How automated real-time noise map can contribute to production efficiency
1. Noise map today:
The most common instrument used for measuring noise level in plants is the handheld sound level meter. Based on the measured noise levels at different locations by the handheld sound level meter, paper noise maps which are being updated every 4 - 6 years are manually created. Actual noise levels could vary significantly between the points in time when these manual readings were made, depending on factors such as the status of the plant equipment and the time of day.
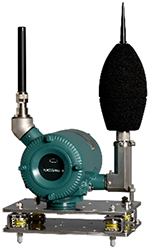
2. Challenges today:
Since paper noise maps are not able to reflect changes in noise levels each time, creating accurate noise maps is challenging, if possible, with current common practice.
However, inaccurate noise maps will affect HSE compliance, which means workers will be exposed to unexpected higher noise levels with the potential to cause critical incidents such as hearing impairments. Also, an inaccurate noise map will decrease production efficiency.
In the O&G industry, workers must comply with governmental noise regulations to ensure the daily noise exposure. The noisier the workplace, the shorter the working hours.
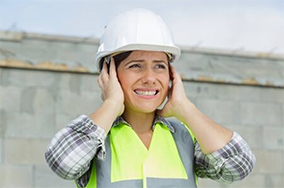
Together with Equinor ASA Norway, we developed a real-time noise level monitoring system. With Yokogawa’s field wireless technology expertise and Equinor’s extensive plant operations knowledge, we were able to develop the wireless noise surveillance system.
What are the issues caused by an inaccurate noise map? Let’s see what we found through our case study.
3. Case Study with Equinor:
Yokogawa and Equinor jointly conducted a field test in a specific area of an operating offshore facility. The below 2 pictures show the result of the test.
Comparing the above 2 noise maps, there are huge gaps in the sound noise level. The gaps are almost 5 dBA.
According to the noise regulations, 6 hours is the maximum number of work hours under the noise levels between 90 and 95 dBA, but it is 12 hours under the noise levels between 85 and 90dBA.
It means that you can increase the time to visit your plant up to 2,190 hours (6 hours x 365days) in a year. This might be an exaggerated estimation, but you can imagine how much you can optimize OPEX!
Due to the fact paper noise maps do not detect unexpected higher noise levels, you can easily imagine how much danger you are expected to be exposed to.
Our wireless noise surveillance system was developed not only to improve HSE issues, it also helps to find abnormal conditions of equipment in the noise map area.
Industrias Relacionadas
-
Power
In the mid 1970s, Yokogawa entered the power business with the release of the EBS Electric Control System. Since then, Yokogawa has steadfastly continued with the development of our technologies and capabilities for providing the best services and solutions to our customers worldwide.
Yokogawa has operated the global power solutions network to play a more active role in the dynamic global power market. This has allowed closer teamwork within Yokogawa, bringing together our global resources and industry know-how. Yokogawa's power industry experts work together to bring each customer the solution that best suits their sophisticated requirements.
-
Water & Wastewater
Water resources are finite, and therefore contributing to a sustainable water cycle is one of the Sustainable Development Goals (SDGs). Yokogawa has been providing advanced digital control solutions for the stable supply of clean and safe water, wastewater treatment for protecting the water environment, water loss management and optimization of plant operation for reducing CO2 emissions and running costs. With our leading-edge technologies, dependable products and extensive expertise and experience of diverse water projects around the world, we work with you to provide sustainable water solutions that boost your business and add value throughout the plant lifecycle.
Yokogawa supports a wide range of water control applications in both the municipal and industrial water markets.
-
Oil & Gas
Yokogawa has a wealth of experience in every part of the oil and gas business, from offshore and onshore facilities to pipelines, terminals, and deepwater operations. We provide solutions that enhance safety, ensure accurate and reliable operation, and increase plant efficiency.
-
Oil & Gas Downstream
The oil & gas downstream industry has been facing an increasing number of challenges in recent years. These include the changing characteristics of the feedstock to be processed, aging of process facilities and equipment, rising cost of energy, lack of skilled plant operators who can run a refinery safely and efficiently, and the ever-changing requirements from both the market and the customer.
Over the years, Yokogawa has partnered with many downstream companies to provide industrial solutions focused on solving these challenges and problems. Yokogawa's VigilantPlant solutions have helped plant owners to achieve maximum profitability and sustainable safety within their plants.
-
Chemical
Chemical plants rely on continuous and batch production processes, each posing different requirements for a control system. A continuous process calls for a robust and stable control system that will not fail and cause the shutdown of a production line, whereas the emphasis with a batch process is on having a control system that allows great flexibility in making adjustments to formulas, procedures, and the like. Both kinds of systems need to be managed in available quality history of product, and to be able to execute non-routine operations. With its extensive product portfolio, experienced systems engineers, and global sales and service network, Yokogawa has a solution for every plant process.
-
LNG Supply Chain
YOKOGAWA has been engaging in LNG automation by supplying the latest sensors, analyzers, control and information systems for more than 50 years since LNG was first imported to Japan. YOKOGAWA is one of the biggest automation suppliers to the worldwide LNG supply chain, liquefaction, transportation, and regasification.
-
Pulp & Paper
The paper and pulp industry is highly competitive and must meet ever-changing market needs. Yokogawa helps realize energy-efficient plants which are globally sustainable.
-
Food & Beverage
At Yokogawa, we understand that today’s food and beverage companies face unprecedented challenges in climate change, consumer demand, and increased global competitiveness. Overcoming these challenges will require innovative solutions that focus on key areas of production, asset management, and food safety and quality.
-
Iron & Steel
In the iron and steel industry, it is crucial to improve the quality of not only products but also manufacturing and operation technologies, as well as to address environmental and energy-efficiency issues. Yokogawa helps customers to create the ideal plant and evolves with them for mutual growth.
Productos y Soluciones Relacionadas
-
Wireless Noise Surveillance System
Wireless Noise Surveillance System is a real-time noise monitoring and mapping system. Monitoring the noise in real time can achieve the optimization of working time. This system also contributes to the SDGs by improving HSE of workers and ensuring acceptable noise levels in the workplaces.