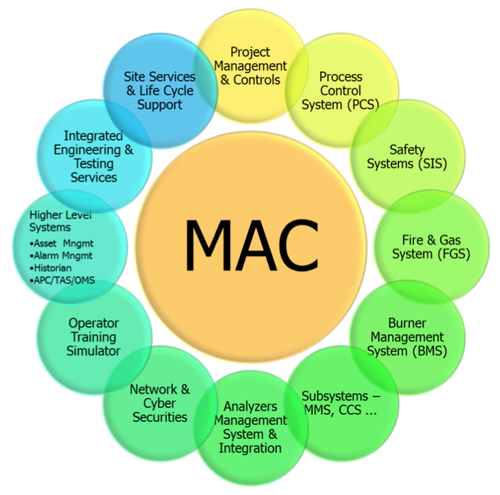
ความสามารถในการส่งมอบขอบเขตทั้งหมดของการดำเนินโครงการในโครงการระบบอัตโนมัติทางอุตสาหกรรมมีความสำคัญมากกว่าที่เคย
ความท้าทาย สำหรับลูกค้า
เมื่อความต้องการพลังงานทั่วโลกเพิ่มขึ้นพืชจึงมีภารกิจในการดำเนินโครงการที่มีคุณภาพสูงการดำเนินงานของโรงงานและการบำรุงรักษา
อย่างไรก็ตาม บริษัท ต่างๆถูก จำกัด มากขึ้นด้วยปัญหาด้านบุคลากรงบประมาณและตารางงานที่หดหาย นอกเหนือจากกิจกรรมการก่อสร้างระดับรากหญ้าในตลาดเกิดใหม่แล้ว บริษัท ต่างๆยังต้องเผชิญกับภารกิจในการดำเนินโครงการหลายโครงการพร้อมกันในพื้นที่ทางภูมิศาสตร์ที่แตกต่างกัน
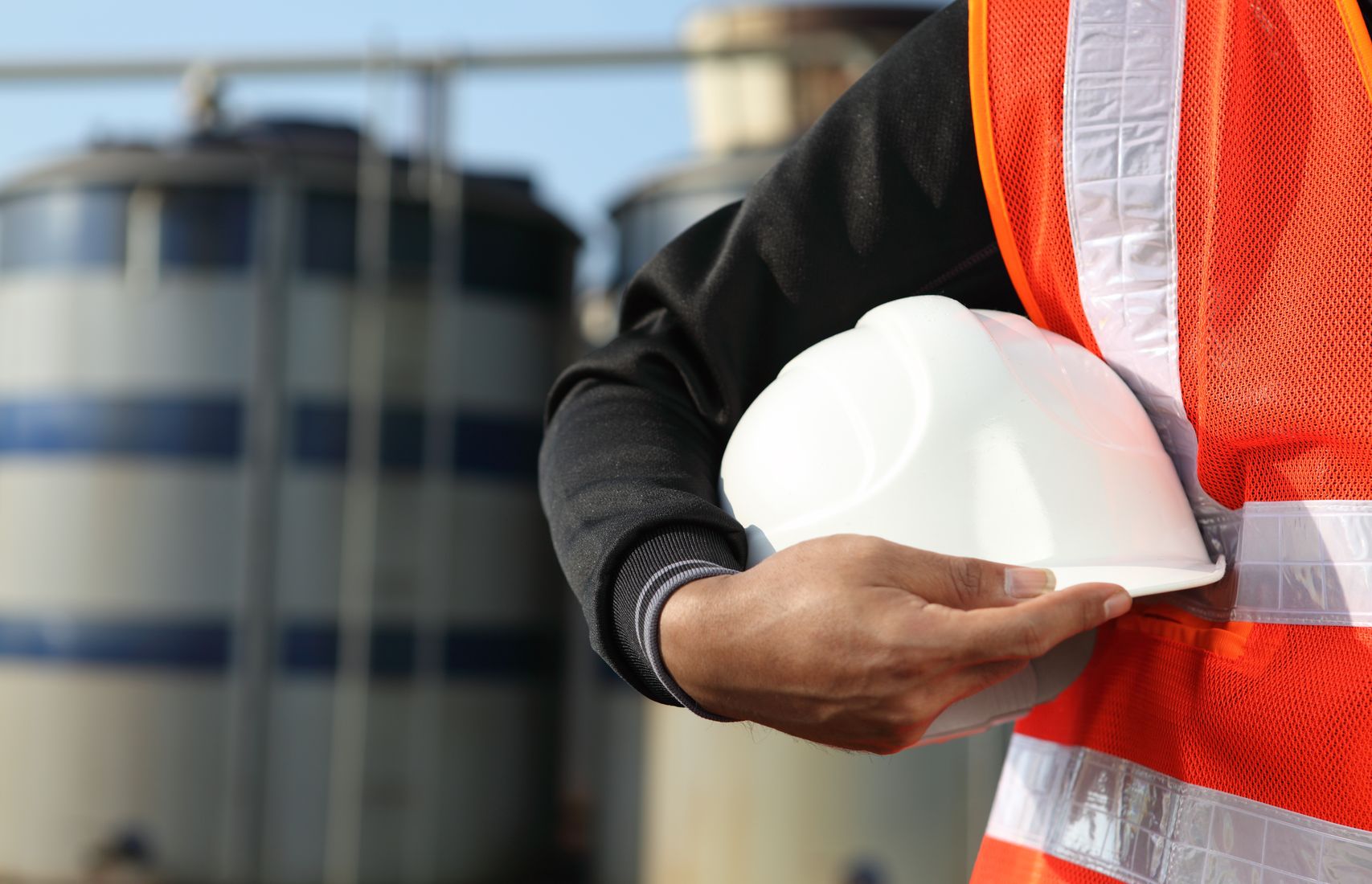
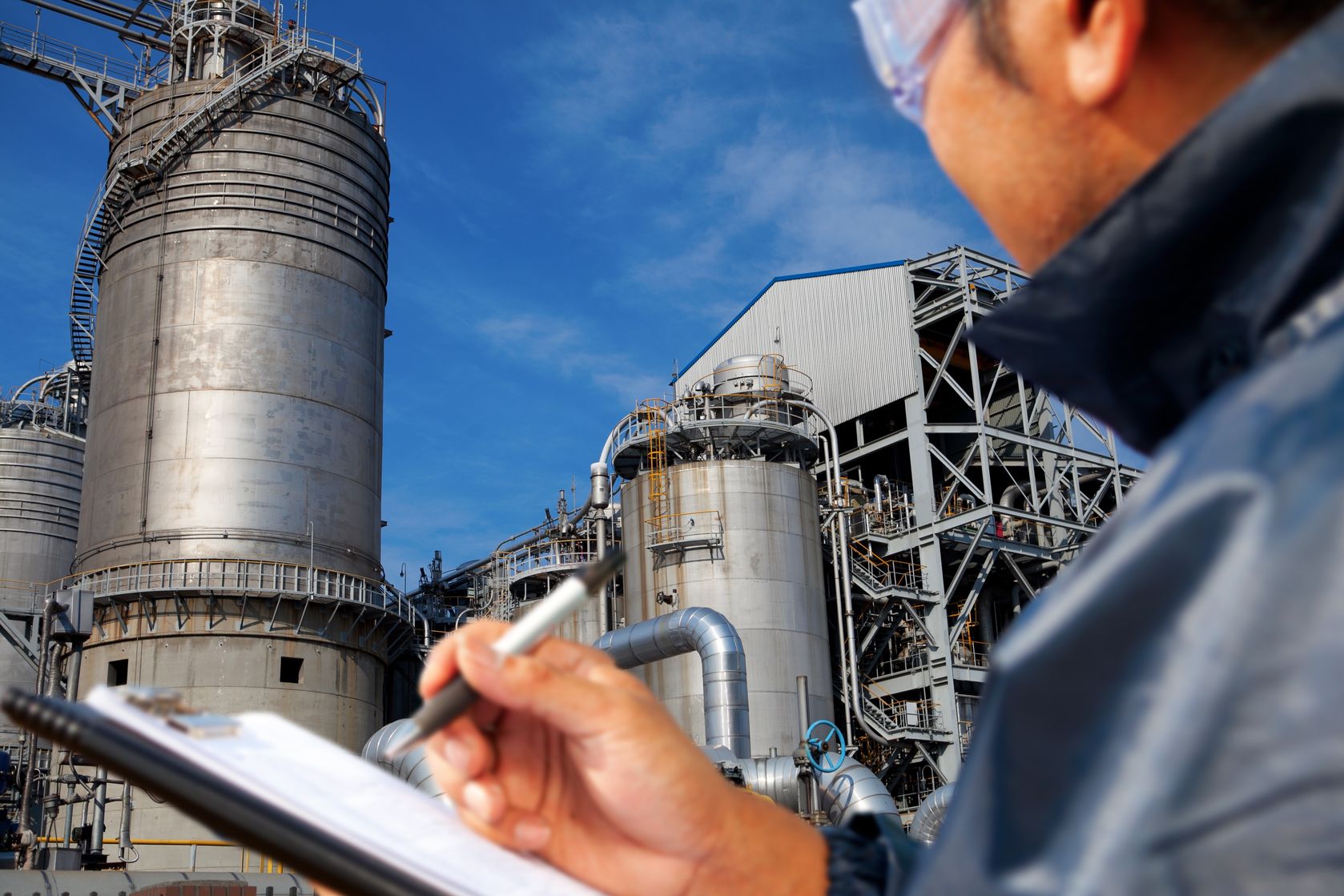
โซลูชั่นของเรา
บริษัท ต่างๆต่างพึ่งพา โยโกกาวา มากขึ้นในการรับหน้าที่เป็นผู้รับเหมาระบบอัตโนมัติหลักโดยเป็นเจ้าของความรับผิดชอบในด้านที่เกี่ยวข้องกับระบบอัตโนมัติทั้งหมดของโครงการด้วยวิธีการดำเนินโครงการของ Innovative MAC Services (yi-MAC)
โยโกกาวา จัดหาผู้เชี่ยวชาญด้านระบบควบคุมที่มีคุณสมบัติสูงและมีทรัพยากรอย่างดีเพื่อเป็นวิศวกรจัดหา / จัดหาและจัดการเครื่องมือวัดระบบควบคุมระบบเครื่องมือด้านความปลอดภัยและอินเทอร์เฟซที่เกี่ยวข้องสำหรับส่วนประกอบและสิ่งอำนวยความสะดวกทั้งหมดของโครงการ
สิทธิประโยชน์ ของลูกค้า
โยโกกาวา ในฐานะ MAC จะรับผิดชอบในทุกขั้นตอนที่เกี่ยวข้องกับระบบอัตโนมัติของโครงการ
โยโกกาวา สร้างองค์กรโครงการที่เหมาะสมที่สุดและทำงานโดยตรงกับผู้ใช้ปลายทาง EPC และบุคคลที่สาม ด้วยวิธีการของ MAC ในการติดต่อกับ โยโกกาวา โดยตรงลูกค้าจึงไม่จำเป็นต้องจัดการซัพพลายเออร์ระบบอัตโนมัติต่างๆ
ลูกค้าสามารถประหยัดต้นทุนลดความเสี่ยงและระยะเวลาในการจัดส่งที่สั้นลงได้เป็นต้นด้วยเครือข่ายและทรัพยากร วิศวกรรม โยโกกาวา สามารถดำเนินโครงการได้อย่างปลอดภัยและมีประสิทธิภาพจากนั้นให้การสนับสนุนการดำเนินงานที่เหมาะสมตลอดวงจรชีวิตของโรงงานทั้งหมด
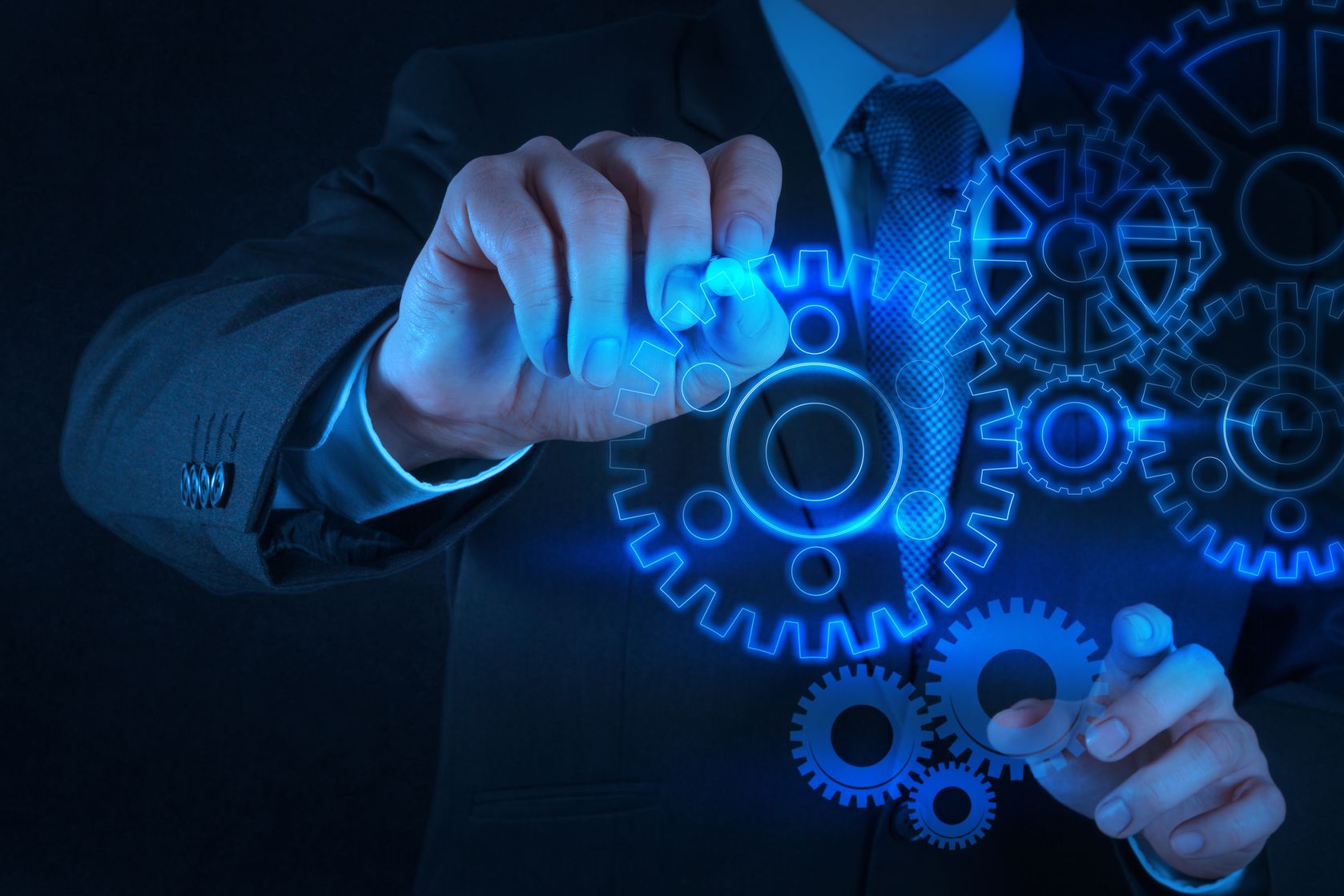
แนวทางดั้งเดิมเทียบกับวิธี MAC
เมื่อเทียบกับวิธีการแบบเดิม โยโกกาวา MAC ช่วยประหยัดค่าใช้จ่ายได้อย่างมากสำหรับโครงการโดยรวม
ผู้ใช้ปลายทางชั้นนำของโลกจำนวนมากโดยเฉพาะในอุตสาหกรรมกระบวนการกำลังใช้แนวทาง MAC กับโครงการทุนทั้งหมดของพวกเขา วิธี MAC สามารถทำให้โครงการประหยัดต้นทุนได้ถึง 30% เมื่อเทียบกับวิธีการแบบเดิม ต้นทุนจะลดลงในเกือบทุกขั้นตอนของโครงการเนื่องจากซัพพลายเออร์ระบบอัตโนมัติได้รับการสนับสนุนให้รวม ความเชี่ยวชาญ อุตสาหกรรมและแอพพลิเคชั่นเข้าด้วยกันเพื่อดำเนินโครงการในลักษณะที่สอดคล้องกัน ซึ่งหมายถึงการพัฒนาแนวทางปฏิบัติและขั้นตอนที่เป็นมาตรฐานและสามารถนำไปใช้กับโครงการต่างๆเพื่อลดต้นทุน
รายละเอียด
บริษัท ต่างๆสามารถรับรู้ถึงประโยชน์ที่สำคัญได้โดยการร่วมมือกับ โยโกกาวา ในฐานะผู้รับเหมาระบบอัตโนมัติหลัก:
- การจัดการโครงการทั้งหมด
- จุดเดียวของความรับผิดชอบและหน้าต่างเดียว
- ความมุ่งมั่นที่มีต่อลูกค้าในระดับองค์กร
- การออกแบบและ วิศวกรรม
- มาตรฐานระบบอัตโนมัติสำหรับหลายโครงการ
- การออกแบบมาตรฐานระบบอัตโนมัติ
- เวลาจัดส่งสั้นลง
- ลดการเปลี่ยนแปลงที่ไม่คาดคิดเนื่องจากการมีส่วนร่วมของ MAC ในช่วงต้น
- การมีส่วนร่วมของลูกค้าขั้นต่ำในระหว่างการดำเนินโครงการ
- สถานที่และทรัพยากร วิศวกรรม ระดับโลก
- เครือข่ายการจัดซื้อทั่วโลก
- ประหยัดค่าใช้จ่ายและลดความเสี่ยงโดยติดต่อกับ โยโกกาวา โดยตรง
บริการ
- การบริหารโครงการ
- การควบคุมต้นทุนและกำหนดการ
- ฟีดและวิศวกรรมรายละเอียด
- การสนับสนุนการ จัดซื้อจัดจ้าง
- อินเทอร์เฟซแพ็คเกจของผู้ขาย
- การรวมระบบและการเขียนโปรแกรม
- การสนับสนุนการก่อสร้าง
- การสนับสนุนการว่าจ้าง
- การฝึกอบรม
- การสนับสนุนการดำเนินงาน
สิ่งที่ส่งมอบ
- การควบคุมกระบวนการและระบบ SCADA
- กระบวนการและระบบปิดระบบฉุกเฉิน
- การตรวจจับไฟและก๊าซ
- ระบบข้อมูล
- ระบบการสื่อสาร
- เครื่องมือวัดที่เลือก
- เครื่องส่ง
- วาล์วควบคุม
- เครื่องมือวัดระดับ
- แพ็คเกจที่เลือก
- การวัดแสงลื่นไถล
- อาคารตราสาร
- เครื่องจำลองトレーニング
- นักประวัติศาสตร์ / MES
- อะไหล่ทุน
แหล่งข้อมูล
- 16,000 FOUNDATION อุปกรณ์ Fieldbus
- ผู้รับเหมาระบบอัตโนมัติหลัก (MAC)
- การบูรณาการ แนวคิด DCS ได้ทุกที่กับระบบ SAP ของไซต์
- สัญญาการบำรุงรักษาระยะยาว
- การพัฒนาที่ยั่งยืน
- ในฐานะผู้รับเหมาระบบอัตโนมัติหลัก (MAC) สำหรับโครงการก่อสร้างโรงงานนี้ โยโกกาวา Brazil ได้ออกแบบติดตั้งและว่าจ้างโซลูชันการควบคุมและเครื่องมือวัดแบบบูรณาการ
- โยโกกาวา Brazil เสร็จสิ้นการว่าจ้างระบบเหล่านี้ก่อนกำหนดและการผลิตโพลีเมอร์สีเขียวก็เริ่มขึ้นในอีกหนึ่งสัปดาห์ต่อมา
Nederlandse Aardolie Maatschappij (NAM) เป็นผู้ผลิตก๊าซธรรมชาติรายใหญ่ที่สุดของเนเธอร์แลนด์ นอกเหนือจากสาขาบนบกแล้ว NAM ยังมีแพลตฟอร์มที่มีคนขับและระบบโมโนโวลต์ไร้คนขับอีก 4 แห่งใน 19 แห่งนอกชายฝั่ง สิ่งเหล่านี้เชื่อมต่อกับเครือข่ายไปป์ไลน์ที่ขึ้นฝั่งที่ Den Helder
ในปี 2554 แพนดอร่าเมทานอลได้เข้าซื้อโรงงานผลิตปิโตรเคมีในโบมอนต์รัฐเท็กซัสซึ่งถูกมอดไปตั้งแต่ปี 2547 โรงงานทั้งสองแห่งนี้ซึ่งเป็นโรงงานแอมโมเนียอายุ 13 ปีและโรงงานเมทานอลอายุ 50 ปีได้รับการบำรุงรักษาเพียงเล็กน้อยในช่วงที่มีการปิดปรับปรุงและ ได้รับผลกระทบโดยตรงจากพายุเฮอริเคนสองลูก
- โยโกกาวา ได้รับรางวัล Hot Cutover ของ BP Sharjah plant DCS
- โยโกกาวา ได้รับเลือกจาก BP ให้เป็นผู้รับเหมาระบบอัตโนมัติหลัก (MAC) สำหรับโครงการเพื่อแทนที่ DCS เดิมที่มีอยู่ของโรงงานชาร์จาห์ด้วย โยโกกาวา CENTUM VP
โครงการ Mars B ได้เพิ่มโครงสร้างพื้นฐานกรีนฟิลด์ดังต่อไปนี้เพื่อเพิ่มการผลิตที่สนามดาวอังคารและการค้นพบการสำรวจในบริเวณใกล้เคียง: แพลตฟอร์ม Olympus tension leg (TLP) ซึ่งมีช่องเจาะ 24 ช่องและแท่นขุดเจาะในตัว ระบบใต้ทะเล Boreas / South Deimos; และระบบส่งออกน้ำมันและก๊าซซึ่งรวมถึงแพลตฟอร์มน้ำตื้น WD-143C แพลตฟอร์ม Olympus tension leg (TLP) เริ่มผลิตเมื่อวันที่ 4 กุมภาพันธ์ 2014 TLP เป็นครั้งที่สองที่สนามดาวอังคารและเป็นอันดับที่หกสำหรับเชลล์ในอ่าวเม็กซิโก
Continuous Control Solutions ("CCS") ให้บริการโซลูชั่นเครื่องจักรเทอร์โบขั้นสูงสู่ตลาดโลกตั้งแต่ปี 2543 โดยมุ่งเน้นอย่างแน่วแน่ในการพัฒนาอัลกอริธึมการควบคุมขั้นสูงที่นำมาใช้กับแพลตฟอร์มฮาร์ดแวร์ PLC หรือ DCS ที่ลูกค้าเลือก CCS Turbo Machinery Control Solutions ได้รับการนำไปใช้บนแพลตฟอร์มฮาร์ดแวร์ที่หลากหลายรวมถึง Allen Bradley ControlLogix, Honeywell C300, Siemens S7, ABB AC800M และ Emerson DeltaV
โซลูชั่นการควบคุมต่อเนื่อง ("CCS") เชี่ยวชาญในความท้าทายในการควบคุมเครื่องจักรเทอร์โบอุตสาหกรรมสำหรับอุตสาหกรรมประเภทต่างๆ เทคโนโลยีเครื่องจักรเทอร์โบของ CCS และอัลกอริธึมการควบคุมที่ได้รับการจดสิทธิบัตรเป็นแพลตฟอร์มฮาร์ดแวร์ที่เป็นอิสระและได้รับการติดตั้งบนแพลตฟอร์มฮาร์ดแวร์ที่แตกต่างกันตั้งแต่ปี 2547
Agile Project Execution เป็นวิธีการของ YOKOGAWA ในการดำเนินโครงการทั้งหมดอย่างคุ้มค่าโดยการกำจัดของเสีย
ด้วยการเปิดตัว CENTUM VP R6 ใหม่ซึ่งเป็นแพลตฟอร์มโซลูชันที่เกินขีดความสามารถของระบบควบคุมการผลิตทั่วไปลูกค้าสามารถใช้ประโยชน์จากคุณสมบัติใหม่ ๆ เช่น Network-IO ที่ให้การแยกฮาร์ดแวร์และซอฟต์แวร์ออกจากกันและ Automation Design Suite ใหม่
ในช่วงทศวรรษที่ผ่านมา บริษัท ต่างๆได้ใช้เทคโนโลยีการขุดเจาะที่แปลกใหม่ในการสกัดก๊าซและของเหลวจากการก่อตัวของชั้นหินที่หาได้ง่ายในอเมริกาเหนือ เมื่ออุตสาหกรรมได้รับประสบการณ์อัตราการผลิตยังคงเพิ่มขึ้นตามการใช้เทคโนโลยีที่ดีขึ้นในการค้นหาทรัพยากรและลดเวลาจากการสำรวจไปจนถึงการผลิต
yi-MAC ย่อมาจาก YOKOGAWA Innovative Main Automation Contractor:
- ควบคุมขอบเขตและกำหนดเวลาข้ามแพ็คเกจได้อย่างสมบูรณ์
- การตระหนักถึงความคาดหวังของลูกค้า
- จุดเดียวของความรับผิดชอบ
- ให้บริการโซลูชั่นแบบครบวงจร
Network-IO สามารถช่วยลดโครงการได้โดยการลดระยะเวลาที่ต้องใช้ในการนำส่วนทางกายภาพของ ระบบควบคุมของกระบวนการ ไปใช้ ระบบที่มี I / O ที่สามารถกำหนดค่าได้ช่วยให้ "การรวม" ที่ยืดหยุ่นซึ่งการกำหนดค่าซอฟต์แวร์ของระบบสามารถโหลดลงในระบบฟิสิคัลได้ในช่วงท้ายของโปรเจ็กต์
ความสามารถในการส่งมอบขอบเขตความสามารถในการดำเนินโครงการอย่างเต็มรูปแบบกำลังมีความสำคัญมากขึ้นกว่าเดิมสำหรับซัพพลายเออร์ระบบอัตโนมัติที่ต้องการแข่งขันในระดับโลก ซัพพลายเออร์ระบบอัตโนมัติในกระบวนการมีความสามารถในการดำเนินโครงการอยู่ในระดับหนึ่ง แต่เพิ่งมีซัพพลายเออร์และผู้ใช้ปลายทางเริ่มตระหนักถึงผลกระทบทางเศรษฐกิจที่แท้จริงซึ่งความสามารถในการดำเนินการที่แม่นยำและครอบคลุมสามารถมีต่อความสำเร็จของโครงการอัตโนมัติและต้นทุนวงจรชีวิตของโรงงาน
เมื่อโครงการดำเนินการตามวิธีการของผู้รับเหมาระบบอัตโนมัติหลัก (MAC) วิศวกรรม ส่วนหน้าและการออกแบบ (FEED) จะดำเนินการก่อนขั้นตอนการส่งมอบจริงเช่นการออกแบบการใช้งานการตรวจสอบและการจัดส่งเพื่อระบุความเสี่ยงล่วงหน้าและลดความเสี่ยงใน ขั้นตอนการจัดส่งผ่านการกำหนดมาตรฐานของฟังก์ชันและส่วนประกอบพื้นฐาน
อุปกรณ์เครื่องมือวัดและอุปกรณ์ทำหน้าที่แทนพืชเช่นตาหูจมูกลิ้นและผิวหนังซึ่งมีหน้าที่รับผิดชอบต่อประสาทสัมผัสทั้งห้าและทำหน้าที่เหมือนระบบประสาทส่วนกลางและสมองที่ทำเพื่อมนุษย์ ความน่าเชื่อถือและความพร้อมใช้งานของอุปกรณ์และอุปกรณ์ดังกล่าวเป็นข้อกำหนดที่สำคัญที่สุดของลูกค้า
วิดีโอ
ข่าวสาร
-
Press Release | Projects May 12, 2017 โยโกกาวา ชนะคำสั่งจัดหาบ้านวิเคราะห์สำหรับโครงการ RAPID ของมาเลเซีย
- โมเมนตัมสร้างขึ้นสำหรับธุรกิจ การบูรณาการ ระบบการวิเคราะห์กระบวนการของเรา -
คุณต้องการข้อมูลเพิ่มเติมเกี่ยวกับบุคลากร เทคโนโลยี และโซลูชั่นของเราหรือไม่ ?
ติดต่อเรา