Rotamass Total Insight (TI), Yokogawa’s Coriolis mass flowmeter, provides very high accuracy for measuring liquids and gases while adopting the Total Insight concept and totally supporting the product lifecycle.
From the direct mass flow, density, temperature measurements, with Rotamass TI you can calculate:
- Volume flow at operating or reference conditions
- Density at reference conditions
- Concentration measurements of mixable or unmixable fluids
With additional measurement input Rotamass TI can calculate fluid viscosity for Newtonian liquids or energy-heating value for gas measurement.
Rotamass TI offer various state of-the-art interfaces including latest technology Ethernet-APL (Advanced Physical Layer) facilitating data-based total insight into your process.
Click here for more details about Ethernet-APL technology.
About OpreX
OpreX is the comprehensive brand for Yokogawa’s industrial automation (IA) and control business and stands for excellence in the related technology and solutions. It consists of categories and families under each category. This product belongs to the OpreX Field Instruments family that is aligned under the OpreX Measurement category.
Details
Total Insight
In the last decade, the use of Coriolis Mass Flow and Density Meters has been changing from general purpose to supporting your needs in specific applications.
While the technological complexity increased, the demand for simple operation and handling is also a rising requirement.
Yokogawa answers these needs by offering six dedicated product lines with two specialized transmitters allowing the highest flexibility -the Rotamass Total Insight
Typical Application Example
The product is ideal for industrial processes such as petrochemicals, chemicals, food and beverages.
Wetted material with excellent wear resistance, corrosion resistance, and permeation resistance is available to provide high precision and stable flow measurement even at high pressure & high temperature.
Specification & Function
Refer to the General Specification sheet located under the 'Downloads' tab for detailed specifications.
Product Line | Rotamass Nano |
Rotamass Prime |
Rotamass Hygienic |
Rotamass Supreme |
Rotamass Intense |
Rotamass Giga |
|||
---|---|---|---|---|---|---|---|---|---|
![]() |
![]() |
![]() |
![]() |
![]() |
![]() |
||||
Flow Range | ![]() |
||||||||
Liquid process fluids
|
|||||||||
Liquids in general | ● | ● | ● | ● | ● | ● | |||
Aggressive liquids | ○ | - | - | ● | ● | ○ | |||
High viscous fluids | ○ | ● | ● | ○ | ○ | ○ | |||
Gaseous process fluids
|
|||||||||
Gases in general | ○ | ● | ○ | ○ | ○ | ● | |||
Low density gases | ○ | ● | ● | ○ | ○ | ○ | |||
Mixed process fluids
|
|||||||||
Unmixable or mixable liquids | ● | ● | ● | ● | ● | ● | |||
Liquids with entrained gas | ● | ● | ● | ● | ● | ○ | |||
Process conditions
|
|||||||||
Process temperature | -50 to +260 °C -58 to +500 °F |
-70 to +200 °C -94 to +392 °F |
-70 to +140 °C -94 to +284 °F |
-196 to +350 °C -321 to +662 °F |
-70 to +150 °C -94 to +302 °F |
-70 to +350 C or +200 C (Giga 2F) -94 to +662 F or +392 F (Giga 2F) |
|||
Process pressure up to | 285 bar or 460 bar *1 4183 psi or 6672 psi *1 |
100 bar 1450 psi |
40 bar 580 psi |
100 bar or 250 bar *1 1450 psi or 3626 psi *1 |
up to 700 bar 10000 psi |
100 bar or 180 bar *1 1450 psi or 2610 psi *1 |
|||
Line sizes | DN15 to DN40 1/4 in. to 1 1/2 in. |
DN15 to DN125 3/8 in. to 5 in. |
DN25 to DN80 1 in. to 3 in. |
DN15 to DN125 3/8 in. to 5 in. |
9/16 or 3/4“in. AutoClave 1/4 in. to 2 in. |
DN100 to DN250 4 in. to 10 in. |
|||
Accuracy
|
|||||||||
Mass flow for liquids up to | ± 0.1 % | ± 0.1 % | ± 0.1 % | ± 0.1 % | ± 0.1 % | ± 0.1 % | |||
Mass flow for gas up to | ± 0.50 % | ± 0.35 % | ± 0.35 % | ± 0.35 % | ± 0.50 % | ± 0.35 % | |||
Density for liquids up to | ± 0.5 g/l | ± 0.5 g/l | ± 0.5 g/l | ± 0.5 g/l | ± 0.5 g/l | ± 2.0 g/l | |||
Turndown flat accuracy | ○ | ● | ● | ○ | ○ | - | |||
Materials and process connections
|
|||||||||
Material of wetted parts | Alloy C-22/2.4602 & 316L/1.4404 | 316L/1.4404 | 316L/1.4404 | 316L/1.4404 or alloy C-22/2.4602 or 304/1.4301 *1 | 316L/1.4404 or alloy C-22/2.4602 or 304/1.4301*1 | 316L/1.4404 or alloy C-22/2.4602 (Giga 1F only) | |||
Flange process connections | EN, ASME, JPI, JIS | EN, ASME, JPI, JIS | − | EN, ASME, JPI, JIS | ASME | EN, ASME, JIS | |||
Threaded process connections | G, NPT | G, NPT | DIN11851, SMS1145 | G, NPT | G, NPT | − | |||
Clamp process connections | DIN32676 | − | DIN32676, JIS/ISO2852 | DIN32676, JIS/ISO2852 | − | − | |||
Sensor design
|
|||||||||
Insulation and heat tracing options | ● | - | - | ● | - | ● | |||
Rupture disk | ○ *1 | - | - | ● | ● | ● | |||
Customer & NAMUR face-to-face length | ● | ● | - | ● | - | ○ | |||
Approvals / Certificates
|
|||||||||
3-A, EHEDG, EC1935:04 and EC2023:06 | - | - | ● | ● | - | - | |||
Marine application | ● | ● | ● | ● | ● | ○ | |||
Functional Safety | SIL 2 (SIL3) | ||||||||
Custody transfer application | NTEP (Nano 20) | NTEP | NTEP | NTEP, INMETRO | NTEP | NTEP, INMETRO | |||
Hazardous area approvals | IECEx, ATEX, UKEx, FM (USA/Canada), NEPSI, INMETRO, PESO, EAC Ex, Taiwan Safety Label, Korea Ex, Japan Ex, ECAS Ex, Ukraine Ex |
ROTAMASS Nano
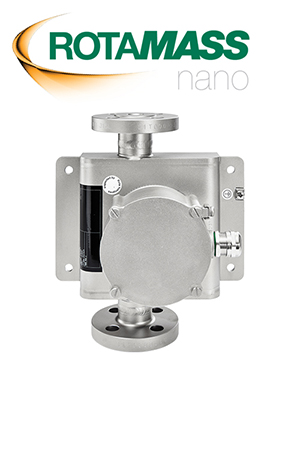
When Every Drop Counts
The world's smallest dual bent tube Coriolis Mass Flow and Density Meters series for highly accurate measurement at lowest flows.
The dual tube design compensates for fluctuations of density, temperature, pressure and environment conditions. This provides a consistent repeatable and accurate measurement especially for small size Coriolis Mass Flow and Density Meters.
- Typical Applications
- Batching
- Dosing
- Blending
- Chemical injection
- Dosing systems
- High-pressure gases
- Liquid and gas low flow measurement
- Precision coatings
- Metering pump control
- Metrology
- R&D laboratory
- Vacuum thin film coating
ROTAMASS Prime
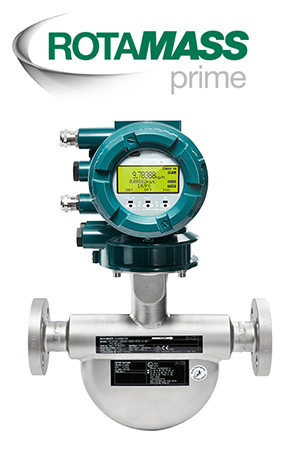
Versatile in Applications
The versatile Coriolis Mass Flow and Density Meters with superior turndown and lowest pressure drop in the market. Ideal for a broad range of standard applications, this series is a flexible and cost effective solution for highly accurate flow and density measurements. Features such as concentration measurement or the Tube Health Check function allow the meter to be adjusted to customer needs.
- Typical Applications
- Batching
- Blending
- Chemical recovery
- Continuous reaction
- In-line concentration and density measurement
- Catalyst feed
- Filling and dosing
- Mass balance
- Net oil computing
- Palm oil
- Process control
ROTAMASS Hygienic
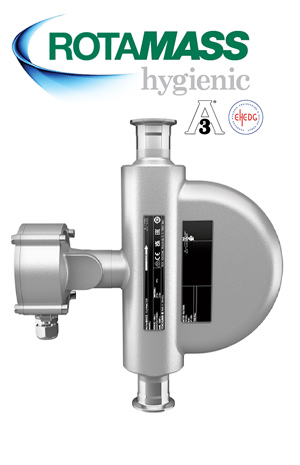
With Pure Dedication
Specifically designed and certified for food & beverage, biotechnology and pharmaceutical utility applications. (EHEDG certified, 3-A certified)
This series is the appropriate answer to the daily constraints of hygienic processes ensuring continuous product quality and minimizing losses. This is made easy by the provided multi-variable measurement and various dedicated features.
- Typical Applications
- Bioreactor feeds
- Bottling
- Carbonation of beverages
- Deionized water
- Fermentation
- Juice processing
- Molasses measurement
- Online sugar concentration
- Raw milk tanker unloading
- Process water reclamation
- Product quality control
- Sugar industry
ROTAMASS Supreme
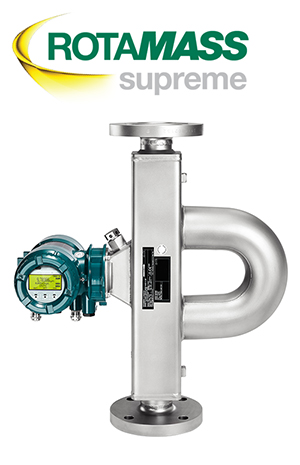
Experience Meets Innovation
The Coriolis Mass Flow and Density Meters with superior performance under demanding conditions.
The successful Rotamass series has been progressively developed and is also newly equipped with the latest technology. This meter delivers unsurpassed performance for demanding and critical applications with superior aeration handling and advanced diagnostic functionality.
- Typical Applications
- Batching
- Burner control
- Feed and product control
- Filling and dosing
- Gas void fraction
- In-line concentration and density
- Loss control
- Material and mass balance
- Net oil computing
- Process control
- Solvents
- Water cut
ROTAMASS Intense
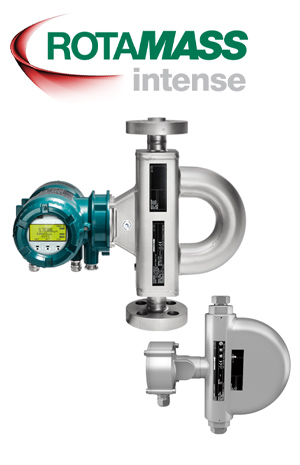
Safe Under High Pressure
The Coriolis Mass Flow and Density Meters with the most robust and durable design for precise measurement in high pressure applications.
Safety is always a concern and especially when operating at high pressures. Therefore, this series has been designed to meet the highest safety requirements. Combined with advanced diagnosis such as the Total Health Check function, operation is always under secure control.
- Typical Applications
- Chemical injection
- Compressed gases
- Fuels
- Glycol TEG/MEG
- High-pressure gases
- Hydraulic oil
- Hydrocarbons
- Liquified gases
- Natural gas hydration
- Offshore and onshore
- Oil refinery processes
- Solvents
ROTAMASS Giga
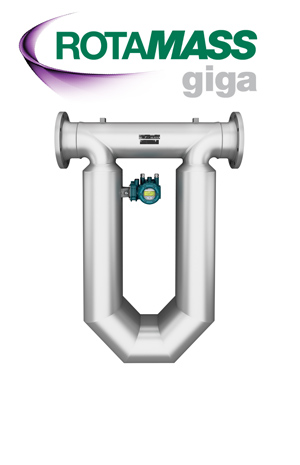
Big in Performance
Delivering best in class accuracy and most flexible installation at high flow rates.
The unmatched accuracy at the low end of the measuring range offers maximum flexibility from engineering to final operation. This series unifies a long service life with low maintenance costs and reliable performance.
- Typical Applications
- Bitumen
- Distribution networks
- Drilling mud
- LNG
- Rail car loading
- Ship loading
- Truck loading
- Tar
- Offshore and onshore
- Oil well cementing and hydrofracturing
ROTAMASS Transmitters
Essential and Ultimate Transmitters
Future Ready. The Rotamass TI product family has a common and unified transmitter platform with two options that provide the highest flexibility and a tailor-made solution. The Essential transmitter is the cost effective solution for general purpose applications, and the Ultimate transmitter provides various additional features for best-in-class measurement.
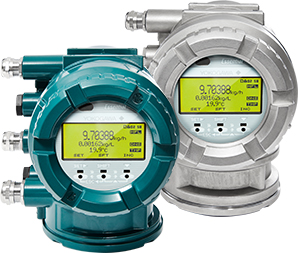
Essential Transmitter
- Multi-lingual wizard for easy setup
- Event Management according NAMUR NE107
- microSD card for easy data transfer and spare management
- Wide range of I/O combinations
- Universal power supply
- Tube Health Check for in-line meter verification
- HART or Modbus communication
- Ultra low copper aluminium or stainless steel transmitter housing
- NAMUR NE95 compliant
- Compliance with AGA11
Ultimate Transmitter
Beyond that the Ultimate transmitter provides:
- In-line concentration measurement
- Net Oil Computing acc. API
- Dynamic Pressure Compensation
- Batching function
- Viscosity function
- Profibus PA , Foundation Fieldbus or PROFINET over APL communication
- Features on Demand for function upgrade
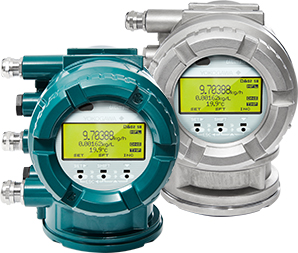
Total Insight - Simplified Selection -
Engineering & Procurement
Have you ever struggled to select the most suitable product/specification for the process being measured?
- Product Selection
Get convenient support by our online tools Product Finder and FlowConfigurator.
Simply select the most suitable products and specifications for your purpose and process conditions.Find the right flowmeter for your application, size and configure it!
The FlowConfigurator allows you to generate your data sheet and save your sizing projects for easy reuse.
Total Insight - Smart Assist -
Installation & Commissioning
Have you ever been struggling to set up the necessary parameters at startup time?
- Wizard Function
With Rotamass TI , it is available to set interactively the minimum required parameters for operation start in an interactive manner. - Multiple Languages
Rotamass TI series supports not only English but also 11 languages in total: French, German, Italian, Spanish, Portuguese, Russian, Chinese, Polish, Kazakh and Japanese. This helps to prevent stress, misunderstandings, and parameter setting errors that occur when using languages that you are not familiar with. - Concentration Calculation
Rotamass TI combines mass flow measurement with an online and user-optimized Concentration Measurement function for suspensions, emulsions and solutions.
Pre-installed data sets support a convenient configuration for many different process fluids and can be adapted individually to the process characteristics.
As concentration measurements are highly reliant on temperature and density, Rotamass TI combines a precise coupled temperature measurement with different density calibration options. This allows high accurate and most reliable results.
Total Insight - Process Guard -
Operation & Observation
Have you ever wanted to know the inside condition of a product without removing it from the production line?
- Total Health Check Function
With Total Health Check, Rotamass TI offers an effective maintenance and diagnostic tool for a complete meter verification without disturbing your process.
With FieldMate software or any FDT/DTM 1.2, 2.0+ compliant software tool you can perform Total Health Check within few minutes and check: -
- Drive circuit
- Sensor circuit
- Temperature circuit
- Hardware and software
- Tube Health
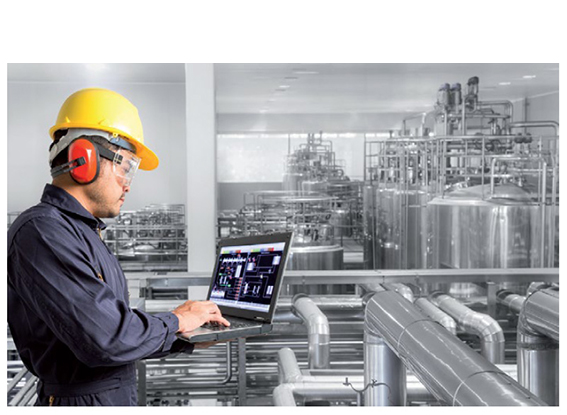
- Using Total Health Check makes it easy to determine the condition of the flowmeter, without disturbing running measurements, and to record the results in a verification report.
- Tube Health Check Function
This unique function detects stiffness changes of the measuring tubes, which can occur due to corrosion, abrasion or clogging.
This is of particular importance, because changed measuring tube stiffness is directly affecting the mass flow measurement.
The Tube Health Check is an in-line verification and can be individually adapted to your process conditions. -
- Frequency of checks (single or automatic test with predefined intervals)
- Definition of alarm levels
- Yokogawa’s FieldMate using DTM delivers a complete report and indicates a clear verification result
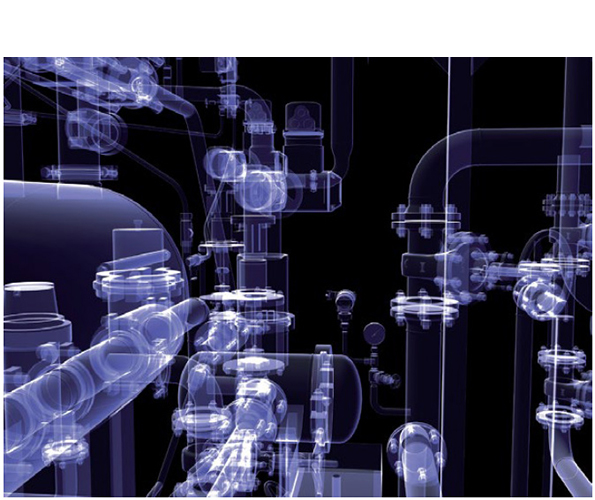
- Event Management
Rotamass TI can set the display, output signal, recording, and other operations for events such as alarms and warnings.
It is possible to record device data before and after the occurrence of an event such as an alarm, and to log the process value to the microSD with the occurrence of an event as a trigger.
In addition, events can be classified and set according to NAMUR NE107.
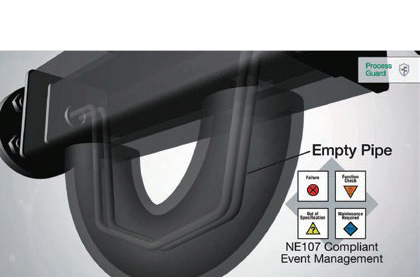
- Data Logging Function
Rotamass TI series can be equipped with a microSD card and can store process information.This makes it possible to record process information simply if there is a device itself. Also, data is stored in text format.
Therefore, analysis using spreadsheet software is also possible by importing data into a PC via a microSD card.
Total Insight - Expert Solution -
Utility & Maintenance
Have you ever taken the time to backup device parameters, copy parameters to replacement devices, etc?
- Data Mobility
Rotamass TI series is equipped with a microSD card and can store process information and Instruction manual, drawing , certification as user documents.
This makes it possible to record process information simply if there is a device itself. Also, data is stored in text format.
Therefore, analysis using spreadsheet software is also possible by importing data into a PC via a microSD card.
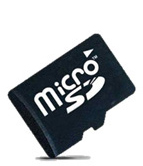
Flexibility Function
- Features on Demand
Market requirements and process conditions are changing. Features on Demand (FOD) contain valuable functions which can be activated at any time, even after installation and anywhere in the world: -
- Concentration measurement functions
- Net Oil Computing function
- Batching function
- Viscosity function
- Function for measurement of heat quantity
- Tube Health Check
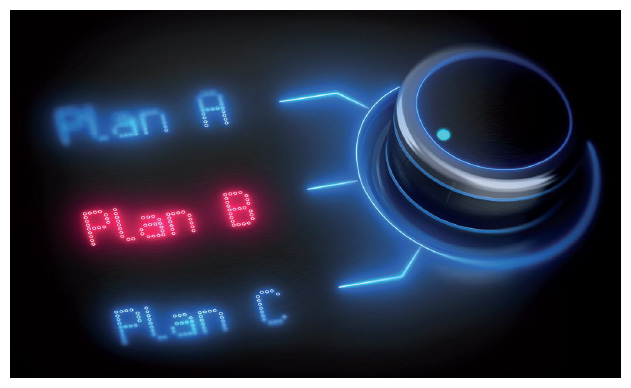
- Universal Power Supply
Thanks to its universal power supply Rotamass TI is ready to be effortlessly installed all over the world.
- Wide Range of I/O Combinations
The wide range of I/O combinations allows an individual configuration specific to your system.
- Short Face-to-Face Length
The short face-to-face length of our Coriolis flowmeter can be combined with customer specific installation length options.
- Dynamic Pressure Compensation
For applications with fluctuations in pressure a dynamic compensation is important to keep accurate and reliable mass flow measurement or gas volume measurement based on density calculation.
With Rotamass TI and the Dynamic Pressure Compensation function you can benefit from continuous and highly accurate results.
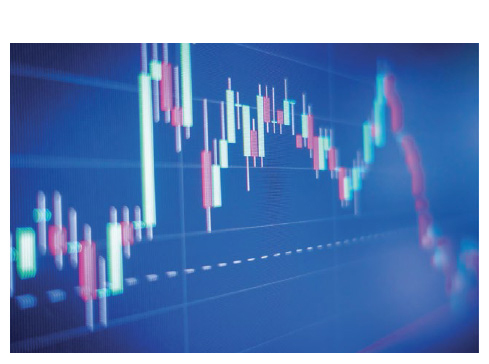
Technical Information
Sensor Structure
- Box-in-Box
Optimum decoupling of core measuring element from external influences by proven box-in-box design.
- Heat Trace Jacket
Supported by robust and durable sensor design, our factory-fitted insulation and heat tracing solutions offer perfect insulation, continuous heating along the entire flow path and purging of the heating fluid. This is enabling to handle high temperature, viscous process fluids or molten fluids like sulfur.
Ethernet-APL
Industry 4.0 as Origin of Ethernet-APL
Industry 4.0 is a transformative concept that aims to revolutionize manufacturing originated from German government’s strategy. By leveraging digitalization, automation, and data-driven processes, Industry 4.0 seeks to enhance productivity and achieve efficient manufacturing. Ethernet-APL is key technology to access necessary field data smoothly.
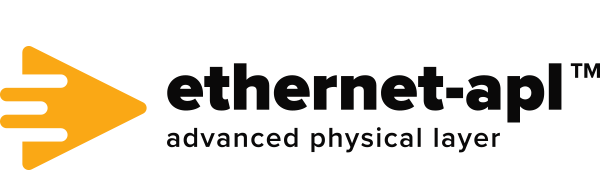
- Smart Factories
- Internet of Things (IoT)
- Cloud Computing
- Big Data and Analytics
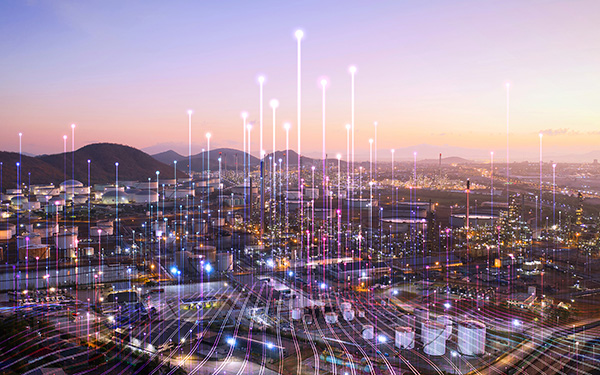
Features of Ethernet-APL
As for realization of industry 4.0, Ethernet-APL is a cutting-edge technology designed for process automation with hazardous environments.
- Two-Wire Ethernet Cable
Ethernet-APL enables direct connection of devices and sensors in hazardous areas using a two-wire Ethernet cable. This technology extends the capabilities of traditional Ethernet by allowing data exchange over just two wires, simplifying installation and maintenance. - Intrinsic Safety of Explosion Proof
Ethernet-APL complies with intrinsic safety requirements, making it suitable for use in explosive atmospheres (Zone 0, 1, and 2). - Direct Integration with IoT
With Ethernet-APL, field devices connect directly to Ethernet-based systems, eliminating the need for complex gateway solutions. It serves as an economic foundation for Industrial Internet of Things (IIoT) in process automation. - Interoperability
Different manufacturers’ equipment and systems can interoperate within an Ethernet-APL network. - Big Data and Analytics
Ethernet-APL captures and analyzes large amounts of additional data (big data), enabling predictive maintenance and other innovative solutions to improve availability. - Long Cable Length
APL supports two common types of segments: boot and spur. Boots provide high-power signals up to 1000 meters, while spurs provide low-power signals up to 200 meters. - Transmission Speed
10 MBit/s, full duplex communication speed, 300 times faster than existing communication protocols such as HART and Fieldbus. - Reuse Existing Cabling
By utilizing existing cable infrastructure, Ethernet-APL allows cost-effective system upgrades. It works seamlessly with established Ethernet protocols like EtherNet/IP™, HART IP, OPC UA, and PROFINET.
Example Topology for Long Cable Reach with up to 1000 m between switches on the Trunk
Image Zoom
* Trunk and Spur
Trunk is the main line of infrastructure. It connects to infrastructure devices like APL field switches using the 2.4Vp-p mode of 10BASE-T1L and can communicate over distances of up to 1000m with power supply.
Spur connects the infrastructure device to the Field device. It connects between infrastructure device and field device using the 1.0 Vp-p mode of -T1L, and can communicate over a distance of up to 200 m with power supply.
Benefit of Ethernet-APL
Ethernet-APL (Advanced Physical Layer) offers several benefits for end users in the process industry.
- Simplified Network Configuration
Ethernet-APL significantly reduces the effort required for network configuration. It streamlines the process of setting up communication between devices, making it easier for both IT and OT teams to manage. - Unified Troubleshooting Tools
With Ethernet-APL, the same troubleshooting tools can be used across both IT and OT domains. This consistency simplifies diagnostics and maintenance, enhancing overall efficiency. - Minimal Installation Time and Cost
The deployment of Ethernet-APL is straightforward, resulting in minimal installation time and associated costs. This is especially beneficial for large-scale process plants. - Effective Integration
Ethernet-APL seamlessly integrates various processes by enabling communication between control systems and field devices. It facilitates the exchange of process variables, secondary parameters, and asset health feedback over long distances.
Networking the Entire Automation Pyramid
Image Zoom
Application Example for Non-explosive Atmosphere
As the example of Non-explosive, the source power class C (field switch spur port) can be combined with spur (load) port classes A, B, or C of the field devices with the following conditions.
- Maximum cable length for all spurs.
- APL field devices are only connected to the spur ports of the APL field switches.
- Tunk_in ports are only connected to Trunk_out ports.
- The field-switch fits the power demand of the connected APL field devices.
* Power class
Power class A: Maximum voltage 15VDC, Minimum output power 0.54W
Power class C: Maximum voltage 15VDC, Minimum output power 1.1W
Rotamass TI Ethernet-APL Specification
ROTAMASS Total Insight offers the following PROFINET over Ethernet-APL functionalities.
- Port profile class: SLAA for Ethernet-APL
Rotamass Total Insight offers the SLAA port profile class. - PROFINET Conformance Class B Compliant
PROFINET provides real time and acyclic real time communication with support of standard TCP/IP, Alarms/Diagnostics and Network Topology. And Conformance Class B adds in simple network management protocol (SNMP) support. - PA Profile 4.0 with Function Blocks
Rotamass Total Insight offers the function blocks of six Analog input function blocks, three Totalizer function blocks and one Analog Output function block. The PA Profile 4.0 has common functionality regardless of device manufacturer and therefore user can operate/control the field device without special handling each manufacture. - S2 Redundancy
System redundancy for PROFINET can be supported. This is the concept of multiple connections to a field device or controller to maintain the system in case of failure event. Rotamass Total Insight offers S2 redundancy. This function contributes to the reduction of downtime. - Web Server
Rotamass Total Insight provides Web server functionality and the field device parameters from Web browser can be configured. As standard Web browser such as Google Chrome and Microsoft Edge can be used to access Web server, the parameters can be configured without handheld terminal and/or any dedicated tool.
- FDI Device Package with PA-DIM
The description of PA-DIM (Process Automation Device Information Model) is available in FDI Device Package for Rotamass Total Insight. It provides standard parameter set each kind of device such as pressure, temperature, flow, level etc. and therefore user easily can access only necessary parameters in field device by the same software/procedure regardless of device manufacturer.
Resources
A milk tanker is typically fitted with a pump and flowmeter that records the volume of milk loaded from each individual farm. Confirmation of the total volume of milk delivered to the dairy plant is performed either by weighing the tanker or via flowmeters in the tanker bays.
Avoid flashing issues while loading cryogenic liquids with safe, reliable, and accurate density fluid measurements utilizing Yokogawa’s industry-leading Coriolis flowmeter to eliminate measurement issues and increase the accuracy of inventory.
Challenge: The customer's existing measurement device was disturbed by vibration and could not be compensated or corrected by the product that was installed.
Precision flow control for high-purity semiconductor materials with Yokogawa's ROTAMASS TI Coriolis Flowmeter, providing a maintenance-free and durable performance solution for photosensitive materials production.
In this application, the customer’s facility was using petroleum-fired generation and required a reliable and accurate flow measurement technology to measure the fuel flow required to run the turbines. The fuel flow to the turbine was to be measured and compared to the power generated by the turbine in megawatts, which would be the direct indication of the power generation efficiency, known as the plant settlement system application.
Accurate and reliable measurement of wash oil in a high temperature process to avoid solidification of the chemical, it is essential to adjoin heat and insulation to the piping and equipment. Therefore, thermal management of the pipe runs is required, to avoid any heat loss in the fluid to maintain the fluid properties.
The process consists of mixing meats, oils, and water to create a finished product, animal feed, using a PLC-based automation system.
Accurate measurement of the oil concentration would allow the heat/steam to be adjusted. Increases efficiency and saves money.
In the food and beverage industry, government regulations for whisky production require compliance of distillation strengths to strict limits. Yokogawa’s ROTAMASS TI Coriolis mass flowmeter is well-matched for the application with its density calibration for ethanol or water percentage and a special calibration for maximum accuracy and stability. The mass flow meter’s dual bent tube technology and advanced software enabled the customer to measure the very small and sensitive range required. Yokogawa commissioned the mass flowmeter onsite to ensure the correct installation and commissioning from the outset, affording Total Insight through the entire product lifecycle.
Accurate tracking of a facility's intake and output is needed as multiple state and federal agencies and environmental programs are involved. Since re-refined oil is considered a renewable resource it qualifies for various state and federal energy credits or pollution programs, so accurate accounting is critical.
A Basic Guide to Accurate & Reliable Flow Measurement.
Smart devices, like Yokogawa’s line of Total Insight transmitters and flowmeters contribute to Digital Transformation during operations and throughout the lifecycle of the instrument.
Thanks to a two year upgrade project, Foster's Yatala brewery is now one of the country's most efficient integrated brewing and packaging operations. More than 1,100 measurement and control devices from instrument manufacturer Yokogawa Australia will help keep it that way.
View TechStar Blog
Downloads
Brochures
- Bulletin Rotamass Total Insight (6.7 MB)
- Yokogawa in the Food and Beverage Industry (5.9 MB)
- Coriolis Mass Flowmeter - ROTAMASS Total Insight (2.3 MB)
- Application for the Marine industry (6.0 MB)
- Yokogawa Performance Blending Solution
- ROTAMASS TI Hygienic Series for Food and Beverage Solutions (5.8 MB)
- Yokogawa Performance Distillation Solutions
- Refining Solutions (12.5 MB)
- Steam Methane Reformer for Methanol Production
- Five Mistakes When Selecting a Flowmeter (439.6 KB)
- Electrolysis Solutions: Instrumentation Solutions for Electrolysis Plant Applications (841.1 KB)
- Brochure: Five Mistakes When Selecting a Flowmeter
Instruction Manuals
- Quick Reference Instruction Manual ROTAMASS TI Coriolis Mass Flow Meter *See IM 01U10B00-11EN-R (4.0 MB)
- Quick Reference Instruction Manual for Spare ROTAMASS TI Coriolis Mass Flow Meter *See IM 01U10B00-11EN-R (3.1 MB)
- General Instruction Manual ROTAMASS TI Coriolis Mass Flow Meter *See IM 01U10B00-11EN-R (7.6 MB)
- ROTAMASS Total Insight - Addendum to Instruction Manuals for NTEP custody transfer (515.0 KB)
- IM 01U10B00-11EN-R (375 KB)
- Safety Manual (SIS) ROTAMASS TI Coriolis Mass Flow Meter (1.3 MB)
- Ex IM ATEX ROTAMASS TI Rotamass Coriolis Mass Flow Meter (4.1 MB)
- Ex IM IECEx ROTAMASS TI Rotamass Coriolis Mass Flow Meter (3.0 MB)
- Ex IM FM ROTAMASS TI Rotamass Coriolis Mass Flow Meter (5.2 MB)
- Ex IM INMETRO ROTAMASS TI Coriolis Mass Flow Meter (2.6 MB)
- Ex IM PESO ROTAMASS TI Coriolis Mass Flow Meter (1.2 MB)
- Software IM (HART) ROTAMASS TI Coriolis Mass Flow Meter (9.8 MB)
- Software IM (MODBUS) ROTAMASS TI Coriolis Mass Flow Meter (9.8 MB)
- Software IM (FOUNDATION FIELDBUS) ROTAMASS TI Coriolis Mass Flow Meter (7.3 MB)
- Software IM (PROFINET over Ethernet-APL) ROTAMASS TI Coriolis Mass Flow Meter (8.9 MB)
- Software IM (PROFIBUS PA) ROTAMASS TI Coriolis Mass Flow Meter (6.0 MB)
General Specifications
- ROTAMASS TI, Coriolis Mass Flow Meter, Specification Overview (21.9 MB)
- ROTAMASS TI, Rotamass Nano Coriolis Mass Flow Meter (3.1 MB)
- ROTAMASS TI, Rotamass Prime Coriolis Mass Flow Meter (3.1 MB)
- ROTAMASS TI, Rotamass Hygienic Coriolis Mass Flow Meter (4.0 MB)
- ROTAMASS Total Insight - Addendum to General Specifications for NTEP (255.4 KB)
- ROTAMASS TI, Rotamass Supreme Coriolis Mass Flow Meter (3.7 MB)
- ROTAMASS TI, Rotamass Universal Spare Transmitter (2.5 MB)
- ROTAMASS TI, Rotamass Intense Coriolis Mass Flow Meter (7.5 MB)
- ROTAMASS TI, Rotamass Giga Coriolis Mass Flow Meter (5.5 MB)
- Addendum to General Specifications for PROFIBUS PA (1.3 MB)
- Addendum to General Specifications for FOUNDATION Fieldbus (1.3 MB)
- Addendum to General Specifications for Marine options, ROTAMASS TI, Coriolis Mass Flow Meter (1.3 MB)
- Addendum to General Specifications (651.0 KB)
- Addendum to General Specifications for PROFINET over APL, ROTAMASS TI, Coriolis Mass Flow Meter (365 KB)
- Addendum to General Specifications for Coating Change, ROTAMASS TI, Coriolis Mass Flow Meter (200.5 KB)
- Addendum to General Specifications to ed. 6, ROTAMASS TI, Coriolis Mass Flow Meter (1.5 MB)
Software
- Fieldbus DD/CF file - ROTAMASS Total Insight Coriolis Mass Flow Meter
- PROFIBUS GSD/EDD file - ROTAMASS TI GSD file
- PROFIBUS GSD/EDD file - ROTAMASS TI EDD file
- PROFINET GSDML file - ROTAMASS TI Rev.1
- PROFINET GSDML file - ROTAMASS TI Rev.2
- PROFINET FDI Device package file - ROTAMASS TI Rev. 2
- Yokogawa DTM FOUNDATION Fieldbus
- Yokogawa DTM HART
- Yokogawa DTM PROFIBUS
Technical Information
Videos
Discover how Yokogawa’s Total Insight Flowmeters with Process Guard transform operational safety and efficiency. In this video, we highlight its advanced capabilities in monitoring, diagnostics, and proactive intervention to minimize risks and maximize uptime.
2D/3D Configurator
Looking for more information on our people, technology and solutions?
Contact Us