A Predictive Maintenance Solution to Prevent Sudden and Critical Failures
Realizing Unstoppable Manufacturing Equipment
With manufacturing sites experiencing labor shortages and aging equipment, there is a growing need for “predictive maintenance.” Predictive maintenance, whereby data is collected from various sensors to predict equipment performance degradation or failure and perform maintenance at the optimal time, is an essential technology for safe and stable operations.
The Multi-Sensing Remote I/O Analog Sensing Unit VZ20X performs reliable sensing to visualize the status of legacy equipment that has not been converted to digital operation. By incorporating IoT and AI, the unit identifies signs of deterioration and facilitates predictive maintenance. As such, it keeps problems with equipment to a minimum and helps ensure improved productivity and efficiency in facility maintenance.
The VZ20X Meets the Needs of the Following Users:
- Those who want to inspect and replace industrial machinery (production equipment) in a timely manner.
- Those who want to add to or improve existing industrial machinery without placing a strain on it.
- Those who want to prevent minor stoppages and major failures in industrial machinery.
>>Download: Predictive Maintenance for Long-Distance Production Lines Seen through Case Studies
Digital transformation (DX) is here, and manufacturing sites are urgently transforming operations using IT to address aging production equipment and labor shortages.
In this document we introduce predictive maintenance in long-distance and complex production lines, with an example of visualization for maintenance of pumps and manifolds on production lines.
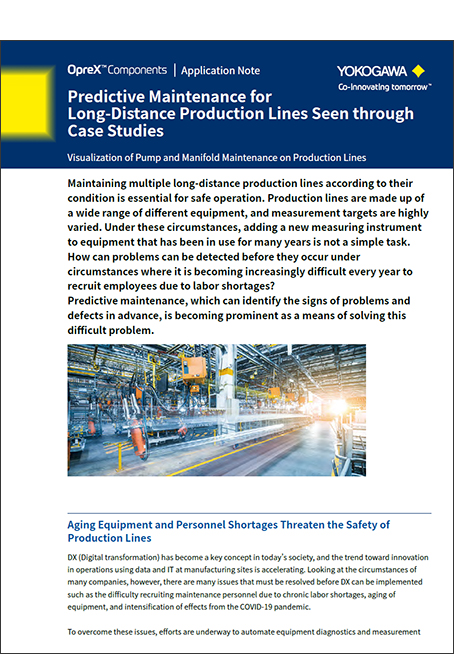
>> Download sample program for VZ20X connection
This is a sample program that collects data by connecting to a PC or PLC. Try it out to experience the convenience offered by the VZ20X.
*The analog sensing unit VZ20X is sold in Asia, Europe, North America, South America, and Africa. However, some areas are excluded.
The Predictive Maintenance That Manufacturing Sites Require
In conventional manufacturing, maintenance consists of “corrective maintenance,” performed after a failure, and “preventative maintenance,” performed periodically. However, these maintenance methods present problems such as labor-intensive maintenance work and the inability to prevent sudden equipment failures. As such, they represent a major burden for manufacturing sites, which are increasingly short on manpower.
This is why “predictive maintenance,” whereby signs of failure are detected and maintenance is performed accordingly, has been attracting attention. With predictive maintenance, maintenance is performed only on equipment that shows signs of failure, thus significantly reducing the man-hours and cost involved in maintenance operations. In addition, downtime due to sudden equipment failures can be minimized, thus improving uptime.
The VZ20X, Enabling Predictive Maintenance
The VZ20X is the world’s smallest class of sensing remote I/O unit, capable of simultaneously measuring various analog sensor signals with high speed, high accuracy, and at high voltages. The measured data is sent via Ethernet to a higher-level system that performs monitoring and constantly assesses the status of the facility. Predictive maintenance is achieved by quickly detecting signs of equipment failure or deterioration, thereby resolving issues of reduced uptime and safety due to equipment stoppages.
เกี่ยวกับ OpreX
OpreX เป็นแบรนด์ที่ครอบคลุมสำหรับธุรกิจระบบอัตโนมัติทางอุตสาหกรรม (IA) และการควบคุมของ Yokogawa และแสดงถึงความเป็นเลิศในเทคโนโลยีและโซลูชั่นที่เกี่ยวข้อง ประกอบด้วยประเภทและครอบครัวในแต่ละประเภท ผลิตภัณฑ์นี้อยู่ในกลุ่ม OpreX Components ซึ่งอยู่ในหมวด OpreX Measurement
รายละเอียด
Benefits of VZ20X Installation
The VZ20X is equipped with the ideal features for implementing predictive maintenance. This section describes some of the benefits of installing the VZ20X at your manufacturing site.
Converting Signs of Deterioration Into Digital Data Allows Optimal Timing of Replacement and Inspection
The VZ20X collects data from multiple sensors simultaneously at high speed and with high accuracy to visualize signs of equipment deterioration. Combined with Yokogawa Electric’s proprietary AI, equipment anomalies and signs thereof can be analyzed and detected at an early stage. This makes possible CBM (condition-based maintenance), in which maintenance is performed at the optimal timing in accordance with the condition of the equipment. This reduces the man-hours required for inspection and parts replacement, helping to achieve labor savings in maintenance work.
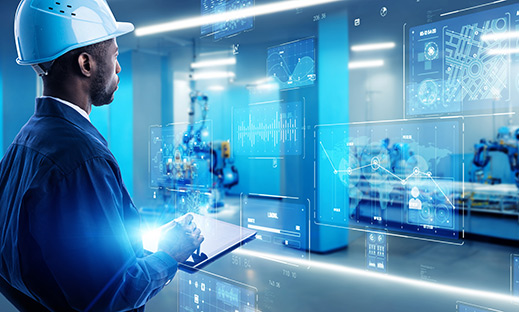
Easy Installation on Existing Equipment to Acquire Diagnostic Data and Make Improvements
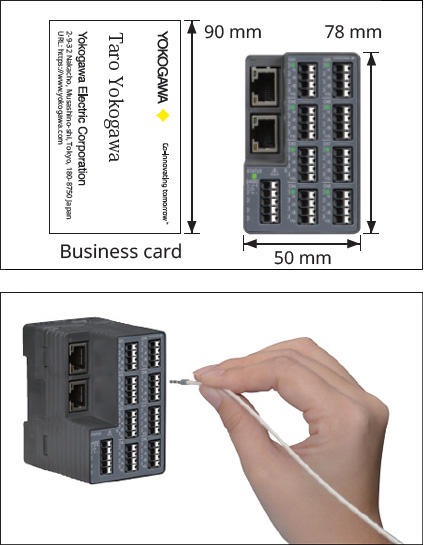
The VZ20X is one of the world’s smallest analog sensing units, shorter and narrower than a business card, and weighing less than 200g. Because it can fit in the gaps between production equipment, it can be easily replaced, minimizing the need for extensions or modifications to existing facilities. It can be applied to evaluating the performance of batteries installed in tight spaces inside a vehicle, or to predictive maintenance of unmanned vehicles.
Furthermore, it employs a push-in connection mechanism that allows installation simply by inserting a ferrule terminal, eliminating the need for special tools. These advantages make it easy to install on any piece of equipment without requiring much space or wiring, allowing predictive maintenance and evaluation of products and components.
High Noise Resistance Helps Ensure Safe Operation
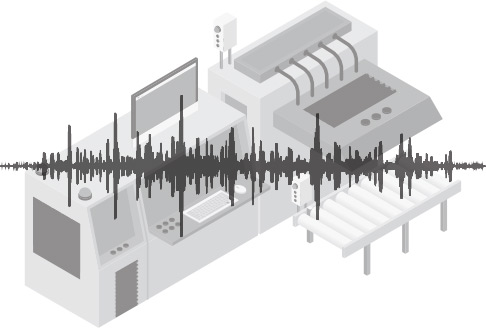
The VZ20X provides stable data measurement thanks to its improved isolation between input channels and noise resistance. Because it can measure highly reliable data even when simultaneously measuring multiple channels or in environments where noise is likely to occur, it is able to accurately analyze the cause of equipment failures. This reduces the number of cases of imprecise maintenance, which in turn reduces the man-hours required for maintenance work.
Also, when using VZ20X in production quality evaluation, safe and reliable testing can be performed because it is less susceptible to the characteristics of products and components and the testing environment.
High-Speed and Highly Accurate Sensing Detects Signs of Failures Before They Occur
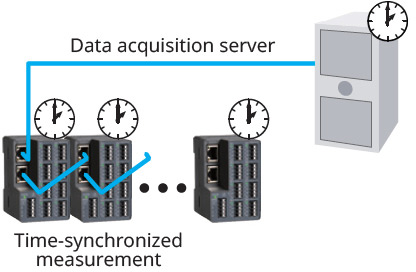
A single VZ20X unit can measure 8 channels of analog inputs at high speed with a sampling cycle of 1 ms. It supports simultaneous measurement by up to 15 units across 120 channels, helping to enable predictive maintenance at manufacturing sites where large amounts of equipment and many sensors are in operation. It is also capable of extremely precise measurement with synchronization accuracy of ±100 µs, measurement accuracy of ±0.05%, temperature measurements accurate to within ±0.16°C, and voltage measurements accurate to ±1mV. In this way, high-speed and highly accurate measurements that do not miss even the slightest changes in the equipment enable the prediction of failures.
Monitors Equipment Status With Support for All Kinds of Analog Sensors
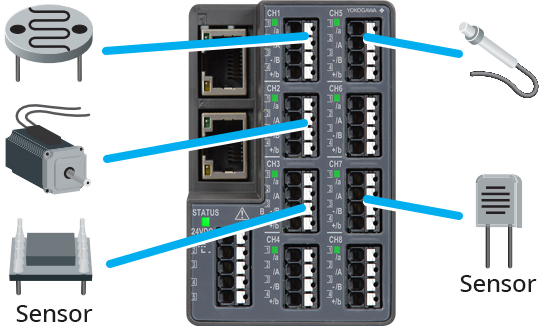
DC voltage, 4-wire resistor, thermocouple (TC), and 3-wire/4-wire RTD can be measured with a single unit. The use of analog sensors that support these inputs allow a variety of data to be measured, eliminating the need to use numerous data measurement devices for different kinds of sensors.
Accurate Sensing Even Without a Power Outlet
Using the USB Type Detection Disable feature, the VZ20X can be powered by sources other than USB Type-C. Powering the device from a PC’s USB Type-A port eliminates the need for an external 24V DC power supply or power cable, reducing installation and wiring costs. Moreover, by connecting the VZ20X to a commercially available PoE (Power over Ethernet) splitter, it is possible to supply power using an Ethernet cable.
Examples of VZ20X Applications
VZ20X can be used in CBM (condition-based maintenance) at manufacturing and logistics sites.
Manufacturing Plants: Predictive Maintenance of Manufacturing and Logistics Equipment
Recently, manufacturing plants have been making use of automatic guided vehicles and other advanced automation systems to reduce the number of workers on production lines. However, there are still many pieces of analog equipment for which it is difficult to successfully detect signs of deterioration, leading to issues of reduced operating rates due to sudden failures.
The VZ20X is extremely small and lightweight, about the size of a business card, and can be retrofitted to existing analog equipment. Furthermore, when combined with Yokogawa Electric’s data logging software (GA10), real-time OS controller (e-RT3 Plus), and its proprietary AI, highly accurate data collection, monitoring, anomaly detection, and causal analysis can be achieved. Properly timed maintenance reduces the number of man-hours required to troubleshoot problems associated with equipment stoppages, contributing to improved uptime and labor savings.
ข้อมูลจำเพาะ
Main Body: Analog Sensing Unit: VZ20X-1N1NDD
สิ่งของ | ข้อมูลจำเพาะ |
---|---|
จำนวนอินพุต | 8 ช่อง |
ประเภทอินพุต | DC voltage, 4-wire resistor, thermocouple, and 3-wire/4-wire RTD |
ช่วงการรับข้อมูล | 1 ms (เร็วที่สุด), การวัดพร้อมกัน 8 ช่อง |
วัด. ซิงค์ ความแม่นยำ | ภายใน ±100 μs (ระหว่างช่องสัญญาณเข้า ระหว่างหน่วย) |
ความแม่นยำในการวัด | 0.025% ของ FS (พร้อมแรงดัน DC และตัวกรองสัญญาณรบกวนความถี่ของแหล่งจ่ายไฟที่เปิดใช้งาน) |
ทนต่อแรงดันไฟฟ้า | 3,000 VAC (50 Hz/60 Hz) 1 นาที (ระหว่างช่องสัญญาณอินพุตแบบแอนะล็อก, วงจรอินพุตแบบแอนะล็อกไปยังวงจรภายใน) |
แหล่งจ่ายไฟ | 24 VDC or USB |
อุณหภูมิ/ความชื้นในการทำงาน | -10–55°C (ติดตั้งบนราง DIN), -10–50°C (บนการติดตั้งเดสก์ท็อป) /5–90% RH |
เดินสายไฟ | ขั้วต่อแบบกดเข้า, ขั้วต่อปลอกโลหะ |
ขนาด | สูง (ส) 78 x กว้าง (ก) 50 x ลึก (ล) 65 mm |
การสื่อสารอีเธอร์เน็ต | 2 พอร์ต, โปรโตคอล: Modbus/TCP, โปรโตคอลเฉพาะ GA10 |
การติดตั้ง | ติดตั้งบนราง DIN บนเดสก์ท็อป |
มาตรฐาน | ![]() |
VZ Configurator
สิ่งของ | คำอธิบาย |
---|---|
การตั้งค่าพารามิเตอร์ | ช่วง/สเกลอินพุต, เงื่อนไขการสื่อสารอีเทอร์เน็ต |
ฟังก์ชั่นการตรวจสอบ | การตรวจสอบตามเวลาจริง การวินิจฉัยตนเอง |
ซ่อมบำรุง | อัพเดตเฟิร์มแวร์ การปรับอินพุต |
แหล่งข้อมูล
ลูกค้าต้องการปรับปรุงการบำรุงรักษาโดยคาดการณ์ความล้มเหลวของอุปกรณ์ที่ทนทานที่มีอยู่ อย่างไรก็ตาม อุปกรณ์ที่มีอยู่ไม่มีพื้นที่เพียงพอ และไม่ง่ายที่จะเพิ่มจำนวนเซ็นเซอร์ที่จำเป็นในการทำความเข้าใจสภาพ
เพื่อแก้ไขปัญหานี้ ขนาดกะทัดรัดของ VZ20X ช่วยให้สามารถติดตั้งระหว่างอุปกรณ์ต่างๆ และสามารถตรวจสอบการรวบรวมข้อมูลผ่านอีเทอร์เน็ต (Modbus/TCP) ได้อย่างง่ายดาย
VZ20X
การหยุดการผลิตที่เกิดจากการทำงานผิดพลาดอย่างกะทันหันในอุปกรณ์การผลิตถือเป็นการสูญเสียโอกาสอย่างร้ายแรง
การตรวจสอบอุปกรณ์เพื่อป้องกันความล้มเหลวมักดำเนินการตามประสบการณ์และความรู้สึกของเจ้าหน้าที่ซ่อมบำรุง และเต็มไปด้วยความเสี่ยง
ลูกค้าต้องการบำรุงรักษาอย่างเหมาะสมตามเวลาของการหยุดทำงานตามปกติและสภาพของอุปกรณ์ ไม่ใช่หลักเกณฑ์ทั่วไปสำหรับเจ้าหน้าที่บำรุงรักษา
เพื่อให้เป็นไปตามความคาดหวังเหล่านี้ VZ20X จึงสามารถติดตั้งได้อย่างกะทัดรัดในช่องว่างของอุปกรณ์การผลิตที่มีอยู่ และด้วยการตรวจจับการเปลี่ยนแปลงสถานะของอุปกรณ์แต่ละอย่างอย่างแม่นยำ จึงช่วยลดความเสี่ยงของอุปกรณ์ดังกล่าวได้
เมื่องานบำรุงรักษาอุปกรณ์การผลิตหรือเกิดปัญหาขึ้น ลูกค้าต้องการตรวจสอบสถานการณ์ที่หน้างานทันที
พวกเขายังต้องการเตรียมตัวอย่างง่ายดายสำหรับสิ่งนั้น (สร้างระบบการวัด)
เพื่อตอบสนองต่อความต้องการเหล่านี้ VZ20X และ GA10 ทำให้การสร้างระบบรวบรวมข้อมูล (ระบบยืนยันในสถานที่ทำงาน) เป็นเรื่องง่าย และตรวจสอบสถานะของอุปกรณ์การผลิตได้อย่างรวดเร็ว
ลูกค้าสามารถครอบคลุมพื้นที่ระยะไกลได้ และ VZ20X มีขนาดกะทัดรัดมากสำหรับติดตั้งในพื้นที่ขนาดเล็กของอุปกรณ์ใดๆ
เนื่องจากการแก้ไขและเพิ่มเติมกฎระเบียบ ปั๊มที่ใช้ในน้ำ ระบบระบายน้ำทิ้ง และระบบระบายน้ำจำเป็นต้องมีการปรับเปลี่ยนที่ยืดหยุ่นและจุดการวัดเพิ่มเติมในการตรวจสอบประสิทธิภาพ
เพื่อตอบสนองต่อการเปลี่ยนแปลงในสภาพแวดล้อมและสถานการณ์ ขนาดกะทัดรัดของ Multi-Sensing Remote I/O Analog Sensing Unit VZ20X ช่วยลดภาระในการขยายและสร้างการผลิตใหม่และอุปกรณ์ทดสอบเพื่อให้เหมาะกับสภาพแวดล้อมการติดตั้งในปัจจุบัน
ลูกค้าต้องการปรับปรุงการบำรุงรักษาโดยคาดการณ์ความล้มเหลวของอุปกรณ์ที่ทนทานที่มีอยู่ อย่างไรก็ตาม อุปกรณ์ที่มีอยู่ไม่มีพื้นที่เพียงพอ และไม่ง่ายที่จะเพิ่มจำนวนเซ็นเซอร์ที่จำเป็นในการทำความเข้าใจสภาพ
เพื่อแก้ไขปัญหานี้ ขนาดกะทัดรัดของ VZ20X ช่วยให้สามารถติดตั้งระหว่างอุปกรณ์ต่างๆ และสามารถตรวจสอบการรวบรวมข้อมูลผ่านอีเทอร์เน็ต (Modbus/TCP) ได้อย่างง่ายดาย
เนื่องจากการทดสอบการประเมินประสิทธิภาพของมอเตอร์ไดรฟ์อินเวอร์เตอร์นั้นไวต่อเสียงรบกวน จึงจำเป็นต้องใช้อุปกรณ์ที่มีความต้านทานเสียงรบกวนสูง นอกจากนี้ หากจำนวนจุดการวัดมีมาก เครื่องมือวัดแบบหลายช่องที่ตอบสนองการวัดจะมีราคาสูง
VZ20X ป้องกันเสียงรบกวนและปลอดภัยสำหรับการรวบรวมข้อมูลที่แม่นยำ แม้ในเป้าหมายการวัดที่มีแนวโน้มเกิดเสียงรบกวน เช่น อินเวอร์เตอร์
ยากที่จะกลับไปกลับมาระหว่างพื้นสำนักงานกับพื้นทดสอบเพื่อตรวจสอบสถานะความทนทานของตลับลูกปืน
เวลาเดินทางไปกลับนั้นสิ้นเปลืองและเป็นภาระหนักต่อชั่วโมงการทำงาน หากคุณมีพื้นที่ทดสอบมากกว่า 1 แห่ง ก็ยิ่งเป็นภาระมากขึ้นไปอีก
VZ20X และ GA10 ทำให้สามารถสร้างระบบตรวจสอบอย่างง่ายได้ ระบบยังช่วยให้สามารถตรวจสอบสถานที่ผลิตและทดสอบได้จากระยะไกล ซึ่งช่วยลดภาระในไซต์งานได้
ขณะนี้ ข้อมูลของอุปกรณ์การผลิตหลายรายการในโรงงานผลิตเซมิคอนดักเตอร์กำลังถูกตรวจสอบโดยเจ้าหน้าที่ภาคสนาม และการตรวจสอบอยู่ในสถานการณ์ที่ยากลำบาก ดังนั้นจึงมีความต้องการเพิ่มขึ้นสำหรับการตรวจสอบจากส่วนกลางภายในโรงงาน
VZ20X ช่วยให้การติดตั้งสามารถใช้ประโยชน์จากพื้นที่ที่มีอยู่
นอกจากนี้ GA10 ยังมีส่วนช่วยในการประหยัดแรงงานในภาคสนามด้วยการตรวจสอบจากระยะไกล
เมื่องานบำรุงรักษาอุปกรณ์การผลิตหรือเกิดปัญหาขึ้น ลูกค้าต้องการตรวจสอบสถานการณ์ที่หน้างานทันที
พวกเขายังต้องการเตรียมตัวอย่างง่ายดายสำหรับสิ่งนั้น (สร้างระบบการวัด)
เพื่อตอบสนองต่อความต้องการเหล่านี้ VZ20X และ GA10 ทำให้การสร้างระบบรวบรวมข้อมูล (ระบบยืนยันในสถานที่ทำงาน) เป็นเรื่องง่าย และตรวจสอบสถานะของอุปกรณ์การผลิตได้อย่างรวดเร็ว
ในกระบวนการพ่นสีของชิ้นส่วนรถยนต์ ความล้มเหลวหรือการกัดกร่อนของอิเล็กโทรดสามารถนำไปสู่การเสื่อมคุณภาพได้
นอกจากนี้ การขาดการตรวจสอบสภาพอิเล็กโทรดในปัจจุบันยังส่งผลให้มีการเปลี่ยนอิเล็กโทรดในช่วงเวลาสั้นๆ ซึ่งเป็นปัญหาที่มีค่าใช้จ่ายสูงมาก
เพื่อแก้ไขปัญหาเหล่านี้ เราตรวจสอบความเสื่อมโทรมของโรงงานผลิตและมีส่วนร่วมในการดำเนินการบำรุงรักษาที่ปรับให้เหมาะกับสภาพของอุปกรณ์
ลูกค้าต้องการตรวจสอบปริมาณการใช้ไฟฟ้าของอุปกรณ์การผลิตแต่ละชิ้นเพื่อประหยัดพลังงานในโรงงาน แต่การติดตั้งระบบตรวจวัดในอุปกรณ์ที่มีอยู่นั้นไม่ใช่เรื่องง่าย แม้กระทั่งจากเงื่อนไขการติดตั้งและสายไฟ
ขนาดกะทัดรัดของ VZ20X ช่วยให้สามารถติดตั้งได้ตามเงื่อนไขที่เป็นอยู่ การตรวจจับที่แม่นยำยังช่วยในการสร้างภาพการใช้พลังงานที่อุปกรณ์การผลิต
ลูกค้าต้องการปรับปรุงการบำรุงรักษาโดยคาดการณ์ความล้มเหลวของอุปกรณ์ที่ทนทานที่มีอยู่ อย่างไรก็ตาม อุปกรณ์ที่มีอยู่ไม่มีพื้นที่เพียงพอ และไม่ง่ายที่จะเพิ่มจำนวนเซ็นเซอร์ที่จำเป็นในการทำความเข้าใจสภาพ
เพื่อแก้ไขปัญหานี้ ขนาดกะทัดรัดของ VZ20X ช่วยให้สามารถติดตั้งระหว่างอุปกรณ์ต่างๆ และสามารถตรวจสอบการรวบรวมข้อมูลผ่านอีเทอร์เน็ต (Modbus/TCP) ได้อย่างง่ายดาย
PLC ในเครื่องฉีดพลาสติกที่มีอยู่ไม่มีฟังก์ชันการบันทึก แต่คุณต้องการเพิ่มฟังก์ชันเพื่อบันทึกข้อมูลการผลิตและข้อมูลสภาพอุปกรณ์ ลูกค้ายังต้องการทราบฟังก์ชันเหล่านี้อย่างง่ายดาย
เพื่อตอบสนองต่อข้อกำหนดเหล่านี้ VZ20X ทำการรวบรวมข้อมูลของ PLC และเซ็นเซอร์อะนาล็อก และ GA10 ให้การตรวจสอบและการบันทึกนอกสถานที่เพื่อสนับสนุนการทำงานที่ปลอดภัยยิ่งขึ้น
ในช่วงไม่กี่ปีที่ผ่านมา ลูกค้าของอุปกรณ์แปรรูปที่ใช้ในการผลิตอาหารและยาได้ร้องขอการแสดงภาพเงื่อนไขของอุปกรณ์มากขึ้น
เนื่องจากเราไม่ทราบสถานะปัจจุบันของโรงงานผลิตของเรา และการบำรุงรักษาขึ้นอยู่กับประสบการณ์และสัญชาตญาณของแต่ละบุคคล
ด้วยการรวบรวมข้อมูลอย่างแม่นยำด้วย VZ20X และการแสดงภาพสถานะของอุปกรณ์ ทำให้สามารถเข้าใจสถานะปัจจุบันและดำเนินการบำรุงรักษาที่เหมาะสมตามสภาพของอุปกรณ์ได้
ลูกค้าต้องการปรับปรุงการบำรุงรักษาโดยคาดการณ์ความล้มเหลวของอุปกรณ์ที่ทนทานที่มีอยู่ อย่างไรก็ตาม อุปกรณ์ที่มีอยู่ไม่มีพื้นที่เพียงพอ และไม่ง่ายที่จะเพิ่มจำนวนเซ็นเซอร์ที่จำเป็นในการทำความเข้าใจสภาพ
เพื่อแก้ไขปัญหานี้ ขนาดกะทัดรัดของ VZ20X ช่วยให้สามารถติดตั้งระหว่างอุปกรณ์ต่างๆ และสามารถตรวจสอบการรวบรวมข้อมูลผ่านอีเทอร์เน็ต (Modbus/TCP) ได้อย่างง่ายดาย
ลูกค้าต้องการปรับปรุงการบำรุงรักษาโดยคาดการณ์ความล้มเหลวของอุปกรณ์ที่ทนทานที่มีอยู่ อย่างไรก็ตาม อุปกรณ์ที่มีอยู่ไม่มีพื้นที่เพียงพอ และไม่ง่ายที่จะเพิ่มจำนวนเซ็นเซอร์ที่จำเป็นในการทำความเข้าใจสภาพ
เพื่อแก้ไขปัญหานี้ ขนาดกะทัดรัดของ VZ20X ช่วยให้สามารถติดตั้งระหว่างอุปกรณ์ต่างๆ และสามารถตรวจสอบการรวบรวมข้อมูลผ่านอีเทอร์เน็ต (Modbus/TCP) ได้อย่างง่ายดาย
VZ20X ติดตั้งใกล้กับเซ็นเซอร์ เช่น อุณหภูมิ ความชื้น และการสั่นสะเทือน และเปิดใช้งานการรวบรวมข้อมูลโดยอัตโนมัติผ่าน LAN ของโรงงาน การรวบรวม การตรวจสอบ และการจัดการข้อมูลสามารถตรวจสอบได้โดยอัตโนมัติและสม่ำเสมอด้วยซอฟต์แวร์บันทึกข้อมูล GA10 เป็นผลให้ช่วยลดภาระงานของคนงาน
ดาวน์โหลด
โบรชัวร์
- VZ20X Analog Sensing Unit (5.1 MB)
คู่มือการใช้งาน
ข้อกำหนดทั่วไป
- Model VZ20X Analog Sensing Unit (918 KB)
ซอฟต์แวร์
ข้อมูลทางเทคนิค
แบบแปลน
- Model VZ20X Analog Sensing Unit (271 KB)
ข่าวสาร
-
Press Release | Solutions & Products Aug 31, 2021 โยโกกาวา เปิด OpreX Multi-Sensing Remote I/O VZ20X Analog Sensing Unit
- การออกแบบที่กะทัดรัดระดับโลกและประสิทธิภาพสูงสำหรับการบำรุงรักษาการผลิตและการพัฒนาแบตเตอรี่ EV และส่วนประกอบอื่นๆ -
คุณต้องการข้อมูลเพิ่มเติมเกี่ยวกับบุคลากร เทคโนโลยี และโซลูชั่นของเราหรือไม่ ?
ติดต่อเรา