Improving Profits through Tighter Control
Plant Name: North American Pulp & Paper Mill
Industry: Pulp and Paper
Product(s): Finished White Paper Rolls
Application
Among the most important measurements in a paper mill is the flow of pulp stock into the head box of the paper machine. The stock level in the head box directly affects the thickness of the stock being placed onto the forming screens and the thickness of the end product. Since there normally are variations in the thickness of the pulp stock as it is set onto the forming screens, excess stock must be used to ensure that a minimum thickness is maintained. The finished product is measured by weight and is referred to as the “basis weight” of the product. Basis weight is defined as the weight of 500 sheets of paper cut to a standard size, usually 17” x 22” for bond paper, 25” x 38” for text, offset, and coated papers, and 20” x 26” for cover papers.
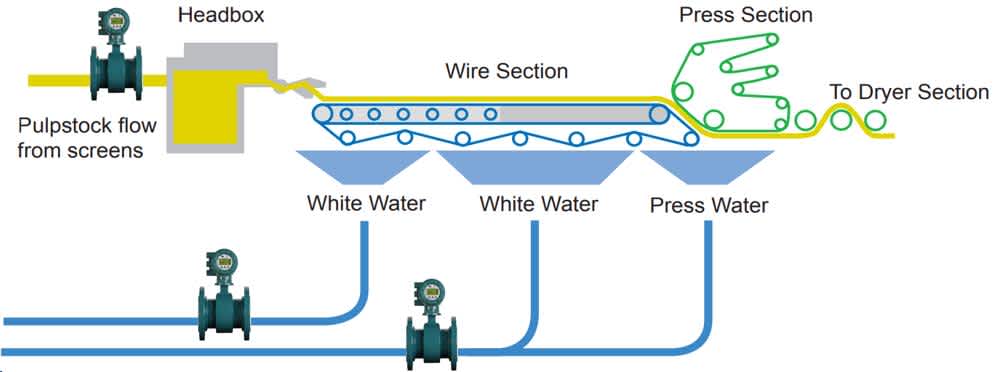
Challenges
Magnetic flowmeters are often used to measure the flow of pulp stock into the head box. Since pulp stock tends to be a noisy measurement with a magnetic flowmeter, long damping times have traditionally been used to smooth the output of the meter. Unfortunately, this results in a slow response from the meter and wasted pulp stock because the level in the head box must be kept high to avoid gaps or voids in the final product. While reducing the damping in a pulsed DC magnetic flowmeter will result in a quicker response, it can also produce a noisy signal. The noisy signal causes the valve to control the pulp stock level in the head box to chatter. That affects level control in the head box and compromises the thickness and basis weight of the end product.
|
ADMAG TI AXG |
Solution
In this application, the unique simultaneous, dual-frequency excitation method used in Yokogawa’s ADMAG TI magnetic flowmeter can enable tighter control, faster response, larger quantity of end product per batch, reduced cost, and higher profitability.
During the measurement of slurries such as pulp stock, noise is generated when pulp fiber collides with the electrode in the meter. The collision displaces a thin oxide layer that is present on most electrodes. Electrical noise occurs when the exposed metal re-oxidizes. Since the magnitude of slurry noise is greatest at low frequencies, conventional magnetic flowmeters using low-frequency DC excitation (6.25-25 Hz) can suffer the most from slurry noise. High frequency AC meters using 50 Hz or 60 Hz excitation adequately reduce slurry noise due to the high-frequency sampling rate. However, zero stability and accuracy, typically 1% of span, are unsatisfactory.
Yokogawa's dual-frequency excitation method offers the advantages of both high and low-frequency excitation. Dual-frequency excitation provides fast response time, 0.1 second, excellent zero stability, 0.30% (0.15% optional), and immunity to slurry noise.
Since dual-frequency excitation is virtually immune to the noise generated by slurry and pulp stock flows, it allows for low damping values, tighter control, and less variation of the pulp stock level in the head box. Those result in more consistent pressure from the head box to the forming screens and less variation in the thickness and basis weight of the end product. Since there is less variation in the end product, the mill can set its control point closer to the desired basis weight figure. By reducing waste, the resulting higher-end product yield from a given amount of pulp stock provides increased profit per batch. As an example, the application of an ADMAG TI AXG magnetic flowmeter at a major paper mill provided an estimated cost savings of several hundred thousand dollars per year on a large machine.
Other magnetic flowmeters on the market reduce slurry or pulp stock noise by using high power to increase the signal to noise ratio. There are several disadvantages to this approach. The extremely high drive current that is generated by the converter considerably increases power consumption. That allows fewer instruments on the electrical circuit and increases the cost of ownership. Some meters use as much as twenty times the drive current of the ADMAG TI AXG.
Drive currents of this magnitude can lead to a number of failure modes. Coil service life could be reduced and the resulting heat buildup could cause liner failures if there is no flow to dissipate the heat. These are the types of failures and cost of ownership issues that plagued AC meters in the past and drove the adoption of pulsed DC meters. The ADMAG TI AXG, on the other hand, offers the “best of both worlds:” high noise immunity that is characteristic of an AC meter and the zero stability and accuracy that are characteristic of a DC meter.
Advantages
- Lower installation cost compared to high power converters
- Longer flow tube life compared to high power converters
- Reduced OPEX and long-term cost of ownership
- Higher-end product yield per batch increases profitability
Related Industries
-
Pulp & Paper
The paper and pulp industry is highly competitive and must meet ever-changing market needs. Yokogawa helps realize energy-efficient plants which are globally sustainable.
Related Products & Solutions
-
ADMAG AXG
Magnetic flowmeters for oil & gas, chemical, pulp & paper, food & beverage, and metal & mining applications
Have Questions?
Contact a Yokogawa Expert to learn how we can help you solve your challenges.