Las plantas químicas dependen de procesos de producción continua y por lotes, cada una de los cuales impone diferentes exigencias para un sistema de control. Un proceso continuo exige un sistema de control robusto y estable que no falle y provoque el cierre de una línea de producción, mientras que en un proceso por lotes el énfasis se centra en tener un sistema de control que permita una gran flexibilidad para realizar ajustes a fórmulas, procedimientos y otros elementos. Ambos tipos de sistemas necesitan ser administrados en el historial de calidad del producto disponible, así como tener la capacidad de ejecutar operaciones no rutinarias. Con el respaldo de su extenso portafolio de productos, un equipo de experimentados ingenieros en sistemas y una red global de ventas y servicio, Yokogawa ofrece una solución para cada proceso productivo.
-
Productos a base de químicos
Yokogawa ha estado sirviendo al mercado de productos químicos a granel globalmente y ha obtenido reconocimiento como líder en este mercado. Con productos, soluciones y especialización en la industria, Yokogawa entiende su mercado y las necesidades de producción y trabajará con usted para proporcionarle una solución confiable y rentable durante el ciclo de vida de su planta.
-
Specialty & Fine Chemical
This page introduces Yokogawa's messages and solutions for the Specialty and Fine Chemicals industry, showcasing our specialized offerings and expertise.
-
Biocombustibles
Para combatir el calentamiento global, la producción y el consumo de biocombustibles ha aumentado a nivel mundial. Como proveedor líder de soluciones de control y medición en las industrias químicas, de petróleo, así como otras, Yokogawa ha desarrollado tecnologías que pueden ser usadas para asegurar la confiabilidad y la producción eficiente de bioetanol y otros tipos de combustibles renovables.
-
Petroquímica y a granel
Las empresas productoras de petroquímicos, productos inorgánicos o productos intermedios se encuentran bajo una presión constante para equilibrar los costos y los márgenes al suministrar productos a sus clientes de manera oportuna y eficiente, manteniendo al mismo tiempo operaciones seguras y conformes con la normativa. Además, las empresas químicas tienen que adaptarse a la constante fluctuación de los precios de los insumos y la energía y tener la capacidad de proveer al mercado la combinación de productos más rentable.
Yokogawa ha estado supliendo las necesidades de automatización del mercado de productos químicos a granel globalmente y ha obtenido reconocimiento como líder en este mercado. Con productos, soluciones y especialización en la industria, Yokogawa entiende su mercado y las necesidades de producción y trabajará con usted para proporcionarle una solución confiable y rentable durante el ciclo de vida de su planta.
Detalles
Cadena de valor de la industria química
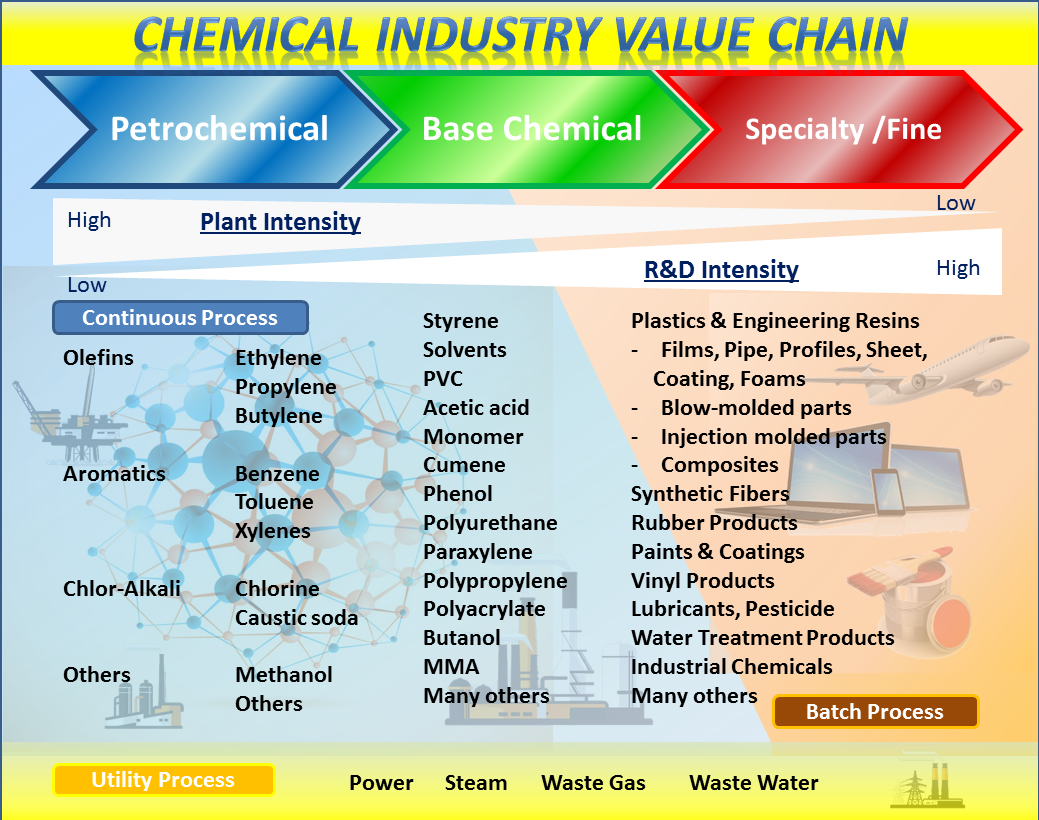
Yokogawa Electric Corporation introdujo los primeros DCS del mundo en 1975, que ganaron una rápida popularidad entre muchos clientes del sector químico en todo el mundo. De esta manera, Yokogawa ha estado contribuyendo a la operación segura y estable de las plantas de los usuarios como un proveedor líder de soluciones de control de procesos en esta industria.
A medida que los procesos, los productos y la cadena de valor de la industria química se vuelven más complejos y sofisticados, lo mismo ocurre con los requerimientos de los clientes. Yokogawa continúa suministrando soluciones y servicios industriales que satisfacen esas necesidades, aprovechando su caudal de experiencia y especialización en este ámbito. También hemos lanzado varias soluciones novedosas, como la gestión de energía para optimizar la operación en las plantas.
Como proveedor integral, Yokogawa continuará cumpliendo las expectativas de sus clientes en la industria química suministrando soluciones de automatización de avanzada tecnología.
Excelencia en la producción
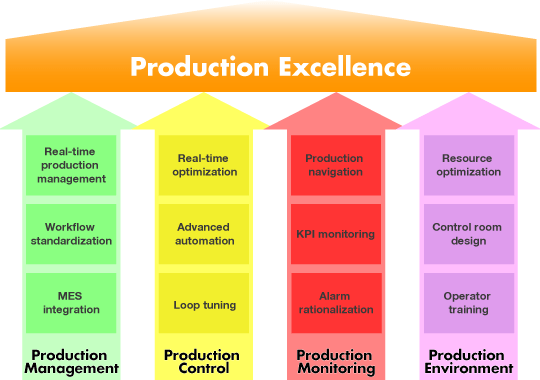
Gestión de la producción
- Integración de MES
El campo de los sistemas de ejecución de manufactura (MES) engloba una serie de sistemas independientes que ejecutan tareas de programación y otras funciones. La conectividad entre los sistemas es un factor decisivo y fundamental para que la gestión de la producción sea ágil. - Sistematización del flujo de trabajo
Los flujos de trabajo de producción deben estar definidos y supervisados para garantizar la fiabilidad de la gestión de la producción. La sistematización de los flujos de trabajo es especialmente eficaz en compañías que cuentan con varios centros de producción. - Gestión de la producción en tiempo real
Se requiere una gestión de la producción completamente en tiempo real para agilizar el ciclo planear, hacer, verificar y actuar (PDCA) de la producción.
Control de la producción
- Sintonización en lazo
El control de identificación de procesos (PID) desempeña un papel fundamental en el control de procesos. Para asegurar un control de procesos estable se requiere una sintonización adecuada, que además es un requisito previo para un control de nivel avanzado. - Automatización avanzada
El control de procesos avanzado y los sistemas de navegación basados en el conocimiento son factores clave para una operación bien automatizada. - Optimización en tiempo real
Se puede lograr la optimización en todas las áreas de la planta con un optimizador en tiempo real que emplee rigurosos modelos de cálculo.
Monitoreo de la producción
- Racionalización de alarmas
Es recomendable contar con una estrategia de gestión de alarmas que esté basada en la reconocida guía núm. 191 de la Asociación de Usuarios de Equipos y Materiales de Ingeniería (EEMUA). El análisis de la causa raíz de las alarmas también es una estrategia eficaz para lograr una racionalización de alarmas exitosa. - Monitoreo de indicadores clave de desempeño (KPI)
Se debe monitorear una amplia variedad de indicadores clave de desempeño (KPI) por cada persona. El monitoreo de indicadores clave de desempeño (KPI) requiere hacer comparaciones con las metas y profundizar en los datos para obtener información detallada. - Navegación en la producción
El sistema debe administrar de manera correcta las tareas de producción. Monitorear el avance de las tareas es un puente valioso entre la planificación y la fabricación que facilita la cooperación en la gestión de la producción.
Entorno de la producción
- Capacitación de operadores
Los sistemas de capacitación de operadores permiten que los operadores adquieran experiencia en el manejo de diversas situaciones, como fallas de los equipos, así como en la ejecución de arranques y otras operaciones de rutina. Ayuda a los operadores a modernizar sus habilidades. - Diseño de la sala de control
Para el diseño de la sala de control se requiere tomar en consideración todos los aspectos del entorno de trabajo, como ergonomía, seguridad, facilidad de comunicación, funcionalidad, automatización de sistemas y política de empresa. - Optimización de recursos
Una sala de control central es deseable para que el entorno de la producción sea eficaz. Todas las unidades que tengan relación con la producción deben ubicarse cerca de esta para garantizar una buena comunicación. Además de centralizar la sala de control, puede considerarse la optimización de recursos humanos y otras actividades para lograr la excelencia en la producción.
Recursos
- El PRM permite un enfoque de mantenimiento preventivo en donde el mantenimiento se puede programar y llevar a cabo antes de que falle un dispositivo de campo.
- El Exaquantum recoge los datos de la planta de la CENTUM VP para generar una variedad de reportes sobre el proceso de polimerización.
ADMAG AXG Magnetic Flowmeter Helps to Optimize Production Throughput and Reduce Energy Consumption in Chlor-Alkali Plant
Syngenta aimed to promote sustainable agriculture as a social responsibility through digital transformation. Syngenta selected Yokogawa to start the smart manufacturing transformation journey.
Kuraray Engineering provides IoT big data analysis solution in collaboration with Yokogawa.
Collaborative process data analysis achieved a high level of quality stabilization at a customer site.
Osaka Gas Chemicals selected Yokogawa to solve long-standing problem at carbon fiber manufacturing process.
Osaka Gas Chemicals established unique problem-solving method using Yokogawa's process data analytics solution.
Nippon Sanso Vietnam JSC (NSVN) equipped a digitalized supply-chain management system to optimize efficiency of industrial gases delivery.
The ODMS (Order delivery management system) was rapidly developed using the DevOps agile approach in collaboration with NSVN and Yokogawa.
- Sumitomo Seika achieved the quality stabilization by cross-department project.
- The fusion of process knowledge and data analysis technology was a key to the success.
- Based on a careful review of all operational procedures and operator roles and configured new SOPs in Exapilot.
- As a result, SFC has been able to reduce operator workload, improve product quality, and reduce production losses.
Operator Training Simulator helps improve human reliability in a young plant of PetroVietnam Ca Mau Fertilizer.
PVCFC and Yokogawa implemented OTS for third-party control and safety system as a team.
- Stable operation and proactive maintenance were realized at new coal-chemical plant in China.
- Yokogawa engineers ensured a successful and efficient commissioning and startup.
- El Sistema Legacy fue reemplazado con CENTUM VP y ProSafe-RS en la planta de PTA en Indonesia.
- Los Parámetros PID fueron importados al CENTUM VP sin cálculos complejos.
Ube Corporation Europe and Yokogawa co-created the Field Assistant mobile solution.
Field Assistant innovates inspection patrol, supervisory management, and O&M efficiency in the plant.
- La Excelencia Operativa a través de la Maximización de Activos, utilizando DCS, SIS, Analizadores, y los Instrumentos de Campo de Yokogawa
- El CENTUM VP PCS y ProSafe-RS SIS se integraron utilizando el mismo entorno de ingeniería.
- Casi 60 cromatógrafos de gases y un gran número de otros tipos de analizadores en varias casas analizadores.
The AFCO project is a showcase of the good coordination between Yokogawa Middle East, Yokogawa Thailand, Yokogawa Singapore, and Yokogawa Electric Corporation. Yokogawa Middle East and Yokogawa headquarters both were involved in the project execution.
- Using the CENTUM CS 3000 system, many kinds of plant key performance indexes are calculated and analyzed to produce further improvements.
- During plant start-up, PRM helps the customer's engineers perform all the loop checks.
- Yokogawa provides CENTUM CS 3000, Exaquantum and PRM solutions for China's largest refinery/petrochemical complex.
- Process data management by Exaquantum is a key issue in the petrochemical complex.
- El concepto de Principal Proveedor de Instrumentos (MIV) fue aplicado en este proyecto para reducir el costo total de la ingeniería del proyecto.
- Este consistía en DCS, SIS, todos los instrumentos, válvulas de control y sistema de medición de tanques en condiciones de trabajo con el consultor de administración de proyectos (PMC) y el EPC.
- La integración del CENTUM CS 3000 con el ProSafe-RS mejora la Seguridad y la Confiabilidad de la Planta.
- El paquete PRM de Yokogawa administra más de 500 dispositivos de campo HART incluyendo las válvulas de control.
- El sistema de control de producción del CENTUM CS 3000 contribuye a la producción sencilla de HDPE.
- El desafío para este proyecto de reemplazo fue completar el trabajo y poner en marcha el nuevo sistema CS 3000 tan pronto como fuera posible, manteniendo el tiempo de inactividad al mínimo.
- CS 3000 efficiently controls and monitors coal gasification process.
- Once an operator selects "Start", the necessary instructions are sent to all plant equipment via the sequence control.
- La implementación rápida de la integración de los sistemas CENTUM CS 3000 y ProSafe-RS.
- El sistema altamente confiable CENTUM CS 3000 también ha ayudado a TOL a mantener una alta productividad en esta planta.
- Migration from Micro-XL and CENTUM CS 1000 to CENTUM CS 3000 Improves Reliability.
- Operations at this plant, which runs more than 330 days per year, are carefully managed by the CENTUM CS 3000 DCS and the CS Batch package.
- Sistema de Paro de Emergencia Certificado
- Reducción sustancial de los trabajos de mantenimiento
- La configuración del sistema con espacio reducido
- Las etapas del sistema
- CS Batch is used to automate a wide range of Reichhold's batch processes and multi-product/multi-path processes.
- Using PRM, process engineers can immediately find out the status of every field device without having to do an onsite inspection.
- Cumplir con las normas funcionales de seguridad IEC 61508/JIS C 0508
- Proactivamente introducir tecnologías de vanguardia
- Adaptarse a las licencias de la planta, los requisitos de seguridad, confiabilidad y de mantenimiento
- Mejorar las funciones de monitoreo y operación del sistema de paro de emergencia
Samsung Petrochemical Co. Ltd. (SPCL), a major Korean petrochemical company, produces 700,000 tons per year of purified terephthalic acid (PTA) at its Daesan plant. PTA, a white powder substance that is produced by oxidizing and refining para-xylene, is a precursor to polyethylene terephthalate (PET), a polyester material that has excellent thermal resistance and wear resistance and is widely used as a substitute for natural cotton fibers and in film packaging, beverage bottles, tire cords, paints, adhesives, and other applications.
- Installation of Exaquantum PIMS package improves efficiency of process data management.
- Improve quality and yield through proactive maintenance of plant assets.
- Introduction of CENTUM CS 3000 maximizes productivity and improves product quality at special polymer plant.
- A major improvement as a result of this project is that butadiene monomer recovery efficiency jumped huge.
- CENTUM CS 3000 distributed control system to control the ethanol plant and it's utility boilers
- Batch processes that require careful automated control for maximum efficiency and product quality
- El CENTUM VP Batch sustituye al sistema Legacy y mejora la eficiencia de producción en la planta acrílica.
- La capacidad del CENTUM VP Batch puede manejar la administración de procedimientos para el manejo de los informes por lotes y la administración de unidades.
- El paquete de lotes de CENTUM VP mejora la productividad.
- Reducción de la carga de trabajo del operador y un funcionamiento seguro.
- Migración del sistema de plantas de Polietileno y Petroquímica de PetroChina Dushanzi.
- La renovación incluyó la desafiante creación de las especificaciones de diseño de función (FDS), así como las pruebas FAT y SAT.
- El CENTUM CS 3000, altamente confiable, reemplaza al sistema Legacy y automatiza la operación de la planta de lotes.
- Trabajando en conjunto, Hanwha Chemical y el personal del proyecto de Yokogawa Corea completaron este trabajo a tiempo y según lo programado.
- Yokogawa suministra un STARDOM y FAST/TOOLS para la planta piloto de biomasa.
- El FAST/TOOLS es una solución SCADA "todo en uno" que funciona como un historiador de datos.
- Implementation of multivariable optimizing controllers and robust quality estimators within a record short period
- 3% rise expected in CCR feed amount
- La tecnología de FOUNDATION™ Fieldbus fue introducida para realizar mantenimiento predictivo y preventivo.
- El ISAE sirve para mejorar la confiabilidad del diagnóstico y el ajuste de parámetros, utilizando los datos recogidos por el PRM.
- Como el contratista de automatización principal (MAC) para este proyecto de construcción de planta, Yokogawa Brasil diseñó, instaló, y puso en marcha una solución de control e instrumentación integrada.
- Yokogawa Brasil completó la puesta en marcha de estos sistemas antes de lo previsto y la producción de polímeros verdes se inició tan sólo una semana más tarde.
- Kaneka Corporation has urgently needed to implement countermeasures that would reduce this facility's energy costs.
- Optimization of control strategy helps BTG plant save energy and operate more efficiently.
- Yokogawa's CENTUM VP and PRM improve efficiency at new nylon plant in Thailand.
- At the plant startup stage, PRM was used together with FieldMate to thoroughly check all loops.
- At the company's Ulsan resin plant, six Exaquantum servers were connected to CENTUM CS 3000 and other vendor's systems.
- KKPC needed to expand its SBC capabilities and improve production efficiency at its plants.
- CENTUM CS 3000 and Exaquantum PIMS improve production efficiency at Chinese synthetic rubber plant.
- Exaquantum provides data on long-term trends needed to make improvements to plant processes.
- Up to 90% of all manual tasks can now be carried out automatically.
- Increasing productivity by means of partially automated start-up and load change procedures.
- 16,000 FOUNDATION Fieldbus devices
- Main Automation Contractor (MAC)
- DCS anywhere concept integration with site SAP system
- Long term maintenance contract
- Sustainable development
- Proyectos de Re-instrumentación en la Planta HDPE para Reemplazar los Instrumentos Neumáticos Legacy y los PLC’s integrados con CENTUM CS 3000 PCS y ProSafe-RS SIS
- Los dispositivos de campo HART se pueden monitorear desde la sala de control central con el paquete de administrador de recursos de la planta (PRM), lo que permite un enfoque de mantenimiento más predictivo y proactivo que reduce el costo total de adquisición.
- Single 'look and feel' operator interface for the DCS and NCS
- Fast and controllable integration cycle
- High speed hybrid compressor control solution
- Reduced OPEX for the compressor operation by replacing old and obsolete PLCs with a modern hybrid control platform
- All logistics of raw materials, intermediate products and final products are controlled and managed by MAS.
- MAS enables Operational Excellence with its seamless interface to enterprise resource planning system.
- Implementation of AOA package for improved grade-change operation
- Dramatically reduced operators' workload and transient products, as well as sharable operation know-how
- Exapilot automates comlex and non-routine decoking process of NCUs.
- Operator workload has been drastically reduced.
- Exapilot was built up as e-SOP system based on the standard operating procedures and the know-how of experienced operators.
- e-SOP system improved the quality and productivity in the performance chemical plant in China.
- Cambio en un día
- Mejora de la productividad y la rentabilidad
A medida que aumenta la demanda mundial de alimentos, los fertilizantes juegan un papel esencial en la mejora de la productividad agrícola. El Nitrógeno OCI (en adelante OCI) es un productor líder de fertilizantes minerales y el mayor productor mundial de melanina, los cuales se utilizan para hacer adhesivos y resinas para una amplia gama de aplicaciones, tales como paneles de muebles, pisos laminados, revestimientos, pinturas y plásticos.
Taiyo Nippon Sanso Corp. estaba buscando un sistema que pudiera ser fácilmente adoptado a su arquitectura de planta. Por las siguientes razones, el sistema STARDOM de Yokogawa con el controlador autónomo FCN y el software SCADA basado en VDS Web fue seleccionado como su sistema de control para una planta Water-18O y otras instalaciones.
Tsurumi Soda Corporation,Yokohama,Kanagawa Prefecture, Japan
- CENTUM VP y SIS fueron seleccionados para el proyecto de ampliación de las instalaciones de la BTX Evonik Oxeno.
- CENTUM proporciona la transparencia operativa, y el diagnóstico más eficiente de los compresores que son el corazón de la instalación.
Yokogawa's network healthiness check service helped the customer identify what they need to protect against cyber-attacks.
By “visualizing” network traffic in control system, the customer was able to detect unauthorized communication in their system.
- A Japanese petrochemical plant leverages FDT/DTM-compliant intelligent field devices and Yokogawa's PRM asset management system for maintenance efficiency.
- The customer aims to improve maintenance efficiency further by introducing condition-based maintenance (CBM).
- Yokogawa assisted in the project implementation by providing design review, calculation modifications, pre-commissioning, training of operators and engineers, commissioning and post implementation review.
- Shell Global Solutions and Shell Deer Park Management were completely satisfied with the way the project was implemented and with the results achieved.
- TOK decided to start local production of high-quality photoresist for semiconductor manufacturing near its customers in Taiwan.
- The MES with traceability comparable with pharmaceutical manufacturing is one of the factors to win the trust of its customers.
- Yokogawa's operational performance program bench mark service enhanced the automation performance at the chemical plant.
- Operator stress was dramatically reduced by identifying the causes of excessive manual interventions.
- Yokogawa joined forces with Air Liquide to co-innovate the step-by-step revamping plan based on Air Liquide's specific requirements.
- Customer was satisfied that Yokogawa was able to deliver its solutions on time and on budget.
- The Advanced Process Control application implemented on the Scotford MEG unit helped control the plant with less variation, resulting in maximized TEG production and reductions in overall steam consumption.
- TEG production increases were greater than originally estimated and the prices for steam and TEG used in the post-implementation study were reduced significantly.
- FDT compliant FieldMate manages a wide variety of digital process instruments of multi-vendors.
- The SNF engineers can manage the complete lifecycle of assets and configure devices by using FieldMate.
- Kuraray EVAL and Yokogawa prepared carefully for the expansion and modernization of the CENTUM system.
- Management of 400+ fieldbus instruments by Yokogawa's PRM plant resource manage also helped the project to proceed smoothly.
The TC series of temperature controllers is perfect for controlling the heating temperature of sealing parts and the temperature of sealing rolls (pre-heating) in a variety of different wrapping machinery.
Accurate reactor level measurement enables flow optimization to enhance yield.
Yokogawa's Paperless Recorder series offers a multi-point touch panel to improve intuitive operator control with predictive monitoring for early detection during sake production and managing brewery wastewater.
Avoid flashing issues while loading cryogenic liquids with safe, reliable, and accurate density fluid measurements utilizing Yokogawa’s industry-leading Coriolis flowmeter to eliminate measurement issues and increase the accuracy of inventory.
Prevent costly downtime and process equipment failures with real-time pressure monitoring. Yokogawa’s Sushi Sensor is the optimal choice for industries depending on bottled gas in essential procedures.
Ensure minor issues in Vinyl Chloride Production can be identified before becoming serious problems with Yokogawa’s In-Situ Gas Analyzer TDLS8000 and Probe Type Analyzer TDLS8200.
Boosting efficiency in Chlor-Alkali Plants with the ADMAG Magnetic Flowmeter provides accurate, stable flow measurement for Brine and Caustic in Chlor-Alkali electrolyzer cells, improving production efficiency and reducing energy consumption.
Remote monitoring of supply pump conditions in the agitation process reduces operator rounds and contributes to stabilization of the product quality.
Yokogawa’s Sushi temperature sensor is a cost-effective, reliable, long-range wireless communication for monitoring and recording to boost reliability, and also able to configure the network with redundant gateways for chemical manufacturers.
Reducing waste in the separator and electrode drying furnaces with Yokogawa’s distributed temperature sensors ensure comprehensive monitoring of thermal events in real-time.
Enhance the efficiency and safety of your vapor recovery systems and flare/vent headers with Yokogawa's cutting-edge Tunable Diode Laser Spectrometers – the TDLS8000 and TDLS8220. Elevate your oxygen measurement capabilities with our interference-free analyzers, providing direct measurements. Experience unparalleled reliability, ensuring minimal upkeep and secure operations without the need for system shutdowns.
Enhance the efficiency and safety of your vapor recovery systems and flare/vent headers with Yokogawa's cutting-edge Tunable Diode Laser Spectrometers – the TDLS8000 and TDLS8220. Elevate your oxygen measurement capabilities with our interference-free analyzers, providing direct measurements. Experience unparalleled reliability, ensuring minimal upkeep and secure operations without the need for system shutdowns.
In the plants of food and beverage manufacturers, there are times when monitoring and recording of production equipment is necessary inside clean rooms. This is an introduction to monitoring and recording in clean rooms using paperless recorders.
The Yokogawa DTSX1 Fiber Optic Heat Detector protects your equipment against abnormal heat events while being more affordable than other heat detection solutions.
La configuración del transmisor de nivel puede tomar mucho tiempo. Los transmisores DPharp tiene la función de un software avanzado eliminando esta tarea que toma tiempo. Con talleres de mantenimiento cada vez más pequeños, la búsqueda de equipos que nos permiten hacer más con menos se convierte en una prioridad.
- Agua industrial
- Agua y agua residual
- Altamar (FPSO, FSRU y FLNG)
- Bocas de pozo y separación
- En cubierta
- Energía
- Exploración, desarrollo y producción
- Perforación
- Petroquímica
- Petróleo y gas
- Procesamiento y fraccionamiento
- Producción flotante, almacenamiento y descarga (FPSO)
- Química
- Refinación
- Specialty & Fine Chemical
- Terrestre
- Transporte, distribución y comercialización de petróleo y gas
- Tratamiento de aguas
- Tratamiento de aguas residuales
- Tubería
- Térmico
Hot Spot Monitoring for Safety with a Fiber Optical Temperature Sensor
Recientemente, las legislaciones de contaminación del aire, como la Ley de Aire Limpio para reducir la cantidad de contaminación del aire están aumentando en todo el mundo. La Ley de Aire Limpio aborda numerosos problemas de la calidad del aire. Uno de estos problemas es la lluvia ácida causada por las emisiones de dióxido de azufre y las emisiones de óxidos de nitrógeno de las centrales eléctricas alimentadas con combustibles fósiles y otras fuentes industriales y de transportación.
The GX20 and GX90UT offer an average value computation function making it ideal for controlling temperature and other fluctuating phenomena. The operating status can be controlled in real time, providing operating cost reductions.
In flue gas desulfurization systems that use magnesium hydroxide (Mg(OH)2) slurry, the consumption of the desulfurization agent (Mg(OH)2) is controlled by using online pH analyzers. A great concern in the pH measurement is heavy staining of the pH electrodes by the Mg(OH)2 slurry. To ensure accurate measurement, frequent cleaning of the electrodes with an acid is required, adding to both maintenance workload and cost.
Industry:Chemical, Power
El ADMAG AXR es el primer medidor de flujo magnético de doble cableado del mundo que emplea el único "Método de Excitación Doble Frecuencia," logrando el 0.5% de tasa de mejor exactitud en su clase y una excelente estabilidad de medición del proceso. Además, la nueva tecnología clave del AXR, "logra el mismo nivel de inmunidad al ruido como el tipo de 4 cables bajo la condición de cambio de fluido y suministra el desempeño suficiente para lograr el requerimiento de aplicarlo en el bucle de control.
Control of sodium chloride (NaCl) concentration at a salt dissolver where solid salt is dissolved in water, is highly important because of the electrolysis efficiency. A conventional way of measuring the concentration of supersaturated NaCl solution had been performed by using non-contact type sensors (e.g., γ-ray density meter) since NaCl, impurities, and precipitates are in the solution.
There are various methods for continuous fabric dyeing as well as dye fixing. When dye is directly applied, steaming (heat treatment) is required. At present the pad-steam method is widely used for continuous dyeing. To ensure stable product quality, the humidity in the steamer is kept at a constant level.
Electrolysis plants create hydrogen and chlorine from a brine solution. Chlorine gas generated from the anolyte of the electrolysis tank generally contains between 0.5 to 2.0 vol% H2O. The sample is then cooled and filtered to remove brine, subsequently coming out as wet chlorine gas. The wet gas is sent to a drying tower where it is treated with sulfuric acid to get moisture down to the ppm level.
Process liquid analyzers such as pH meters, conductivity meters, ORP meters, and density meters play an important role at electrolysis plants in the control of concentrations of various process solutions. This requires both precision and stability under harsh conditions that include highly corrosive substances, high temperatures, and many impurities.
- Effeciently controls the inlet valve and blow-off valve when the compressor starts and stops.
- During steady operation, controls the inlet valve so that the amount of discharged compressed air becomes constant (flow control)
- Surging: Load decreases, the amount of discharge flow and pressure drop, and a limit is exceeded, possibly destroying the compressor.
- Emergency interlock circuits for petrochemical plants and other facilities must be independent of the main control system.
- The YS80 Rack Instrument interfaces not only with field devices and upstream control systems, but also with emergency interlock circuits guarding against process abnormalities.
Risk management is crucial when expanding your business.
El rendimiento del DPharp en aplicaciones de medición de nivel de la batería de la caldera es superior a los transmisores de presión de capacidad metálica. Un mejor desempeño se puede atribuir al diseño único del sensor resonante de silicón con resonadores duales.
With industrial and economic development comes increasingly large and advanced power plants and factories. Nevertheless, we find many cases where the original cables, cable tunnels, and other components of the power infrastructure have languished under continuous operation.
In limestone-gypsum flue gas desulfurization systems, the consumption of a desulfurization agent (lime) is controlled using online pH analyzers.
Fired heaters are used for various processes in oil refining and petrochemical plants.
Heat exchangers are devices that provide the flow of thermal energy between two or more fluids at different temperatures. Heat exchangers are used in a wide variety of applications. These include power production; process, chemical and food industries; electronics; environmental engineering; waste heat recovery; manufacturing industry; and air-conditioning, refrigeration, and space applications. Yokogawa offers a means to control heat exchanger leakage and prevent costly maintenance, repair and downtime with an easy-to-use, virtually maintenance-free condensate conductivity measurement method.
Both bulk and finished inventories are stored in distributed tank farm remote from the site operations. These are difficult to instrument due to the infrastructure cost involved. These are then monitored daily by patrol rounds. While effective, this method does require a large skilled labor force to monitor all of tanks. This can impose an additional risk when the stored medium is of a hazardous nature.
Install a YTMX580 on the side of the rotating furnace that can wirelessly transmit measured values from multiple temperature sensors.
Storage tanks are used in a variety of industries ranging from holding crude oil to holding feedstock for vinyl chloride monomer (VCM).
- Manual temperature reading requires walking about 130 m and climbing up and down elevated sections of the dryer stages.
- Multiple temperature measurement points along the various stages of the dryer require many cables to the control room.
- Very high humidity.
Ion Exchange is a method for the exchange of ions between two electrolytes or between an electrolyte solution and a complex molecule. In most cases the term is used to denote the processes of purification, separation, and decontamination of aqueous and other ion-containing solutions with solid polymeric or mineralic ion exchangers.
- Temperature is monitored to maintain consistency of the viscous fiber entering the drum.
- Existing system requires manual temperature readings.
- Wired temperature measurement is not available because the tank is rotating.
El hidrógeno es el elemento atómico más simple y más pequeño. El agua, ácidos, bases, y la inmensa familia de compuestos orgánicos contienen hidrógeno. A pesar de que el hidrógeno no es corrosivo, puede causar problemas para los transmisores de presión a través de su permeabilidad.
- Wireless temperature measurement
Gateway x1, transmitter (YTA) x1, repeater x2 (The 2 repeaters are for redundancy) - Extended antenna to circumvent obstacles and improve the radio path for stable measurement (communication was unstable when the height of the antenna was low).
NH3 injection lowers NOx in stack flue gas, boosts dust collection efficiency, and prevents erosion. Precise measurement and control of NH3 are crucial to avoid excess use, which increases costs and causes odors. The TDLS8000 solves these issues with direct measurement for effective NH3 management.
ISA100 wireless temperature and pressure transmitters with orifice plates allow:
- No cabling installations or maintenance.
- Small amount of hardware and simple equipment implementation means minimizing potential vandalism.
ISA100 Wireless Monitoring
- Gateway x1, Temperature Transmitter (YTA) x3, Pressure Transmitter (EJX) x1, Repeater x1
Gateway is installed at control room and 3m height extended antenna is set.
- Temperature Transmitter (YTA) and Pressure Transmitter (EJX) are installed at each monitoring point.
- Repeater is installed on high position.
En el mantenimiento y la administración de plantas industriales, monitoreo del pH de las aguas residuales / ORP es a la vez una obligación legal y una necesidad necesaria para la protección del medio ambiente. El Monitoreo sin estar atento puede llevar a consecuencias graves.
Yokogawa’s Process Liquid Analyzers series help pigment producers achieve a more reliable and accurate analysis of pH during industrial bioprocesses, improving product quality with less total operation costs.
Pressure measurement of tubeless tyres to monitor the air loss is one of the key performance tests in the tyre manufacturing units. Relocation of tyres from one testing rack to the other for various tests and frequent movement of the testing setup for conditional tests to various locations calls for cable free implementation for ease of handling.
To defray energy costs, many industrial plants have their own boilers to generate steam to produce a portion of their energy needs. In addition to generating power, the steam may also be used directly in plant processes or indirectly via heat exchangers or steam jacketed vessels.
Optimizing ORP measurements for reliable chlorine control in cooling tower applications is essential for maintaining water quality, preventing corrosion, and ensuring work health and safety.
In this eBook we explain how to improve fired heaters safety & efficiency by controlling combustion using TDLS technology. Download it now and learn:
- The 4 top industry challenges related to fired heaters
- How to efficiently and safely manage combustion
- How TDLS technology can improve operational excellence in fired heaters
Download this eBook and learn:
- The top challenges that drive reinstrumentation
- How to plan for and achieve a successful project
- Best practices in identifying your project scope
- 5 ways to improve operator effectiveness
- Different scenarios and best practices for updating, migrating or replacing process controls, safety systems, and instrumentation in plants
Plants increasingly are turning to machine learning (ML) and artificial intelligence (AI) to recognize precise patterns in sensor data. The technologies ease differentiating between normal and abnormal equipment behavior and also detecting specific patterns that lead up to failures — and, so, enhance capabilities for predictive maintenance.
Read this report to learn how more insightful data and better analyses can boost uptime.
This eBook explains why implementing IIoT based digital operator monitoring solutions for autonomous anomaly detection enhances operations.
A Basic Guide to Accurate & Reliable Flow Measurement.
In this Yokogawa RAP Best Practices eBook, you’ll discover how our wealth of knowledge about Integrated Safe Systems and Control of Work is available to help you and your teams design and implement a system that best suits your needs.
Visual MESA© is a steam system optimization and management computer program that was originally developed at Chevron and now marketed by Nelson & Roseme, Inc. Visual MESA is currently used at refinery and chemical manufacturing sites to optimize the overall site steam system and the parts of the electrical system that economically trade off with the steam system.
This paper will explore significant optimization variables and constraints commonly encountered in refinery steam system optimization, the strategies Visual MESA uses to deal with them.
In the course of more than twenty years as an engineer involved directly in utility related projects in a number of industries, I have seen a great variety of energy efficiency projects and programs covering the entire spectrum of efficacy. The Deer Park, Texas, plant of the Rohm and Haas Company has a unique energy management program that has proven to be highly successful. This program has resulted in a 17 percent reduction in energy use on a per pound of product basis, saving 3.25 trillion btus and $15 million each year! This article discusses this program, its history, successes, and the unique characteristics that have contributed to those successes.
Get Connected: Advancing Workers and Capabilities
In this whitepaper by Shahzad Khan, you will learn how to use collaborative, integrated, optimized, and autonomous operations to integrate your systems and emerging performance metrics.
By downloading this whitepaper you will learn how to:
- Connect operations, systems, processes, maintenance, and goals
- Empower employees digitally, to improve their decision-making skills
- Gain access to immediate improvements to production efficiency
The whitepaper discusses the importance of safety culture in achieving a smarter and safer working environment. It highlights statistics on work-related accidents and diseases, the cost of poor safety culture, and the need for a true safety culture achieved through company leadership.
On-site digital champions can drive your operation towards data integration and a more aligned way of working.
In general, refineries exhibit a very good potential for real time monitoring and optimization using Visual MESA Energy Management System.
Based on our extensive experience, overall benefit in the range of 2% to 5% of the total energy cost can be achieved. Expected project payback is always less than one year.
Digital twins are dynamic digital representations that enable companies to understand, predict and radically reorient their business processes.
Outline
- Introduction
- What is Energy Optimization
- How does a Real Time Online Energy Management System based on Visual MESA work
- Calculation Foundation for Key Performance Indicators
- Visual MESA implementation at Saudi Kayan (A SABIC Affiliate) (SK)
- Optimization Actionable Items
- Economic Benefits
- Relevance of Visual MESA RTEMS for SK's Sustainability Initiative
- Conclusions
The REPSOL company had in mind the improvement of the control on one of their chemical reactors. A feasibility study for the implementation of an Advanced Control technique (Predictive Control for temperature control for chemical Reactors - PCR) for a batch reactor for Polyols production has been performed. The proposed technique PCR is based on a dynamic model of the unit which makes the prediction of the process variables behaviour.
When selecting a Level Measurement device, what to consider in order to be accurate and repeatable?
This paper will not describe just all the features of the software or fully explain on-line optimization technology. The objective of this work is to present some interesting facts and lessons from the experience of implementing a cost based optimization program at thirty oil refineries and petrochemical complexes, around the world, since 1997. This paper will focus on the key optimization variables and constraints in steam system optimization, how they should be handled and how the human and organizational aspects can be addressed.
Industrial facilities where power and steam is produced (i.e., Cogeneration) exhibit a very good potential for real time monitoring and optimization using Visual MESA Energy Management System.
Based on our extensive experience, overall benefit in the range of 2% to 5% of the total energy cost can be achieved. Expected project payback is always less than one year.
Visual MESA was successfully applied to many industrial facilities worldwide, several of them operating steam and power generation networks of different complexity and capacity but all with energy cost savings.
This paper discusses real industrial examples in which the sitewide utilities system of refinery and petrochemical Sites are optimized with a real time, on line, industrially proven software. Experiences gained during more than 20 years of industrial projects deployed worldwide are commented (Refs. 1 to 10 are related to some recent projects). Main project steps are explained and critical details to be taken into account to assure successful use and proper technology transfer are presented. Specific case studies will be discussed in the paper.
Utilities and energy systems are often the major source of SOx, NOx and CO2 emissions, therefore, emissions control and the management of credits and quotas are tightly interrelated with energy management.
In the case of refineries, chemical and petrochemical plants, energy represents the main cost (second to feedstock) and therefore its reduction has become a bottom line business decision. The energy systems at these sites are inherently complex, with the emissions cost analysis and limits compliance introducing an additional factor to the complexity of the energy costs reduction challenge.
Process plants use different type of fuels, they often operate cogeneration units, their steam networks consist of several pressure levels, there are different types of energy consumers and there are emission limits to be observed. Import or export of electricity in deregulated markets, which could also be traded off with more or less CO2 and other contaminant gaseous emissions, increase the optimization problem complexity.
After a feasibility study, Repsol YPF decided to apply a model-based predictive controller to a batch reactor producing polyols. The predictive controller for reactors (PCR) is a set of control modules that are designed to face most of the reactor configurations. The important increase of production is a consequence of the better handling of the reactor temperature. Here's a description of the unit and control objectives, methodology, project steps, results and the corresponding benefits.
Big and complex industrial facilities like Refineries and Petrochemicals are becoming increasingly aware that power systems need to be optimally managed because any energy reduction that Operations accomplish in the producing Units could eventually be wasted if the overall power system cost is not properly managed. However, process engineers always attempted to develop some kind of tools, many times spreadsheet based, to improve the way utilities systems were operated. The main drawback of the earlier attempts was the lack of data: engineers spent the whole day at phone or visiting the control rooms to gather information from the Distributed Control System (DCS) data historian, process it at the spreadsheet and produce recommendations that, when ready to be applied, were outdated and not any more applicable.
This paper addresses some of the root causes for issues and discusses the best practices that will help to avoid project failures. Main project steps are explained and critical details to be taken into account to assure successful use and proper technology transfer are discussed. It also presents real industrial examples in which the whole utilities system cost of a production Site (i.e., steam, fuels, boiler feed water and electricity) is optimized with a real time, online, industrially well established software.
Utilities and energy systems are often the major source of SOx, NOx and CO2 emissions, therefore, emissions control and the management of credits and quotas are tightly interrelated with energy management. In the case of refineries, chemical and petrochemical plants, energy represents the main cost (second to feedstock) and therefore its reduction has become a bottom line business decision. The energy systems at these sites are inherently complex, with the emissions cost analysis and limits compliance introducing an additional factor to the complexity of the energy costs reduction challenge.
The energy systems, the steps for the implementation of Visual MESA and several features of the model are described in this article, with a focus on the use of the software for the calculation of energy-related KPIs. The EMS implementation project is discussed and the main conclusions relative to the reduction in operating costs are also presented.
Experiences gained during more than 20 years of industrial projects deployed worldwide are commented. Main project steps are explained and critical details to be taken into account to assure successful use and proper technology transfer are presented. Specific case studies will be discussed in the paper. Open loop vs Closed loop implementation is also presented.
Rohm and Haas Company is one of the world's largest manufacturers of specialty materials, including adhesives, sealants, coatings, monomers, electronic materials, inorganic and specialty solutions, and ion exchange resins. Founded in 1909 by two German entrepreneurs, Rohm and Haas has grown to approximately $6 billion in annual revenues.
Alarm management is not just a project that has a start and end date; it's a continuous cycle. Once the alarm system has been reviewed and improvements have been identified, we must check that controls are in place to ensure the alarm system remains functional. The key is to ensure that the system is continuously monitored and any changes are fully documented. There are seven key steps for alarm management. Rationalization is one of those critical steps.
- Altamar (FPSO, FSRU y FLNG)
- En cubierta
- Exploración, desarrollo y producción
- Petroquímica
- Petróleo y gas
- Procesamiento y fraccionamiento
- Producción flotante, almacenamiento y descarga (FPSO)
- Química
- Refinación
- Refinación, procesamiento y almacenamiento de petróleo y gas
- Submarino
- Terrestre
- Transporte, distribución y comercialización de petróleo y gas
- Tubería
This paper shows how to improve distillation operations by focusing on procedure automation. It will review the importance of using procedures in distillation operations and highlights the collaboration work underway between Fractionation Research Inc. (FRI) and Yokogawa Corporation to improve procedural operations.
The worlds of process automation and production management have been converging for some time. What once used to be islands of automation and production management functionality connected through highly proprietary integration schemes that were costly to maintain have developed into integrated platforms that provide seamless data exchange between the world of automation and the plant floor, the functions of production and operations management, and integration with business level systems.
- Acero y hierro
- Agua y agua residual
- Alimentos y bebidas
- Altamar (FPSO, FSRU y FLNG)
- Biocombustibles
- Energía
- Energía geotérmica
- Energía renovable
- Exploración, desarrollo y producción
- Farmacéutica
- Papel y pulpa
- Petroquímica
- Petroquímica y a granel
- Petróleo y gas
- Productos a base de químicos
- Química
- Refinación
- Transporte, distribución y comercialización de petróleo y gas
- Tratamiento de aguas
- Tratamiento de aguas residuales
- Tubería
- Térmico
The world of process automation is governed by procedures. While we like to refer to the process industries as being largely "continuous", this could not be further from the truth. Process manufacturing is constantly in flux.
- Acero y hierro
- Agua y agua residual
- Alimentos y bebidas
- Altamar (FPSO, FSRU y FLNG)
- En cubierta
- Energía
- Exploración, desarrollo y producción
- Farmacéutica
- Papel y pulpa
- Petroquímica
- Petroquímica y a granel
- Petróleo y gas
- Procesamiento y fraccionamiento
- Producción flotante, almacenamiento y descarga (FPSO)
- Química
- Refinación
- Refinación, procesamiento y almacenamiento de petróleo y gas
- Submarino
- Terrestre
- Transporte, distribución y comercialización de petróleo y gas
From engineering to installation, commissioning, operations, and maintenance, FOUNDATION fieldbus offer significant cost reductions of 30 percent or more versus conventional analog systems. Many of these cost reductions come from the advanced functions that fieldbus offers versus analog technology.
The automation suppliers that will be successful in the long term will be those that effectively address application or industry specific problems for end users with a value proposition that cannot be ignored. These problems exist throughout the process industries today, and they won't be solved by simply offering a product, but through a combination of hardware, software, services, application expertise, and knowledge.
- Acero y hierro
- Agua y agua residual
- Altamar (FPSO, FSRU y FLNG)
- Biocombustibles
- De residuos a energía
- Energía
- Energía de biomasa
- Energía geotérmica
- Energía renovable
- Exploración, desarrollo y producción
- Farmacéutica
- Papel y pulpa
- Petroquímica
- Petroquímica y a granel
- Petróleo y gas
- Química
- Refinación
- Transporte, distribución y comercialización de petróleo y gas
- Tratamiento de aguas
- Tratamiento de aguas residuales
- Tubería
- Térmico
In ARC's view, customers need a compelling business value proposition to justify investment in any kind of automation. Vigilance and VigilantPlant were created with this in mind. Yokogawa's vision with VigilantPlant is to create an environment where plant personnel and operators are well informed, alert, and ready to take action.
- Acero y hierro
- Agua y agua residual
- Altamar (FPSO, FSRU y FLNG)
- Biocombustibles
- De residuos a energía
- Energía
- Energía de biomasa
- Energía geotérmica
- Energía renovable
- Exploración, desarrollo y producción
- Farmacéutica
- Papel y pulpa
- Petroquímica
- Petroquímica y a granel
- Petróleo y gas
- Química
- Refinación
- Transporte, distribución y comercialización de petróleo y gas
- Tratamiento de aguas
- Tratamiento de aguas residuales
- Tubería
- Térmico
Yokogawa ha recorrido un largo camino en hacer que su mensaje sea claro en el mundo de la automatización de procesos. El año pasado, la compañía se embarcó en una campaña global de marketing a gran escala para que los clientes conocieran el enfoque de la compañía en la confiabilidad del sistema, su seguridad, constancia y durabilidad. Denominado "Vigilancia", la campaña creó un mensaje unificado para la empresa y en gran medida ayudó a aumentar la difusión de la marca Yokogawa y la filosofía de la empresa.
- Acero y hierro
- Agua y agua residual
- Altamar (FPSO, FSRU y FLNG)
- Biocombustibles
- De residuos a energía
- Energía
- Energía de biomasa
- Energía geotérmica
- Energía renovable
- Exploración, desarrollo y producción
- Farmacéutica
- Papel y pulpa
- Petroquímica
- Petroquímica y a granel
- Petróleo y gas
- Química
- Refinación
- Transporte, distribución y comercialización de petróleo y gas
- Tratamiento de aguas
- Térmico
Los usuarios finales de procesos automatización están bajo más presión para hacer más con menos. La situación económica actual hace que muchos proyectos de capital de automatización estén en espera. Con los presupuestos de capital más limitados que nunca, los usuarios en lugar de enfocarse en los presupuestos de operaciones (en donde también la reducción de costos es una preocupación clave), o en las inversiones de automatización con un rápido retorno de inversión.
- Acero y hierro
- Agua y agua residual
- Altamar (FPSO, FSRU y FLNG)
- Biocombustibles
- De residuos a energía
- Energía
- Energía de biomasa
- Energía geotérmica
- Energía renovable
- Exploración, desarrollo y producción
- Farmacéutica
- Papel y pulpa
- Petroquímica
- Petroquímica y a granel
- Petróleo y gas
- Química
- Refinación
- Transporte, distribución y comercialización de petróleo y gas
- Tratamiento de aguas
- Térmico
In today's dynamic industrial marketplace, the only constant is change. Raw material costs, energy costs, market demands, environmental and safety regulations, technology, and even the nature of the labor force itself are constantly changing, and not always in predictable directions.
- Acero y hierro
- Agua y agua residual
- Altamar (FPSO, FSRU y FLNG)
- Biocombustibles
- De residuos a energía
- Energía
- Energía de biomasa
- Energía geotérmica
- Energía renovable
- Exploración, desarrollo y producción
- Farmacéutica
- Papel y pulpa
- Petroquímica
- Petroquímica y a granel
- Petróleo y gas
- Química
- Refinación
- Transporte, distribución y comercialización de petróleo y gas
- Tratamiento de aguas
- Térmico
La migración de DCS de una refinería proporcionó una oportunidad para volver a configurar y consolidar las salas de control y sistema de administración operativo.
With work injuries on the increase, migrating to digital platforms to address worker safety has become a priority. Digital transformation simplifies the integration of new digital applications such as alarm lifecycle management, functional safety lifecycle management, shift team effectiveness, and permit-to-work.
Differential pressure level measurement has an enemy- temperature. Temperature can have a negative effect on the accuracy of level measurement. This article covers why temperature has this effect and how it can be reduced.
With fired heaters, users hope to get greater efficiency and reduced emissions but often are disappointed. Given the number of fired heaters operating every day and their importance in the process industries, any improvements realized across the board will have huge impacts. More units can reach their potential with some simple changes in work practices and technology upgrades.
July 2011
Process plants are run according to operational procedures. These procedures consist of a set of tasks that are executed in a consistent manner to achieve a specific objective, such as starting up, shutting down or transitioning a unit as part of making a product.
September 2008
Yokogawa is helping a large chemicals site in China manage product transfer by road, ship and pipeline.
March 2006
The new CSPC (CNOOC and Shell Petrochemicals Company Limited) petrochemical complex at Daya Bay in southern China is one of the world's largest process industry projects (see box, Figure 1 and Table). It has a control system to match. Process Worldwide spoke to Johan Veerman, principal instrument and process control engineer at CSPC, about the challenges of managing such a huge job.
In times of abnormal operations, systems are configured to produce lots of data – humans are not configured to handle or interpret them. However, when presented with the right information, in the right context, during an abnormal condition, humans are able to do things machines cannot.
The Wyoming Trona Ore Mine and Refinery upgrade from Yokogawa Centum CS3000 to CENTUM VP-R5 involved two domains, 21 RIO and FIO field control stations, 17 operator stations, 6 engineering stations and 8 different plant servers
ISA S88.01 provides great benefit to users and vendors by solidifying batch operating models and standardizing batch control terminology. On the other hand, as befits an industry-wide standard, ISA S88.01 leaves great flexibility for individual users to apply their own project practices and implementation methodology. Even when utilizing ISA S88.01 models and terminology, many pitfalls remain for those who implement batch controls and recipe management without thinking ahead. Real-world project experience has demonstrated a number of design and implementation "lessons" which might be overlooked to the eventual grief of the batch engineer.
The S88.02 draft standard defines a means for depicting procedural control in master and control recipes. This depiction method is called a Procedural Function Chart (PFC). This standard depiction is based on the requirements of S88.01, technical report ISA-TR88.0.03-1996, user requirements, previous standards and commonly used procedure depiction methods in use today. PFCs can provide a common basis for the exchange of recipes, reduce the learning curve between control systems, and establish a common ground for improved human communication. This paper provides a brief overview of the development of PFCs, the rules for their use and some of the benefits expected by their adoption in the industry.
The case study in this paper illustrates the value of integrating front-end scheduling with a batch control system. Recipe changes, and addition of recipes, occur frequently in the target process. However, since both scheduler and batch packages were designed with the ISA-S88.01 model in mind, these packages could be tightly coupled (well integrated) – and, as a result, it is easy to add or change recipes. The front- end scheduler is not limited to performing scheduling; it also provides an easy-to-grasp real-time production status display which can help enhance efficiency and productivity.
As batch processes are automated, it is common to leave certain less essential field devices without automatic actuators. Thus, the initial control design must accommodate both automated and manual activities. Later, the manual field devices may be automated, either one-at-a-time or in related groups as equipment modules. These field changes, often occurring over a period of years, each require rework of the batch control logic, which can easily exceed the cost of the actuator. In response to this undesirable situation, a technique has been developed which permits the batch design to automatically modify itself, or evolve, to accommodate changes in field automation.
Six Sigma is a quality improvement methodology applied to improving any type of process. It is a methodology endorsed by and heavily integrated into several major chemical companies.
Key Performance Indicators (KPIs) are used in batch processing industries as measurements of production performance. Their use is one element in the current trend of real-time performance management. A single KPI used as the primary measurement of production can cause other dimensions of production performance lose importance. When multiple KPIs are used to measure a batch's production performance it can be difficult to reconcile differences between them for individual batches or for groups of batches. KPIs based upon meeting a target, or specification, measure absolute performance yet do not provide relative information regarding how a batch performed against its peers. The peer comparisons are important for monitoring variability of production performance, which is a critical factor in documenting ROI.
The application of DCS-based "advanced controls" is a common method of achieving enhanced performance from continuous processes such as refinery units. However, it is less widely recognized, but nonetheless true, that modern DCS systems can include other software tools for the significant improvement of batch plant productivity, product quality, and economic performance. Due to the fundamental processing differences between the two types of plants, unique batch "advanced control" features are required which are different from those used for continuous plants.
CONTROL, January 2013
Standard Automation Methodology Improves Operations and Prevents Incidents by Enabling the Sharing of Best Practices Among Operators.
ARC believes that by implementing procedural automation, many process plants can minimize variability to help ensure smooth, efficient, and safe state transitions.
Wiring temperature sensors installed in a chimney back to a control room can be challenging and expensive, so many plants and facilities are instead implementing wireless solutions, such as this Yokogawa YTMX580 8-input temperature transmitter.
Process automation in oil refineries is undergoing major changes, driven by customers frustrated by what they consider to be slow and incremental advances from the main automation original equipment manufacturers (OEMs) in the industry. ExxonMobil has become a de facto industry representative and is driving vendors like Yokogawa and others to reevaluate how large-scale automation projects are implemented.
Supervisory control and data acquisition (SCADA) systems have been part of the process industries for many decades and cyber security measures need to grow as technology advances. SCADA systems are used in oil and gas pipeline and other remote control and monitoring applications, such as electrical transmission and distribution, and water/wastewater.
Many lubricant blending businesses find themselves in a challenging situation: there are opportunities to increase their overall business volume and profits by improving production flexibility, expanding their product slate and optimizing high-margin blends. At the same time, they find themselves constrained by current manufacturing limitations. However, launching a capital project for a significant manufacturing expansion may not be possible, and it may not be necessary.
Spectrometric technology can assess many critical characteristics about products, but it has limits. It can be challenging to determine when the line has been crossed
Machines can support humans when facing a stressful situation. Using a standards-based approach can reduce the likelihood of a problem escalating.
SABIC Turns to Yokogawa TDLS Analyzers to Enhance Safety Functions and Production
Honeywell and Yokogawa have both been producing Distributed Control System (DCS) platforms for decades, and both are very active in this area. In 1975, Honeywell introduced its TDC2000 platform and Yokogawa brought out CENTUM. These two competing systems emerged from a similar place, oil refining and petrochemical industries, so they started out with similar basic concepts and use cases in mind.
The accuracy of pH measurements depends upon maintenance; maintenance frequency largely depends upon the application. Understanding and addressing the causes of pH measurement difficulties comprise key to ensuring stable and accurate readings.
Extend your differential pressure transmitter's range with affordable isolation solutions, shielding it from extreme process temperatures and corrosive fluids.
Remember, the goal is to transform your business. Data and digital technology are but means to that end.
With a testbed plant nearing full OPA system operations, the dream is becoming reality.
ESG-focused institution offers a framework and a guide for manufacturers to be sustainable.
For more YNOW2024 articles, please visit YNOW: A Yokogawa Users Conference | Control Global
While cyberattacks and countermeasures are likely to evolve forever, there’s no reason the trip can’t prove successful and satisfying.
For more YNOW2024 articles, please visit YNOW: A Yokogawa Users Conference | Control Global
Is it a harmless duck or a venomous male platypus lurking in the bushes? Trish Kerin helps identify the biases that cloud our safety judgment.
For more YNOW2024 articles, please visit YNOW: A Yokogawa Users Conference | Control Global
When it comes to digital transformation, Petronas’ Sharul Rashid wants to see more collaborative efforts.
For more YNOW2024 articles, please visit YNOW: A Yokogawa Users Conference | Control Global
Documentos y Descargas
Catálogos
- Solutions for the Chemical Operations Executive (1.2 MB)
- Temperature Sensing Solutions (673.1 KB)
- Pre-Engineered Solutions for Moisture in Chlorine (650.1 KB)
- TDLS8220 LOC (Limiting Oxygen Concentration) Infographic
- TDLS8220 LOC (Limiting Oxygen Concentration) Infographic
- Extractive Tunable Diode Laser Spectrometer TDLS8220 (5.6 MB)
- Soluciones y Productos Yokogawa en Norteamérica (3.6 MB)
- Overcome Temperature Effects for DP Level (778.1 KB)
- Differential Pressure Level Solutions (23.1 MB)
- Refining Solutions (12.5 MB)
Especificaciones Generales
Certificados
Videos
ROTAMASS is the integral and remote type Coriolis Mass Flow Meter. Both types have highly refined digital signal processing electronics, so that accurate and stable mass flow measurement is achieved.
It is the most technologically advanced mass flow meter yet. By combining the superior design of the application specific flow sensor and transmitters with the Total Insight philosophy and functionality, the flexibility of the ROTAMASS to adapt to changing requirements guarantees performance throughout the lifecycle of the process measurement.
Showcases the OpreX Intelligent Manufacturing Hub, an AI-enabled platform that enhances manufacturing with seamless data integration, intelligent reporting, optimized workflows, and advanced visualization for smarter decision-making and efficiency.
Chet Mroz, President & CEO Yokogawa North America, discusses the benefits of IoT at the 2015 ARC Industry Forum in Orlando.
How much do you know about pressure transmitters? Are you accurately, quickly and reliably measuring pressure? Ultimately, the drive of any good pressure transmitter is to get an accurate, reliable pressure measurement to the data user quickly. This video gives you the answers to your basic questions about pressure and pressure transmitters.
As a gateway to further expand Yokogawa's messaging as a One-stop Solution Business, Yokogawa has partnered up with INCIT, to introduce the S.I.R.I. framework.
Watch the film by KBC who are supporting their clients in their efforts to address climate change and sustainability.
Join this webinar to better understand which manifolds you should use for specific applications and conditions. You will learn:
- A brief history of manifolds
- An overview of the different types of manifolds that are available
- The advantages, disadvantages, and application considerations you should consider when selecting a manifold
Whether you are a safety professional, an industry leader, or someone passionate about fostering a culture of safety excellence, this on-demand webinar is a must-attend event. Join us to unlock the potential of digital technology in driving safety culture forward and ensuring the well-being of your workforce.
Here come our experts discussing the Visual MESA® Energy Management System, anticipating the future of energy management technology to reduce carbon footprints and cash outflows.
Here come our experts discussing the Visual MESA® Energy Management System, anticipating the future of energy management technology to reduce carbon footprints and cash outflows.
Addresses productivity challenges in the chemical industry and how digital field instruments can improve productivity.
This workshop provided by industry partners Yokogawa and ThreatConnect will show you a way to strategically manage cyber risk within an industrial environment. Learn how to transition from the “break/fix” model of industrial cybersecurity to a business risk management strategy through cyber risk quantification, return on investment (ROI) for industrial cybersecurity solutions calculations, and cyber risk identification.
Our experts review the theory behind flow measurement technologies. Discuss common flow application challenges and evaluate the different technologies when selecting a flow meter. They also give examples of best installation practices for successful measurements.
Sample systems are a crucial component of and have a significant impact on the performance of a process gas chromatograph analyzer. When working on sample systems, you must have a constant awareness of time delays. This fundamentals webinar will take the mystery out of lag times.
Discover how to achieve industrial autonomy step by step through one of the 75+ inspiring presentations.
Noticias
-
Nota de Prensa | Productos y Soluciones Feb 2, 2025 Yokogawa Releases OpreX Quality Management System to Accelerate DX in Quality Assurance Processes for the Manufacturing of Pharmaceuticals and Food & Beverages
- A cloud-based system that enables swift and flexible process improvements -
-
Nota de Prensa | Productos y Soluciones Oct 28, 2024 Yokogawa Enters into Sales Partnership with Sensyn Robotics for Drone-Related Services
- For safe and efficient inspections of plants and other infrastructure all over the world -
-
Nota de Prensa | Productos y Soluciones Jun 21, 2023 Yokogawa to Release OpreX Informatics Manager, Enabling Integrated Management of Experimental Data and Research Resources in the Cloud
-
Nota de Prensa | Corporativo Feb 20, 2023 Yokogawa Enters into Partnership with Radial Software Group to Provide AI-powered Viewport Software Worldwide
- Giving customers a single view of all their technical data -
-
Nota de Prensa | Proyectos Nov 14, 2013 Yokogawa Selected by Chevron Phillips Chemical for USGC Petrochemicals Project
¿En busca de información adicional sobre Yokogawa Iberia, tecnología y soluciones?
Contáctenos