Low-power, wide-area industrial temperature and pressure sensors enhance monitoring capabilities, leading to clearer understanding of maintenance needs and improved decision making.
Walking through most process plants or remote facilities, an observer will encounter a sizeable collection of temperature and pressure instruments. Without knowledge of the two critical parameters of temperature and pressure, it is often impossible to properly monitor a process and maintain equipment.
Temperature is primarily measured by one of two methods in a plant environment, by either a thermocouple or a resistance temperature detector. Pressure can be measured by a variety of methods, but each involves measuring the force a product process exerts on one side of a medium relative to the force on the other side. The medium can be a fluid or a diaphragm, and the force opposing the product process force may be a spring, a fluid, the atmosphere itself, or another product process force. A pressure sensor resolves the forces at play into a pressure value.
Inconvenient wired practices
Traditionally, transmitting a temperature or pressure measurement to a central plant control location required a wired line from an instrument to a host, such as a basic process control system, an asset management system, or a process historian. While this method works well in some parts of existing plants, wired instrumentation is not always practical or possible.
It can be difficult to run conduit, power, and communication lines to distant locations, and the cost may be prohibitive for one or two instruments. Furthermore, wired solutions place constraints on instruments’ physical locations, restricting flexibility if monitoring requirements change.
Some applications do not require continuous monitoring at a host system but may require manual readings of gauges to be performed and recorded on a regular schedule to keep a general watch on equipment health. In these situations, equipment may be located in confined spaces or hazardous environments that may pose safety risks to plant personnel when gathering data.
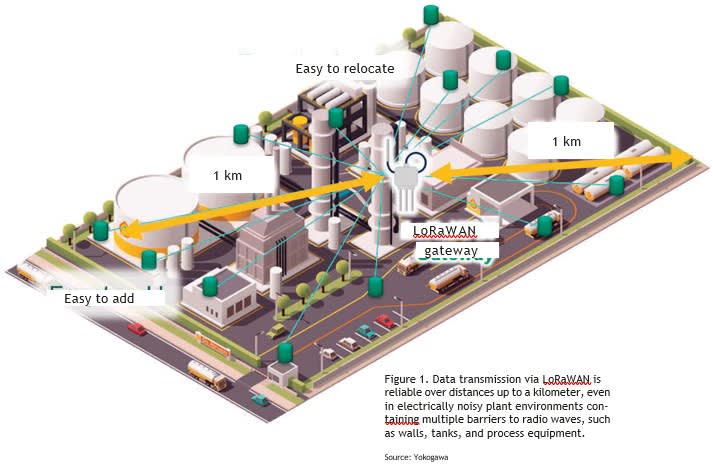
Modern wireless solutions
Spurred by a globally increasing desire to boost productivity and improve the efficiency of equipment maintenance in plants, there is a need to detect and analyze abnormalities and identify degrading equipment. In hard-to-reach locations—such as distant sites, confined spaces, or dangerous environments—there are advantages to be gained by introducing sensors that utilize modern wireless technologies.
The two wireless instrumentation technologies most often used in process manufacturing are in-plant networks, such as ISA100, and long-range wireless networks. In-plant networks are more capable but require more effort and resources to set up than their long-range counterparts. This article will focus on long-range wireless networks and show their advantages in certain applications. Low-power, wide-area (LPWA) industrial sensors for Industrial Internet of Things (IIoT) applications address the obstacles faced when making measurements in hard-to-reach or distant locations. They are compact, lightweight, battery powered, and durable. They can transmit data wirelessly to a long-range, wide-area network (LoRaWAN) gateway. Data transmission via LoRaWAN is reliable over distances up to a kilometer, even in electrically noisy plant environments containing multiple barriers to radio waves, such as walls, tanks, and process equipment (figure 1).
A host system, whether on premises or in the cloud, can continuously monitor data formerly read on gauges and limited by operator rounds.
Sensor anatomy
LPWA industrial sensors comprise a module for temperature or pressure measurement coupled with a wireless communication module. When the modules are connected, program and parameter settings stored on the measuring module are copied to the wireless communication module for transmission (figure 2).
By storing configuration parameters on the measurement module, wireless communication modules may be easily swapped without disrupting the product process. The dual-module setup also allows personnel to replace batteries without taking the product process offline. During battery replacement, the wireless communication module—containing the battery that powers both modules—is decoupled from the measuring module. Once battery replacement is complete and the modules are reconnected, the measurement module transfers its program and parameter settings to the wireless communication module.
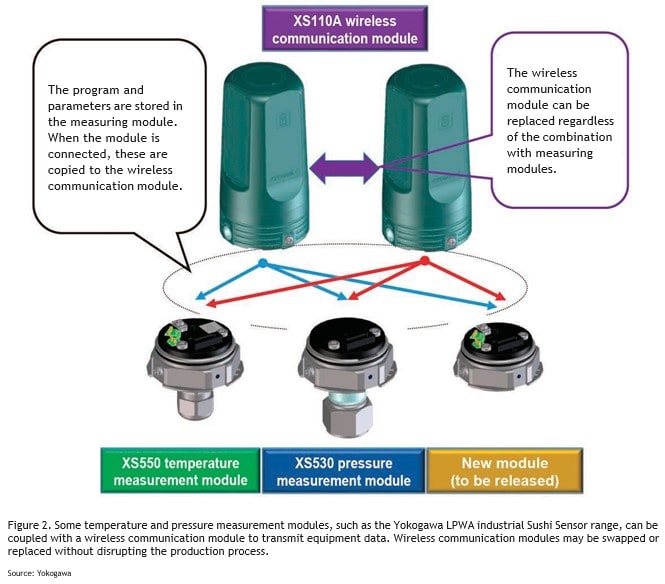
The wireless communication module handles data transmission to the LoRaWAN gateway and incorporates a near-field communication radio for sensor configuration from a compatible mobile device, such as a smartphone. When coupled, the communication and measurement modules are encased in an IP67/NEMA 4X–rated waterproof, dustproof, and explosion-proof housing for use in harsh environments.
LPWA industrial temperature sensors accept input from a thermocouple, making them compatible with instrumentation found at most plants. They convert the voltage input to a temperature value using reference junction compensation and built-in conversion tables, and then send this value to the LoRaWAN gateway. An LPWA industrial pressure sensor uses a piezoresistive diaphragm for lower power consumption and noise reduction compared with other diaphragm types. The diaphragm’s degree of deflection varies the electrical resistance within the sensor, which is converted to a pressure value based on factory configuration. As with its temperature sensor counterpart, the LPWA industrial pressure sensor transmits its pressure value to the LoRaWAN gateway at a user-defined update time.
Data is normally collected and transmitted by LPWA industrial sensors at a period ranging from every minute to once every three days. An LPWA industrial sensor containing a single D-size battery may last up to 10 years without battery replacement when transmitting one equipment data point per hour, depending on ambient temperature.
Application cases
When multistage heat exchangers are used in a plant, the first stage input and last stage output temperatures are usually monitored online. By installing LPWA industrial temperature sensors in the tight spaces between stages, it is possible to increase data capture and better understand equipment conditions in the heat exchanger. This enables anomaly detection at every stage, knowledge that can improve operational and maintenance efficiency.
In another scenario, leaks or clogging can degrade dust collectors and their piping, decreasing operational efficiency. Pressure gauges are usually mounted to detect such abnormalities over wide areas within plants, with visual observations made during operator rounds. Replacing these pressure gauges with LPWA industrial pressure sensors increases the frequency, ease, and reliability of measurement. Additionally, the data is optimized for immediate use by a plant historian or other software system, without requiring human effort to input or translate individual data points.
Benefits gained
By capitalizing on wireless technological advances in temperature and pressure sensors, plant owners can move beyond the obstacles inherent with wired sensor architectures. Increased freedom to deploy sensors that reliably transmit data for seamless integration into host systems leads to clearer understanding of equipment maintenance needs. It is this understanding—as well as the ability to detect abnormalities—that enables plant owners to remain a step ahead in regard to equipment maintenance, while continuously refining and improving product process efficiency.
* Sushi Sensor is a registered trademark or trademark of Yokogawa Electric Corporation.
* LoRa is a registered trademark, and LoRaWAN is a trademark of Semtech Corporation.
* All other company, organization, product names, and logos that appear in this article are either trademarks or registered trademarks of their respective holders.
ABOUT THE AUTHOR
Takayuki Sugizaki is an IoT wireless promotion manager at Yokogawa Electric Corporation. He works in the Technical Consulting Section of the CX Strategy Department, specializing in industrial automation products and services. Sugizaki has been with Yokogawa for 18 years and has 35 years of experience in the electronics industry. He has a BS in electronic engineering from Shinshu University.
Related Products & Solutions
-
Sushi Sensor
Optimize processes with a range of wireless measurement and diagnostic solutions.
Have Questions?
Contact a Yokogawa Expert to learn how we can help you solve your challenges.