Executive Summary
Russian Copper Smelter
Russian Copper Company has modernized its Karabash smelter in the Chelyabinsk region of Russia's Ural Mountains. An Ausmelt smelting and rotary holding furnace replaced three old shaft furnaces. The new smelting system processes approximately 460,000 tonnes/year of concentrates, producing matte for subsequent conversion to blister copper in existing Peirce-Smith converters.
Ausmelt successfully completed this project with a CENTUM CS 3000 production control system from Yokogawa Australia.
Ausmelt Limited was awarded a PACE Zenith Highly Commended Award in 2008 for the technical excellence and innovation incorporated in the plant. The Karabash smelter has also won two prestigious awards from the Russian government for environmental and ecological excellence.
The Challenges and the Solutions
Central control room of Russian Copper Company
The project required Ausmelt to provide metallurgical and operational support to the end user, which was difficult due to the distance between Ausmelt's office in Melbourne, Australia and the Ural Mountains in Russia. The solution was a remote connection via Microsoft Terminal Services across the Internet, which enables an Ausmelt technical expert in Melbourne to log on to the Yokogawa control system at the Karabash smelter and perform investigative, consultative, diagnostic, and corrective services.
The Ausmelt top submerged lance technology optimizes critical processes such as feed material dissolution, energy transfer, reaction, and primary combustion, which all take place in the slag layer in the smelter vessel. The intense agitation in the vessel caused by submerged gas injection ensures that reactions occur rapidly and residence times are low. The degree of oxidation and reduction is controlled by adjusting the fuel to oxygen ratio supply to the lance, and the proportion of reductant coal to feed. This enables the furnace to be operated at strongly oxidizing through to strongly reducing conditions. Operating temperatures range from 900°C to 1400°C. Yokogawa's highly reliable CS 3000 production control system brings high availability to the plant operation.
System Configuration
EWS : Engineering work station
HIS : Human interface station
FCS : Field control station
UPS : Uninterrupted power supply
About Ausmelt
Ausmelt Limited is a Melbourne, Australia-based supplier and developer of top submerged lance (TSL) metallurgical technology suitable for use in a wide range of applications in the non-ferrous, ferrous, and waste industries. Ausmelt has commercialized this technology globally with many applications for copper, lead, zinc, nickel, and PGM concentrates and waste materials.
There are 28 commercial furnaces in operation and three pilot plants. Three furnaces are now under construction, with a further eight furnaces in design.
About the PACE Zenith Awards
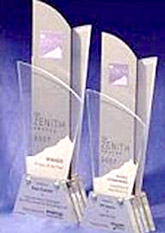
PACE Zenith Awards
Automotive and manufacturing
Chemicals and petrochemicals
Food and beverage
Oil, gas, and hydrocarbons
Metal products
Mining
Transport, power and infrastructure
Water and wastewater
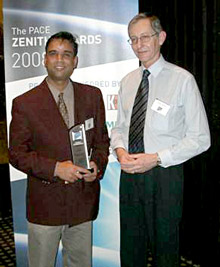
Right: Lindsay Hadland/YAU Major Accounts Manager
Left: Praveen Parashar/Ausmelt Project Engineer
Related Products & Solutions
-
Distributed Control System (DCS)
Maximize performance and profitability