돌발 사고 및 치명적인 고장을 방지하기 위한 예측 유지보수 솔루션
고장 없이 계속 가동되는 제조 설비 실현
제조 현장의 노동력 부족과 장비 노후화로 인해 '예측 유지 보수'의 필요성이 커지고 있습니다. 각종 센서로부터 데이터를 수집하여 장비의 성능 저하나 고장을 예측하고 안전하고 안정적인 운영을 위한 필수 기술인 예측정비를 최적의 시점에서 유지보수를 수행할 수 있도록 도와줍니다.
다중 I/O 아날로그 센싱 유닛 VZ20X는 디지털로 변환되지 않은 장비의 데이터들을 시각화하기 위해 안정적인 센싱을 수행합니다. IoT와 AI를 통합하여 VZ20X는 장비의 열화 징후를 식별하고 예측 유지보수를 용이하게 합니다. 예측 유지보수는 장비의 문제를 최소화하고 설비 유지보수의 생산성과 효율성을 향상시킵니다.
VZ20X는 다음 사용자의 요구를 충족합니다. :
- 산업기계(생산설비)를 적시에 점검 및 교체하고자 하는 사람
- 사용하고 있는 산업기계에 부담을 주지 않으면서 개선하고자 하는 사람
- 산업기계의 돌발 사고 및 치명적인 고장을 방지하고자 하는 사람
>> VZ20X 연결을 위한 샘플 프로그램 다운로드
PC나 PLC에 연결하여 데이터를 수집할 수 있는 샘플 프로그램입니다. VZ20X가 제공하는 편리함을 경험해 보십시오.
*아날로그 센싱 유닛 VZ20X는 아시아, 유럽, 북미, 남미 및 아프리카에서 판매됩니다. 단, 일부 지역은 제외됩니다.
제조 현장에 필요한 예측 유지보수
기존 제조 현장에서 유지보수는 고장 후에 수행되는 '시정 유지보수'와 주기적으로 수행되는 '예방 유지보수'로 진행되고 있습니다. 그러나 이러한 유지보수 방법은 노동집약적인 유지보수 작업과 갑작스러운 장비 고장을 방지하지 못하는 등의 문제를 가지고 있습니다. 인력난이 심화되고 있는 제조현장에서 이러한 유지보수 방법은 큰 부담이 되고 있습니다.
이상징후를 미리 감지하여 그에 따른 유지보수를 하는 '예지보전'이 현재 주목받고 있는 이유입니다. 예측 유지보수를 진행한다면 이상징후가 보이는 장비에 대해서만 유지보수가 수행되므로 유지보수 작업과 관련된 작업 시간과 비용이 크게 줄어듭니다. 게다가 갑작스러운 장비 고장으로 인한 가동 중지 시간을 최소화하여 가동 시간을 향상시킬 수 있습니다.
예측 유지보수가 가능한 VZ20X
VZ20X는 다양한 아날로그 센서 신호를 고속, 고정밀, 고전압으로 동시에 측정할 수 있는 세계 최소형 센싱 리모트 I/O 유닛입니다. 측정된 데이터는 이더넷을 통해 모니터링을 수행하고 장비 및 시설 상태를 지속적으로 평가하는 상위 시스템으로 전송됩니다. 장비 고장 또는 열화 같은 이상 징후를 신속하게 감지하여 장비 가동 중단으로 인한 가동 시간 감소 및 안전 문제를 해결함으로써 예측 유지 보수가 실현됩니다.
OpreX
OpreX는 Yokogawa의 산업 자동화(IA) 및 제어 비즈니스를 위한 포괄적인 브랜드이며 관련 기술 및 솔루션의 우수성을 나타냅니다. 이 제품은 OpreX 범주 아래 정렬된 OpreX 구성 요소 제품군에 속합니다.
Details
Benefits of VZ20X Installation
The VZ20X is equipped with the ideal features for implementing predictive maintenance. This section describes some of the benefits of installing the VZ20X at your manufacturing site.
Converting Signs of Deterioration Into Digital Data Allows Optimal Timing of Replacement and Inspection
The VZ20X collects data from multiple sensors simultaneously at high speed and with high accuracy to visualize signs of equipment deterioration. Combined with Yokogawa Electric’s proprietary AI, equipment anomalies and signs thereof can be analyzed and detected at an early stage. This makes possible CBM (condition-based maintenance), in which maintenance is performed at the optimal timing in accordance with the condition of the equipment. This reduces the man-hours required for inspection and parts replacement, helping to achieve labor savings in maintenance work.
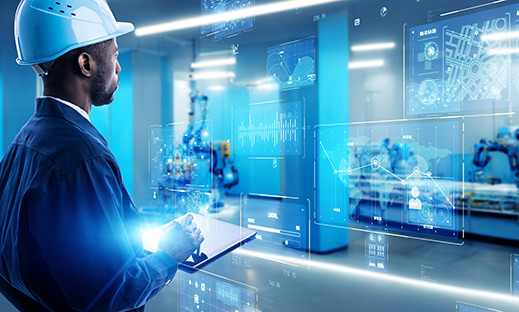
Easy Installation on Existing Equipment to Acquire Diagnostic Data and Make Improvements
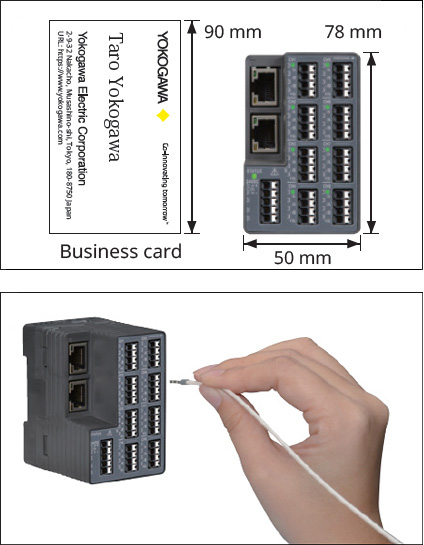
The VZ20X is one of the world’s smallest analog sensing units, shorter and narrower than a business card, and weighing less than 200g. Because it can fit in the gaps between production equipment, it can be easily replaced, minimizing the need for extensions or modifications to existing facilities. It can be applied to evaluating the performance of batteries installed in tight spaces inside a vehicle, or to predictive maintenance of unmanned vehicles.
Furthermore, it employs a push-in connection mechanism that allows installation simply by inserting a ferrule terminal, eliminating the need for special tools. These advantages make it easy to install on any piece of equipment without requiring much space or wiring, allowing predictive maintenance and evaluation of products and components.
High Noise Resistance Helps Ensure Safe Operation
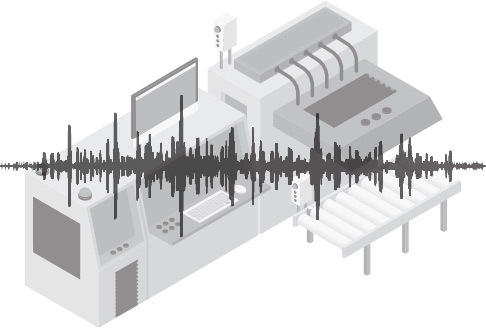
The VZ20X provides stable data measurement thanks to its improved isolation between input channels and noise resistance. Because it can measure highly reliable data even when simultaneously measuring multiple channels or in environments where noise is likely to occur, it is able to accurately analyze the cause of equipment failures. This reduces the number of cases of imprecise maintenance, which in turn reduces the man-hours required for maintenance work.
Also, when using VZ20X in production quality evaluation, safe and reliable testing can be performed because it is less susceptible to the characteristics of products and components and the testing environment.
High-Speed and Highly Accurate Sensing Detects Signs of Failures Before They Occur
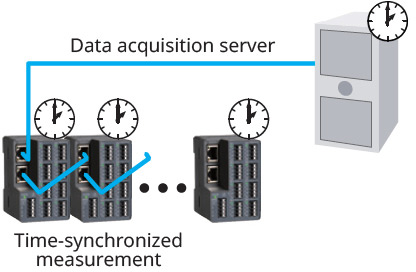
A single VZ20X unit can measure 8 channels of analog inputs at high speed with a sampling cycle of 1 ms. It supports simultaneous measurement by up to 15 units across 120 channels, helping to enable predictive maintenance at manufacturing sites where large amounts of equipment and many sensors are in operation. It is also capable of extremely precise measurement with synchronization accuracy of ±100 µs, measurement accuracy of ±0.05%, temperature measurements accurate to within ±0.16°C, and voltage measurements accurate to ±1mV. In this way, high-speed and highly accurate measurements that do not miss even the slightest changes in the equipment enable the prediction of failures.
Monitors Equipment Status With Support for All Kinds of Analog Sensors
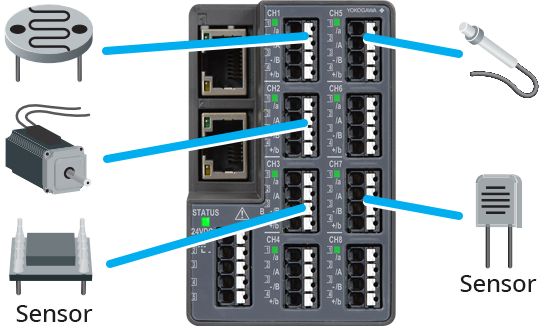
DC voltage, unified signal, 4-wire resistor, thermocouple (TC), and 3-wire/4-wire RTD can be measured with a single unit. The use of analog sensors that support these inputs allow a variety of data to be measured, eliminating the need to use numerous data measurement devices for different kinds of sensors.
Accurate Sensing Even Without a Power Outlet
Using the USB Type Detection Disable feature, the VZ20X can be powered by sources other than USB Type-C. Powering the device from a PC’s USB Type-A port eliminates the need for an external 24V DC power supply or power cable, reducing installation and wiring costs. Moreover, by connecting the VZ20X to a commercially available PoE (Power over Ethernet) splitter, it is possible to supply power using an Ethernet cable.
Examples of VZ20X Applications
VZ20X can be used in CBM (condition-based maintenance) at manufacturing and logistics sites.
Manufacturing Plants: Predictive Maintenance of Manufacturing and Logistics Equipment
Recently, manufacturing plants have been making use of automatic guided vehicles and other advanced automation systems to reduce the number of workers on production lines. However, there are still many pieces of analog equipment for which it is difficult to successfully detect signs of deterioration, leading to issues of reduced operating rates due to sudden failures.
The VZ20X is extremely small and lightweight, about the size of a business card, and can be retrofitted to existing analog equipment. Furthermore, when combined with Yokogawa Electric’s data logging software (GA10), real-time OS controller (e-RT3 Plus), and its proprietary AI, highly accurate data collection, monitoring, anomaly detection, and causal analysis can be achieved. Properly timed maintenance reduces the number of man-hours required to troubleshoot problems associated with equipment stoppages, contributing to improved uptime and labor savings.
Specifications
Main Body: Analog Sensing Unit: VZ20X-1N1NDD
Item | Specification |
---|---|
Number of inputs | 8 channels |
Input types | DC voltage, unified signal, 4-wire resistor, thermocouple, and 3-wire/4-wire RTD |
Data acquisition interval | 1 ms (fastest), 8 channels simultaneous measurement |
Meas. synch. accuracy | Within ±100 μs (between input channels, between units) |
Measurement accuracy | 0.025% of FS (with DC voltage, and power supply frequency noise removal filter enabled) |
Withstanding voltage | 3,000 VAC (50 Hz/60 Hz) 1 min. (between analog input channels, analog input-to-internal circuit) |
Power supply | 24 VDC or USB |
Operating temperature/humidity | -10–55°C (DIN rail-mounted), -10–50°C (on desktop installation) /5–90% RH |
Wiring | Push-in terminal, Ferrule terminal |
Size | Height (H) 78 x width (W) 50 x depth (D) 65 mm |
Ethernet communication | 2 ports, protocol: Modbus/TCP, GA10 dedicated protocol |
Installation | DIN rail-mounted, On desktop installation |
Standards | ![]() |
VZ Configurator
Item | Description |
---|---|
Parameter settings | Input range/scale, Ethernet communication conditions |
Monitor function | Real time monitoring Self-diagnosis |
Maintenance | Firmware update Input adjustment |
자료실
Customers want to improve maintenance by predicting failures of existing durable equipment. However, existing equipments do not have enough space, and it is not easy to increase the number of sensors needed to grasp the condition.
To address this issue, the VZ20X’s compact size allows it to be installed between equipments, and data collection can be easily monitored via Ethernet (Modbus/TCP).
VZ20X
Production stoppages caused by sudden malfunctions in production equipment are a serious loss of opportunity.
Equipment inspections to prevent failures are often carried out based on the experience and sense of maintenance personnel, and are fraught with risks.
Customers want to perform maintenance appropriately in accordance with the timing of regular stoppages and the condition of the equipment, not as a rule of thumb for maintenance personnel.
To meet these expectations, the VZ20X can be installed compactly in the gaps of existing production equipment, and by accurately capturing the status changes of each, it contributes to reducing the risk of them.
When maintenance work of production equipment or trouble occurs, customers want to check the situation at the site immediately.
They also want to prepare easily for that (building a measurement system).
In response to these demands, the VZ20X and GA10 make it easy to construct a DATA collection system (on-site confirmation system) and quickly check the status of production equipment.
Customer can cover long-distance area and the VZ20X is very compact to install into small space of any equipment .
Due to revisions and additions to regulations, pumps used in water, sewerage, and drainage systems require flexible modifications and additional measurement points in their performance inspections.
In response to these changes in the environment and circumstances, the compact size of the Multi-Sensing Remote I/O Analog Sensing Unit VZ20X reduces the burden of expanding and reconstructing production and test equipment to fit the current installation environment.
Customers want to improve maintenance by predicting failures of existing durable equipment. However, existing equipments do not have enough space, and it is not easy to increase the number of sensors needed to grasp the condition.
To address this issue, the VZ20X’s compact size allows it to be installed between equipments, and data collection can be easily monitored via Ethernet (Modbus/TCP).
Since performance evaluation tests of inverter drive motors are susceptible to noise, equipment with high noise resistance is required. Also, if the number of measurement points is large, a multi-channel measuring instrument that satisfies the measurement will be costly.
The VZ20X is noise-resistant and safe for accurate DATA collection even on noise-prone measurement targets such as inverters.
It is hard to go back and forth between the office floor and the test floor to check the bearing durability status.
That round trip time is wasteful and a heavy burden on man-hours. If you have more than one test floor, that's even more of a burden.
The VZ20X and GA10 make it possible to build simple monitoring systems. The system also enables remote monitoring of manufacturing and testing sites, contributing to reducing the burden on the site.
DATA of several production equipment in a semiconductor manufacturing factory is currently being checked by field workers, and the checking is in a difficult situation. Therefore, there is a growing demand for centralized monitoring within the factory.
The VZ20X allows installation to take advantage of existing space.
In addition, the GA10 contributes to labor saving in the field by remote monitoring.
When maintenance work of production equipment or trouble occurs, customers want to check the situation at the site immediately.
They also want to prepare easily for that (building a measurement system).
In response to these demands, the VZ20X and GA10 make it easy to construct a DATA collection system (on-site confirmation system) and quickly check the status of production equipment.
In the painting process of automobile parts, failure or corrosion of electrodes can lead to quality degradation.
In addition, the current lack of electrode condition monitoring has resulted in the replacement of electrodes in a short period of time, a problem that is extremely costly.
To address these issues, we monitor the deterioration of production facilities and contribute to the realization of maintenance tailored to the conditions of the equipment.
Customers want to monitor the amount of electricity consumed by each production equipment in order to conserve energy in the factory, but it is not easy to install a measurement system in existing equipment, even from the installation and wiring conditions.
The VZ20X's compact size allows it to be installed for existing conditions. Accurate sensing also contributes to the visualization of power usage at production equipment.
Customers want to improve maintenance by predicting failures of existing durable equipment. However, existing equipments do not have enough space, and it is not easy to increase the number of sensors needed to grasp the condition.
To address this issue, the VZ20X’s compact size allows it to be installed between equipments, and data collection can be easily monitored via Ethernet (Modbus/TCP).
The PLC in the existing injection molding machine does not have a recording function, but you want to add a function to record the production DATA and equipment condition DATA. Customers also want to easily realize these functions.
In response to these requirements, the VZ20X performs DATA collection of PLC and analog sensors, and the GA10 provides on-site monitoring and recording to support safer operations.
In recent years, customers of processing equipment used in food and pharmaceutical manufacturing have increasingly requested visualization of equipment conditions.
This is because we do not know the current state of our production facilities, and maintenance depends on individual experience and intuition.
By accurately collecting DATA with VZ20X and visualizing the status of equipment, it is possible to understand the current status and perform appropriate maintenance according to the condition of the equipment.
Customers want to improve maintenance by predicting failures of existing durable equipment. However, existing equipments do not have enough space, and it is not easy to increase the number of sensors needed to grasp the condition.
To address this issue, the VZ20X’s compact size allows it to be installed between equipments, and data collection can be easily monitored via Ethernet (Modbus/TCP).
Customers want to improve maintenance by predicting failures of existing durable equipment. However, existing equipment do not have enough space, and it is not easy to increase the number of sensors needed to grasp the condition.
To address this issue, the VZ20X’s compact size allows it to be installed between equipment, and data collection can be easily monitored via Ethernet (Modbus/TCP).
the VZ20X installed near sensors such as temperature, humidity, and vibration, and enables automatic collection of data via the factory LAN. The data collection, monitoring and management can be automatically and regularly monitored with the data logging software GA10. As a result, it contributes to reducing the workload of workers.
Downloads
Brochures
- VZ20X Analog Sensing Unit (5.1 MB)
Instruction Manuals
General Specifications
- Model VZ20X Analog Sensing Unit (918 KB)
Technical Information
Drawings
- Model VZ20X Analog Sensing Unit (271 KB)
기술 및 솔루션, 요꼬가와에 대한 자세한 정보를 찾고 계십니까?
견적 및 기술문의