efficiency, and environmental protection. With years of expertise in the automation field, Yokogawa can bring you affordable total solutions for improved operability and a cleaner world.
Related Products & Solutions
-
Distributed Control System (DCS)
Our distributed control system (DCS) enables automation and control of industrial processes and enhanced business performance. Over 10,000 plants entrust Yokogawa DCS to deliver their production goals.
-
Procedural Automation (Exapilot)
Procedural Automation (Exapilot) provides a flexible methodology to capture, optimize and retain procedural knowledge in a process plant while meeting requirements in reliability, flexibility, and lifecycle costs.