Introduction
A process and apparatus for removing SO2 from a gas stream having the steps of scrubbing the SO2 with an ammonia scrubbing solution and removing any aerosols generated by the scrubbing in a wet electrostatic precipitator. The scrubbing solution is maintained at a pH between 6 and 8 to increase the speed of absorption of SO2, to Increase the ratio of sulfite to bisulfite which also facilitates the oxidation of SO2, and to avoid the need to use exotic, corrosion resistant alloys. Ammonium sulfate, a valuable fertilizer, can be withdrawn from the scrubbing solution.
Process background
Fossil fuels are burned in many industrial processes. Electric power producers, for example, burn large quantities of coal, oil, and natural gas. Sulfur dioxide (“SO2”) is one of the unwanted byproducts of burning any type of fossil fuel. It is known to cause acid rain, and to have serious negative health effects on people, animals, and plants. A great deal of research has been done to find a way to economically remove SO2 from flue gas streams before it enters the atmosphere.
The pH of the ammonium sulfate solution should be kept between about four and six. This range is the result of a compromise between competing factors. On one hand, ammonium sulfate solution is capable of absorbing SO2 more rapidly when its pH is higher. The ability to absorb SO2 better implies that the size of the scrubbing tower can be smaller, thus saving capital costs. In addition, the liquid to gas (“L/G”) ratio can be smaller, meaning less liquid will be required and operating costs will be lower.
On the other hand, higher pH levels are also associated with the release of free ammonia from solution, often termed “ammonia slip.” In addition to incurring an economic loss because of lost ammonia, free ammonia in the scrubbed flue gas reacts with uncaptured sulfur dioxide and trioxide to create an ammonium sulfate/bisulfite aerosol that is visible as a blue or white plume in the stack discharge, leading to secondary pollution problems. Controlling the amount of free ammonia in the desulfurization process is in part a function of the ammonia vapor pressure, which results from a combination of pH and levels of unoxidized ammonium sulfite that remain in the absence of sufficient oxygen. Therefore, high pH values and high levels of unoxidized ammonium sulfite promote ammonia slip.
Typical Process Example
- Name of Application / Process: Ammonia Scrubbing
- Location of Sensor mounting (location name): Tail Gas Scrubber Complex
- Operating Temp / Max.Temp: 75 to 80 deg C
- Operating Press / Max. Press: 2 to 2.5 Kg/cm2
- Type of Installation: On Pipe ( Direct mounting ) / Flow through Chamber (By pass mounting ) /
- Process Composition: Liquid - Scrub Acid,
- P2O5:105 ppm,
- AN (Ammonical Nitrogen):1326 ppm,
- UN(Urea Nitrogen):22 ppm,
- TN(Total Nitrogen):1348 ppm,
- Florine:116 ppm.
Typical process details
- Pure acetic acid service, more than 30% Water even less than<1%.
Typical problems
- The acid has very low conductivity so measurement is difficult.
Remedies
- To use a flowing special sensor to get a good electrolytic contact between reference cell and process.
Product Recommendations
Measurement System
Process Liquid Analyzer:
- 2-wire Analyzer FLXA202
Features
- Dual sensor measurement on 2-wire type analyser
- Redundant system on dual sensor measurement
- Easy touch screen operation on 2-wire type analyzer
- 4-wire Converter FLXA402
Features
- Connectable to upto five sensor
- Easily viawable color LCD
- Touch screen operation
Sensor Selection:
Yokogawa sensor SC21C-AGC55 can be the solution.
This flowing electrolyte sensors uses a ceramic reference junction, with the electrolyte (3.3 molalKCl). The flow of electrolyte through the junction, while small, remains the safest way to prevent clogging and to protect the internal reference against poisoning and diffusion.
Features for type SC21C-AGC55
- For tough application where pollution of the reference system is to be expected
- Low ionic application where the positive flow of electrolyte provides the conductivity needed to measure pH(< 50 μS/cm)
- Heavy duty pH sensitive glass.
- Flowing reference system for pollution resistance, and highly stable reference potential.
- Use in combination with the presurisableelectrolyte reservoir to obtain a positive flow towards the process (K1500YA)
Cable used:
- WU20-LT** Qty1 + WU20-PC** Qty1
Flow fitting:
- F*20 various type of flow fittings can be used
Temperature Sensor
SM60-T1 SERIES -For accurate pH measurement temperature compensation is required. Either a Pt100 or a Pt 1000 temperature electrode can be selected.
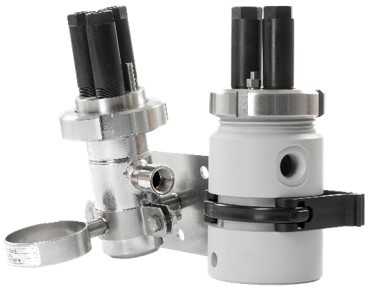
Tangible benefit
Save down time in cleaning, repeated calibration, improve end product quality.
Note: For additional information on this application contact the local Yokogawa Process Liquid Analyzer Department
Related Industries
-
Ammonia
Ammonia producers are faced with rapid growth combined with many older control systems. Growth is driven by global demand for fertilizer and supported by cheap and plentiful shale gas.
Related Products & Solutions
-
12mm pH Sensor SC25V
The SC25V is a pH sensor in a 12 mm design that includes an integral temperature element and a Liquid earth electrode.
-
2-Wire Transmitter/Analyzer FLXA202
Most flexible two-wire analyzer available
-
2-Wire Transmitter/Analyzer FLXA21
The FLEXA™ series analyzers are used for continuous on-line measurements in industrial installations. With an option for single or dual sensor measurement, they are the most flexible two-wire analyzer available.
-
Digital SMART SENCOM™ Adapter, SA11
Reusable SMART adapter, requiring only the analog sensor to be disposed of when it reaches the end of its lifetime. With the SENCOM 4.0 platform, Yokogawa delivers reduced costs and waste while contributing to its long-term business goals of a sustainable future for all.
-
Multi Channel 4-Wire Analyzer FLXA402
Available in single or multi-sensor measurement
-
pH and ORP Analyzers
Optimize field maintenance, calibration, and system configuration
Have Questions?
Contact a Yokogawa Expert to learn how we can help you solve your challenges.